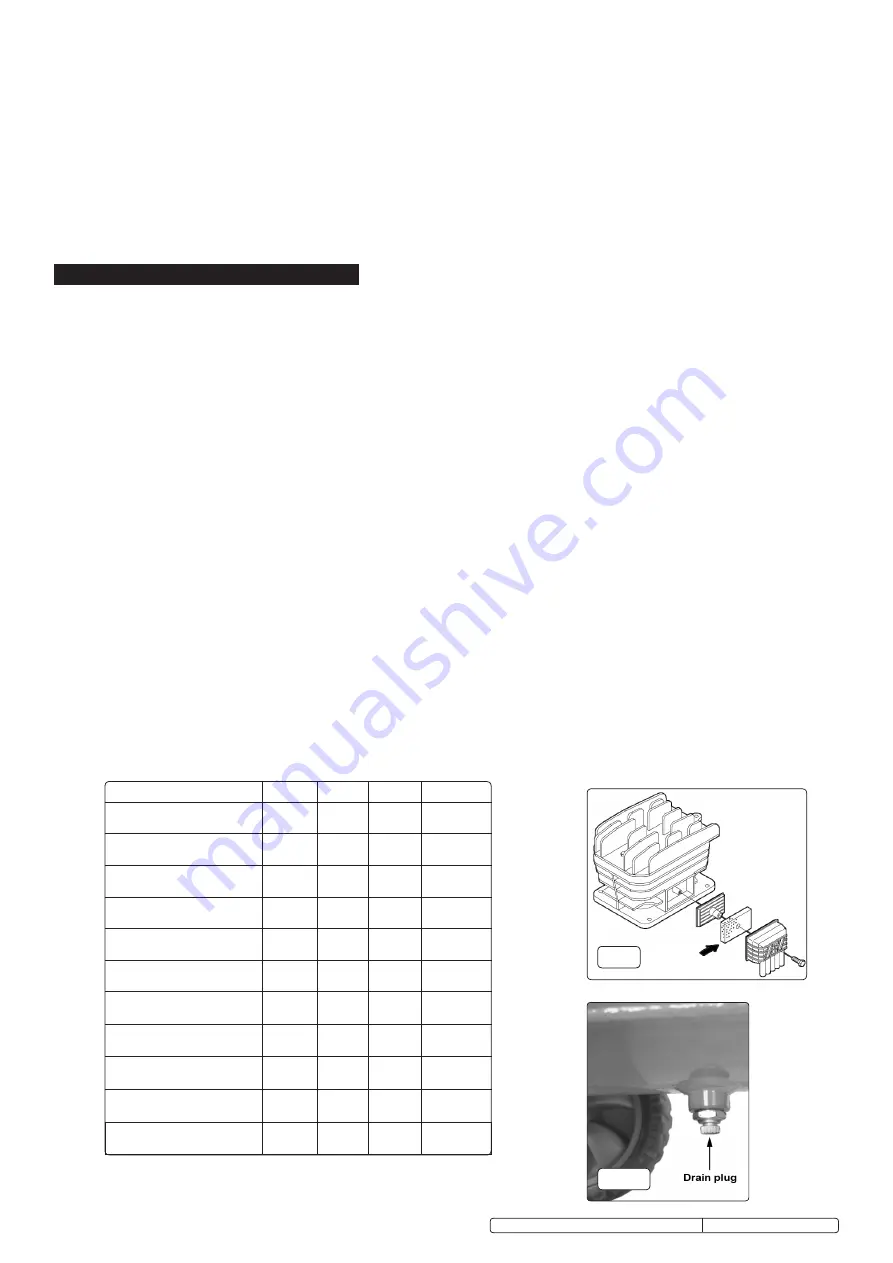
Original Language Version
© Jack Sealey Limited
off the mains socket, or by pulling the plug out, as the pressure relief will not then operate and motor damage may result upon restart.
5.1.6.
