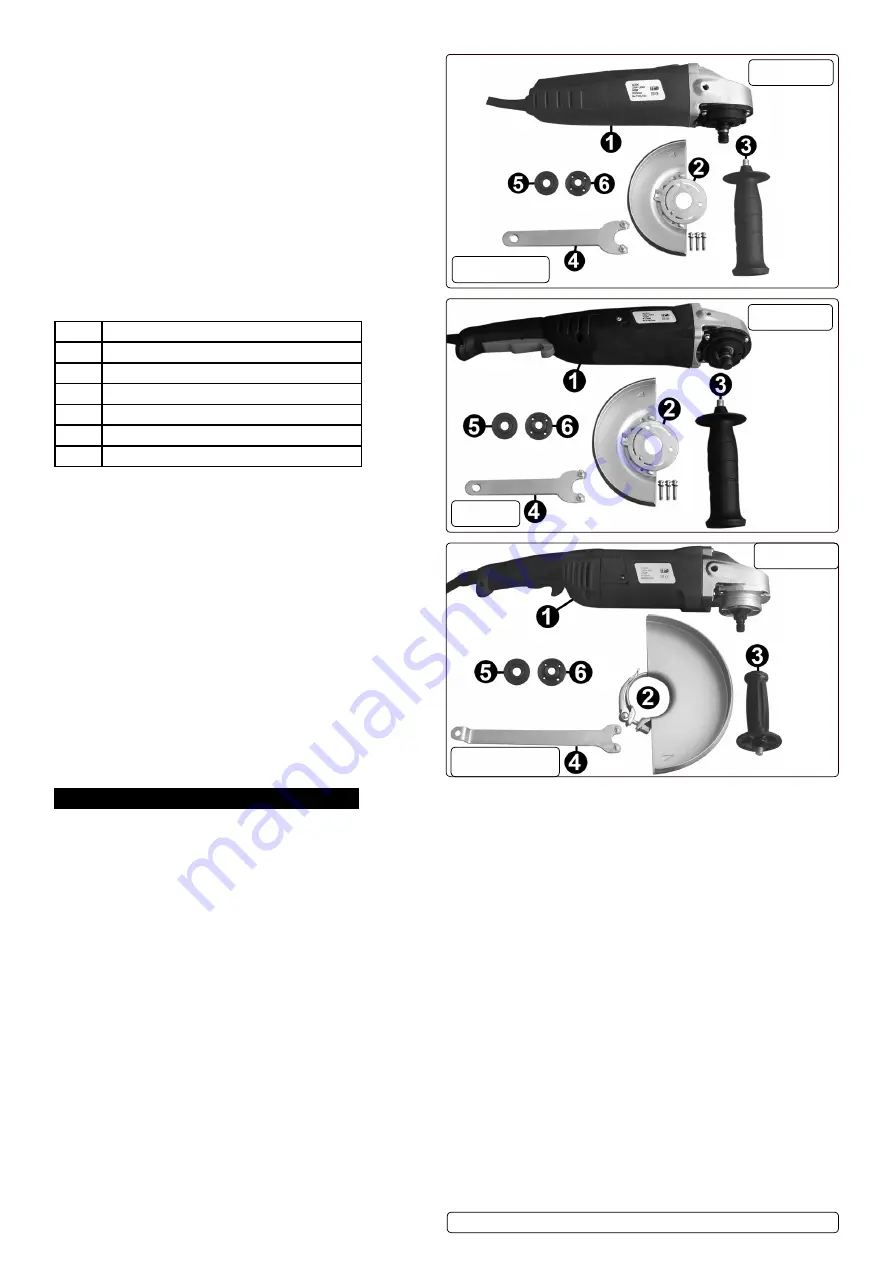
model ..........................................................................SG125
Power input ................................................................... 1000W
no-load speed ...........................................................11000rpm
Spindle Size .......................................................................m14
Grinding/cutting disc max. dia. ......................................125mm
Sound Pressure/power level ................................ 90/101dB(A)
Weight ..............................................................................2.4kg
model ...................................................................SG2303.V2
Power input ................................................................... 2000W
no-load speed ............................................................ 6000rpm
Spindle Size .......................................................................m14
Grinding/cutting disc max. dia. ......................................230mm
Sound Pressure/power level ................................ 94/105dB(A)
Weight ..............................................................................1.8kg
Item
description
1
main Unit
2
S
afety Guard c/w fixing
3
Handle
4
Pin Wrench
5
Clamping Flange
6
Flange nut
4. ASSEMbLy
WARNING!
ensure that the grinder is unplugged from the power supply before assembly.
4.1.
fitting the Guard Assembly. (SG101.V2)
4.1.1.
The guard may be orientated at any angle to suit the grinding task required and should be positioned to allow maximum working
performance whilst providing maximum personal protection for the operator.
4.1.2.
loosen locking screw and turn the guard to the required position. lock the guard in place by re-tightening the locking screw.
4.2.
fitting the Guard Assembly. (SG115.V2, SG125)
4.2.1.
The guard may be orientated at any angle to suit the grinding task required and should be positioned to allow maximum working
performance whilst providing maximum personal protection for the operator.
4.2.2.
Take the guard and place it around the spindle as in fig.4, place the securing plate (fig.4B) around the spindle and line up the
holes in the plate with the holes in the main unit as in fig.4 and secure with screws (fig.4A).
4.3.
fitting the Guard Assembly. (SG2303.V2)
4.3.1.
The guard may be orientated at any angle to suit the grinding task required and should be positioned to allow maximum working
performance whilst providing maximum personal protection for the operator.
4.3.2.
Take the guard (fig.1 item 2) and unlock the clamp. on the inside of the guard clamping collar is a small pip (indicated by arrow ‘A’ in fig.5)
which must be aligned with a notch in the housing (also indicated by arrow ‘A’). orientate the guard as shown in fig.5 and place it over the
central spindle and onto the housing. leaving the clamp open, rotate the guard on the housing until it is over the main body of the tool as
indicated in fig.3.
4.3.3.
lock the guard in place by pushing the clamp lever towards the centre spindle as shown in fig.3.
4.4.
Attaching a Grinding/Cutting Disc.
(discs should only be fitted by a person holding a grinding wheel certificate).
4.4.1.
lay the grinder on it’s back and place the clamping flange onto the centre spindle with the
raised ring facing upwards (see fig.2 item 5). Rotate the clamping flange on the spindle until the flats on its back face drop into
alignment with the flats on the spindle. When the clamping flange is in the correct position it can no longer be rotated on the spindle.
4.4.2.
Place the grinding (or cutting) disc over the spindle and onto the clamping flange. fg8A , fig8B, fig8C section 6. ConSUmABleS
shows the correct orientation of the retaining flange nut for the different types of disc.
fig.1B
SG115.V2
fig.1C
fig.1D
SG125
SG2303.V2
SG101.V2, SG115.V2, SG125, SG2303.V2 Issue 5 (1,3) 02/05/18
Original Language Version
© Jack Sealey limited