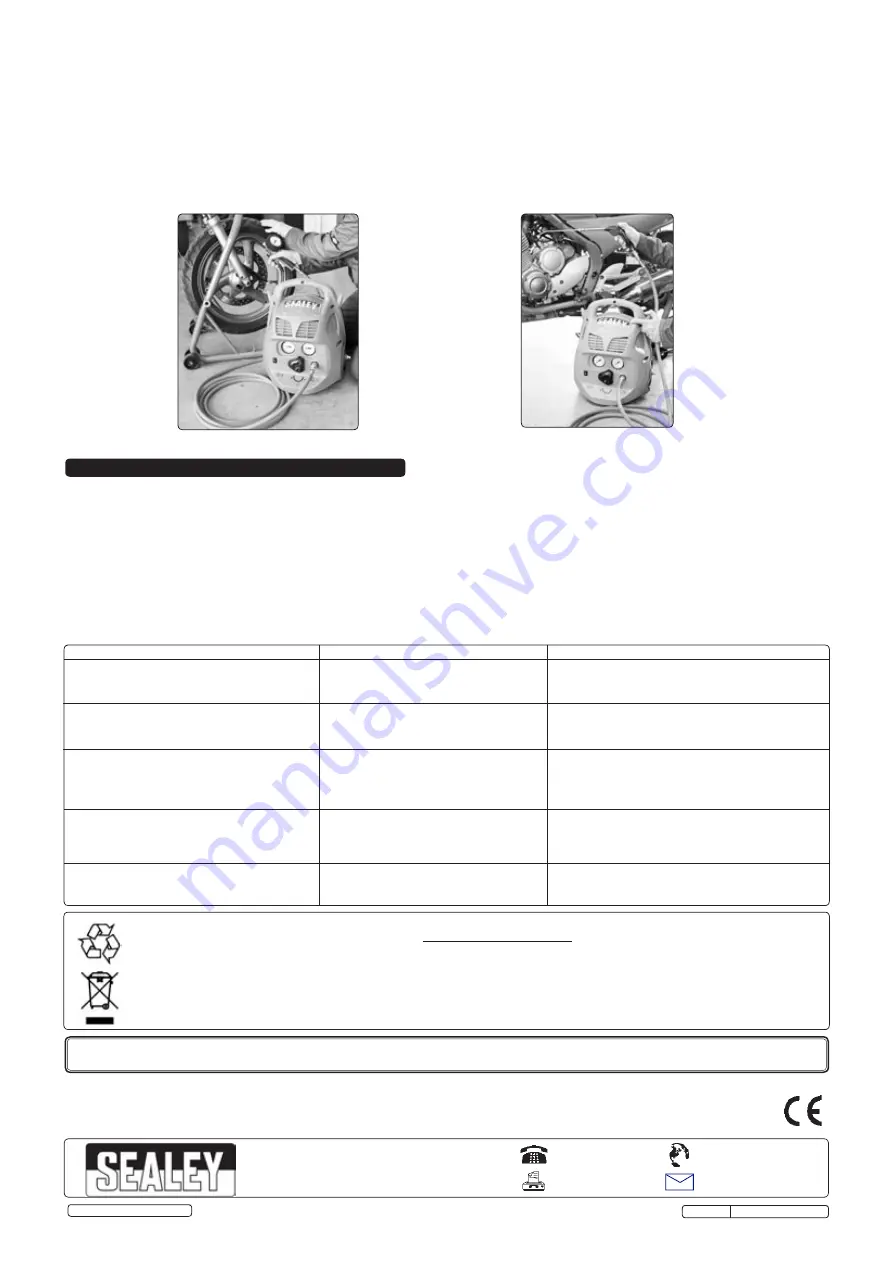
Original Language Version
SAC106B Issue: 3(SP) - 29/11/13
4. MAINTENANCE & TROUBLESHOOTING
Before carrying out any maintenance, switch compressor off, unplug it from the mains electricity supply, depressurise the
tank and allow unit to cool down fully.
