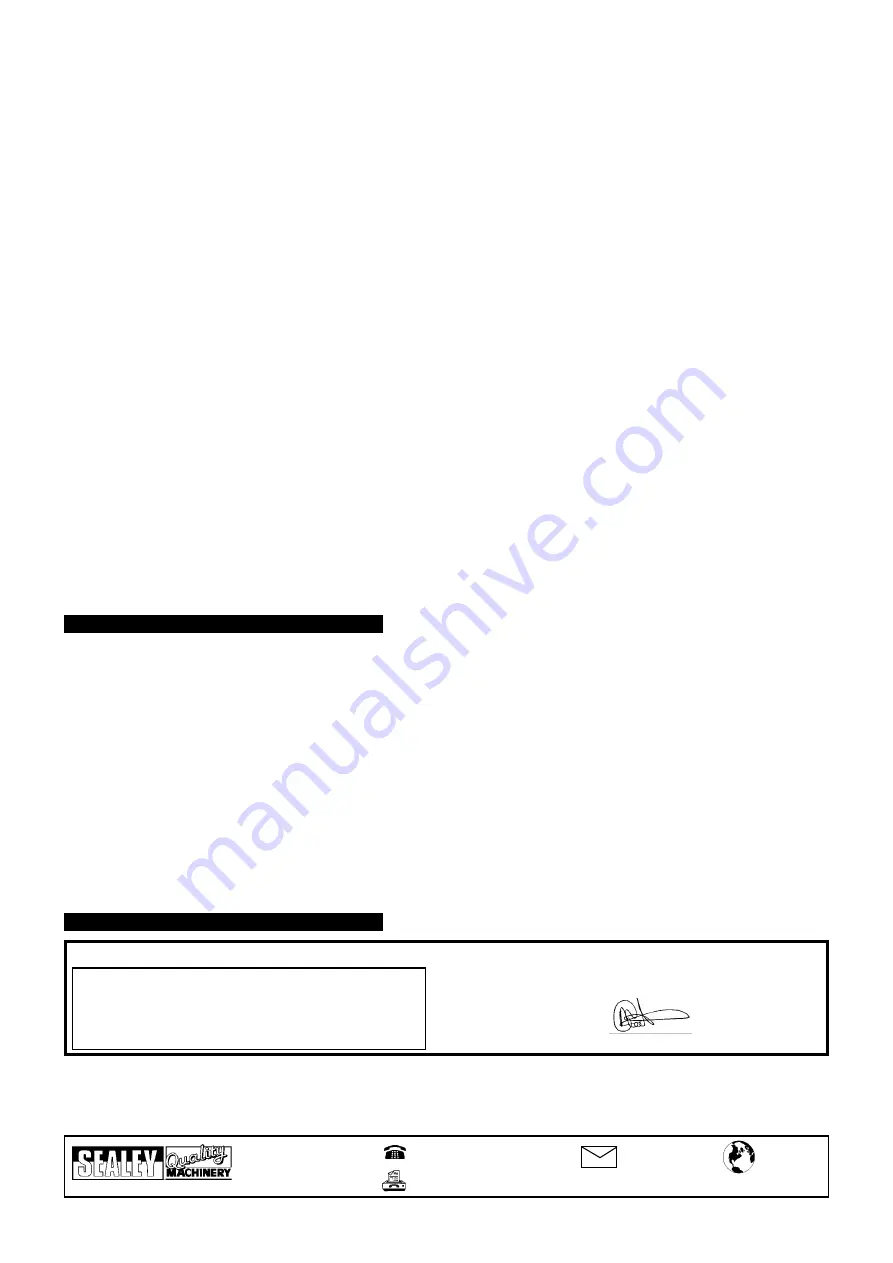
For Jack Sealey Ltd. Sole UK importer of Sealey Quality Machinery.
NOTE:
It is our policy to continually improve products and as such we reserve the right to alter data, specifications and component parts without prior notice.
IMPORTANT:
No liability is accepted for incorrect use of this equipment.
WARRANTY:
Guarantee is 12 months from purchase date, proof of which will be required for any claim.
INFORMATION:
For a copy of our latest catalogue and promotions call us on 01284 757525 and leave your full name and address, including postcode.
Declaration of Conformity
We, the sole UK importer, declare that the product listed below is in conformity with the following standards and directives.
The construction file for this product is held by the Manufacturer and may be
inspected, by a national authority, upon request to Jack Sealey Ltd.
GAS WELDING/CUTTING KIT
Model: SGA1
BS EN ISO 730:1995 Gas Welding Equipment - Safety Device
Incorporating Flame/Flashback Arrestor .