The motor of the compressor is fitted with a thermal breaker located in the housing on top of the motor. The manual resetting button is
located in the end of the housing as shown in fig.10A. When the breaker is tripped, wait for a few minutes and then press the reset button.
5.1.7.
On Models SAC1503B and SAC1103B, the output pressure is regulated by the pressure regulator (fig.6.2). Turn the knob clockwise
to increase pressure and anti-clockwise to reduce it. Lock knob in position at required pressure with locking ring. To determine the correct
working pressure for any piece of equipment check the corresponding manual. When the compressor is not being used, set the regulated
pressure to zero so as to avoid damaging the pressure regulator.
NOTE:
a) If the motor does not cut in and out, but runs continuously when using an air appliance, the capacity of the compressor may be too
small for the equipment or tool.
b)The gauge (figs.6.5 and 7.5) indicates the pressure inside the main tank,
NOT
the pressure supplied to the air equipment.
Should the pressure in the main tank exceed the pre-set switch maximum, the safety valve will activate.
WARNING!
For this reason
DO NOT
tamper with, or adjust, the switch or safety valve.
6. MAINTENANCE
6.1.
In order to keep the compressor in good working condition, periodic maintenance is essential.
IMPORTANT!
Failure to carry out maintenance tasks may invalidate the warranty on your compressor.
WARNING!
Before performing any maintenance operation, switch off the compressor, disconnect from electricity supply and release all
air from the tank (except for 5.3.a)
6.2.
Operations to be carried out after the first 50 working hours:
a)
Check that all bolts/nuts are tight, particularly those retaining the crankcase and cylinder head.
b) Replace the lubricating oil - see para 5.5.
6.3.
Operations to be carried out weekly:
a) Drain condensation by opening the valve located under the tank (fig.9). Place a container under the valve and open the valve
by turning anti-clockwise.
WARNING!
Take care if there is still pressure inside the cylinder as water could flow out with considerable force. Recommended
pressure 1 - 2bar max.
b) Check oil level and, if necessary, top up.
6.4.
Operations to be carried out every 50 hours (or more frequently, if the compressor operates in a very dusty atmosphere):
a)
Remove the air filter element (fig.8). Using stored air from the compressor’s tank, clean the filter with compressed air. (Wear
eye protection and
DO NOT
direct air towards the body or hands).
DO NOT
operate the compressor without the filter as foreign bodies
or dust could seriously damage the pump. Replace the filter element and air filter housing.
b) Check for oil leaks.
6.5.
Operations to be carried out every 100 hours:
a)Check the automatic cut-out at max. pressure and the automatic cut-in at 2bar below.
6.6.
Operations to be carried out every 400 hours:
a) Replace the lubricating oil. For oil specifications see 6.8.
Remove the filler/breather plug (see fig.4) then remove oil drain plug, draining the oil into a container. Drain when the compressor is hot
so that the oil drains rapidly and completely. Incline compressor to ensure complete drainage. Replace oil drain plug and refill through
the filler/breather aperture.
DO NOT
overfill. Replace plug.
WARNING!
Never mix different oils and
DO NOT
use non-detergent/low quality oils as the compressor may be damaged.
WARNING!
Dispose of waste oil only in accordance with local authority requirements.
b) Replace air filter. (See fig.8)
c) Check all tube fittings and electrical connections.
d) Inspect pressure tank inside and out for damage or corrosion.
6.7.
Maintenance Schedule
Maintenance Operations
Weekly 50hrs
100hrs
400 hrs
Drain condensation
•
Check oil level
•
Clean intake filter
•
Check for oil leaks
•
Replace oil
•
Check cut-out
•
General cleaning of
compressor
•
Replace air filter
•
Check tube fittings and
electrical connections
•
Internal & external
inspection of tank
•
Check and adjust belt
tension
•
fig.9
fig.8
SAC1503B, SAC1103B, SAC1153B, SAC1203B Issue: 4(1, 3, 6) 30/10/18