4.1.
Keep the compressor clean and free of dust. Do not use cleaning agents. Wipe the compressor using a slightly dampened cloth and
blow it over with compressed air, if available.
4.2.
Ensure that the ventilation openings are clear. Do not allow any extraneous material to enter the unit via any of the ventilation
openings.
4.3.
To prevent corrosion to the tank, drain it on a regular basis by opening the drainage tap at the end of the tank, after draining ensure
the drainage tap is fully closed.
4.4.
The troubleshooting guide below is intended to give an indication of the type of fault which may develop with the compressor over a
long period of service. The chart is not intended as a guide on how to repair the fault, it is recommended that the compressor is
returned to an authorised service agent for rectification of serious faults.
NOTE: It is our policy to continually improve products and as such we reserve the right to alter data, specifications and component parts without prior notice.
IMPORTANT:
No liability is accepted for incorrect use of this product.
WARRANTY:
Guarantee is 12 months from purchase date, proof of which will be required for any claim.
INFORMATION:
For a copy of our latest catalogue and promotions call us on 01284 757525 and leave your full name and address, including postcode.
01284 757500
01284 703534
Sole UK Distributor, Sealey Group,
Kempson Way, Suffolk Business Park
,
Bury St. Edmunds, Suffolk,
IP32 7AR
www.sealey.co.uk
Web
3.7.
Do not leave the compressor running for any length of time with the air tool attached not being used. If there is a pause in the
work, switch the compressor off. These compressors have a duty-cycle of 30%. For each period of use, a rest period of 70% of the
cycle period should be left before using it again. For example, after 3 minutes use, a rest period of 7 minutes should follow. If the
motor over-heats, the thermal cut-out will operate and cut the motor out. When the temperature has returned to normal, the motor will
re-start automatically.
3.8.
When work is complete, switch the compressor off by pressing the I/O switch and releasing. Disconnect the air tool from the
compressor and relieve remaining pressure. Open the drainage tap at the end of the tank, tip the compressor to allow any moisture to
be drained from the tank. This prevents corrosion on the inside of the tank. Close drainage tap.
3.9.
If it is intended to store the compressor away, allow it to cool before storing it carefully in a safe, dry, dust free, childproof location.
Environmental Protection.
Recycle unwanted materials instead of disposing of them as waste. All tools, accessories and packaging should be
sorted, taken to a recycle centre and disposed of in a manner which is compatible with the environment.
When the product is no longer required, it must be disposed of in an environmentally protective way.
Fault
Possible Cause
Remedy
Air leakage from the valve of the pressure
switch whilst the compressor is off.
Pressure switch valve defective, due to
wear or dirt on the seal, does not perform
correctly.
Unscrew the head of the valve, clean the valve seat
and the rubber disc (replace if worn).
Reassemble and tighten carefully.
The compressor does not stop and the safety
valve is tripped.
Reduction in performance. Frequent start-up.
Low pressure values.
Irregular functioning of the compressor or
broken pressure switch.
Excessive air consumption, leaks from
the couplings and/or pipes.
Switch off compressor and contact
Authorised Service Agent.
Clean the air vents and ensure the work area is
ventilated. Do not over-run the compressor's duty
cycle.
Air tool requires higher spec. compressor.
Check / replace the seals of the fitting.
The compressor stops, then restarts
automatically after a few minutes.
Tripping of the thermal cutout due to
overheating of the motor.
Parts support is available for this product. To obtain a parts listing and/or diagram, please log on to www.sealey.co.uk,
email [email protected] or phone 01284 757500.
© Jack Sealey Limited 2013
Inflating a motorcycle tyre
BIowing an engine clean
Compressor operating note changes.
Blockage within the tool or pinched hose.
Switch off immediately, source restriction and
eliminate before re-starting.