BS EN ISO 5172:1997 Manual blowpipes for welding, cutting and heating
Signed by Mark Sweetman
6th August 2003
3.1.6. Connect the correct hose to each regulator.
BLUE
to
OXYGEN
and
RED
to
ACETYLENE
. Tighten nuts securely with wrench. If any
sign of oil or grease is found, discontinue use immediately.
3.1.7. Blowing out hoses. Perform this on one hose at a time and in a well ventilated area, otherwise you may create conditions for fire or explosion.
a.Turn the oxygen regulator adjusting screw to allow 5psi to pass through hose.
b.Allow oxygen to flow approximately 10 seconds to purge the hose.
c. Repeat the above steps for acetylene hose.
Note: New hoses contain a preservative powder which must be blown out before use.
3.1.8. Connect the two hoses to the respective connections on the torch handle.
p
WARNING!
If traces of oil or grease are found,
DO NOT
use. Contact your gas supplier immediately.
3.1.9. Always use reverse flow check valves on torch handles.
3.1.10. Always connect welding tip or cutting attachment to torch handle. Always check seal, coupling nut and torch head for damage or oil.
If either is found, discontinue use and contact your supplier.
p
WARNING!
The teflon seal on the torch inlet must not be damaged or missing, otherwise gases will mix inside the torch and result in
flashbacks or backfires.
3.1.11. Check connections for leaks. Adjust the regulators to normal operating pressure and, using an approved leak detection solution, check for
leaks at hose and check valve connections. If a leak is found, tighten nut more securely. If leak persists, discontinue use and call your supplier.
p
WARNING!
Never set acetylene regulator at a delivery pressure above 15psi (1 bar).
3.1.12. Neutral flame adjusting
a.Refer to welding tip or cutting nozzle chart to determine the proper regulator pressures.
b.Open oxygen valve on the torch handle (and preheat oxygen valve on cutting attachment). Adjust the oxygen regulator to the desired
working pressure, and then close the oxygen valve.
c. Open acetylene valve on the torch handle, adjust the acetylene regulator to the desired working pressure. Then close the acetylene valve.
d.Hold torch in one hand and spark lighter in the other.
e.Open the acetylene torch valve about 1/4 turn and ignite the acetylene gas coming out of the tip.
p
WARNING!
Always point torch away from person when lighting.
f. Turn on the acetylene torch valve slowly until smoke subsides and the flame jumps away from the end of the tip slightly.
g.Slowly open the oxygen valve until a brilliant neutral flame is reached.
p
WARNING!
Always use goggles or eye protection when welding or cutting.
3.2.
Shutting down and leaving safe
3.2.1. Turn off the acetylene valve on the torch and
then
turn off the oxygen valve on the torch.
Note: Reversal of this procedure can cause damage to the torch.
3.2.2. Close both cylinder valves.
3.2.3. Drain gas from oxygen regulator by opening the oxygen valve on the torch handle. Similarly drain gas from the acetylene regulator.
3.2.4. Release adjusting screws on regulators. This is done by turning them anti-clockwise.
4.1.
CUTTING CAPACITIES
Mild
Nozzle
Operating Pressure (bar - lbf/in²)
Gas Consumption (ltr/m - ft³/h)
Steel
Size
Oxygen
Acetylene
O2 - Cutting
O2 - Heating
Acetylene
6mm / 1/4
1/32
1.4 - 20
0.30 - 4
14.15 - 30
8.5 - 18
8.0 - 17
13mm / 1/2
3/64
2.1 - 30
0.35 - 5
30.70 - 65
10.4 - 22
9.4 - 20
25mm / 1
1/16
2.8 - 40
0.40 - 6
67.50 - 143
13.2 - 28
11.8 - 25
50mm / 2
1/16
3.1 - 45
0.40 - 6
78.30 - 166
13.2 - 28
11.8 - 25
75mm / 3
1/16
3.5 - 50
0.40 - 6
88.70 - 188
13.2 - 28
11.8 - 25
4.2.
WELDING CAPACITIES
Mild
Nozzle
Operating Pressure (bar - lbf/in²)
Gas Consumption (ltr/m - ft³/h)
Steel
Size
Oxygen
Acetylene
O2 - Welding
O2 - Heating
Acetylene
1.2mm / 18SWG
LW02
0.14 - 2
0.14 - 2
11.8 - 25
4.2 - 9
3.8 - 8
2.6mm / 12SWG
LW05
0.28 - 4
0.21 - 3
23.5 - 50
4.2 - 9
3.8 - 8
4mm / 8SWG
LW10
0.35 - 5
0.28 - 4
56.6 - 120
4.2 - 9
3.8 - 8
4. TECHNICAL INFORMATION
5. DECLARATION OF CONFORMITY
01284 757500
01284 703534
www.sealey.co.uk
Sole UK Distributor,
Sealey Group,
Bury St. Edmunds, Suffolk.
Web
SGA1 - 3 - 060803