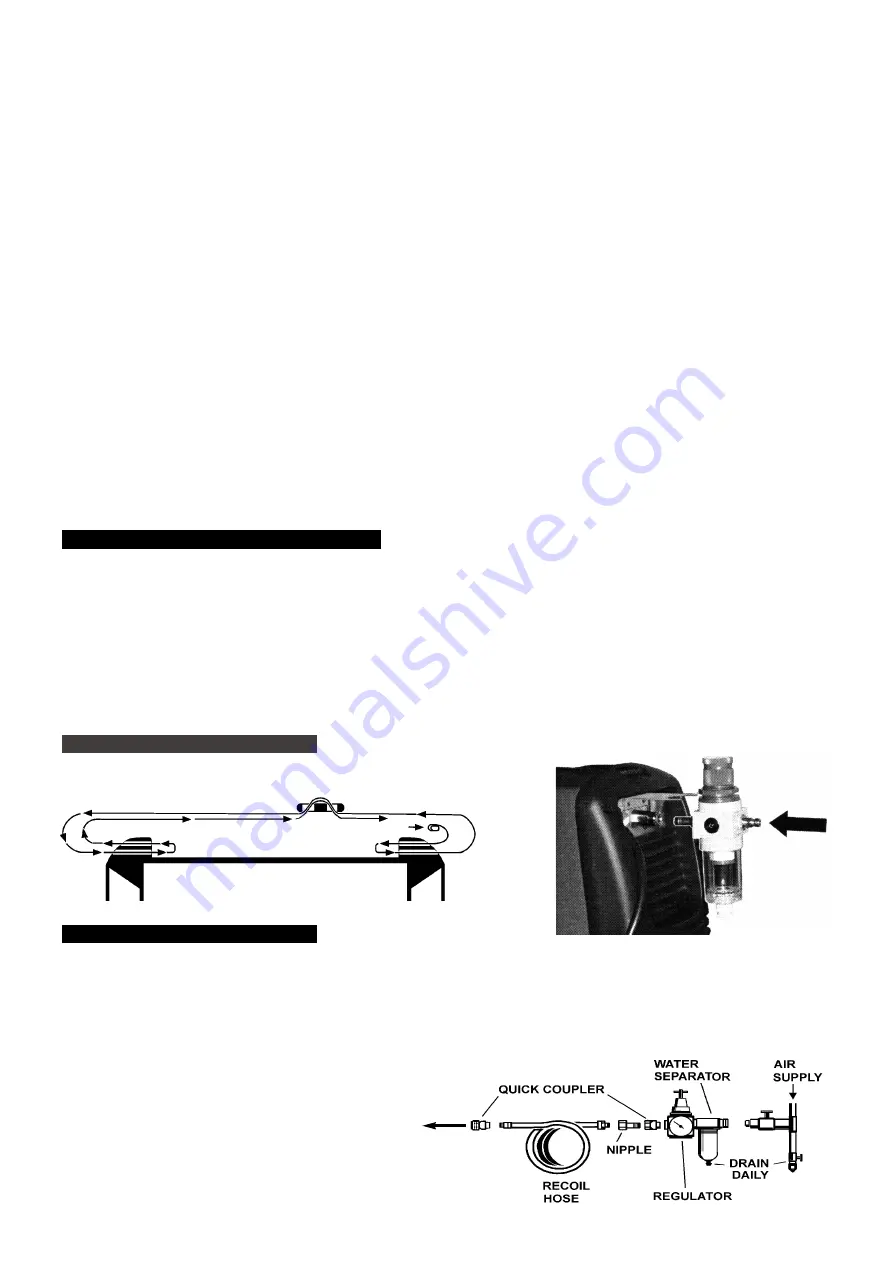
3. STRAP ASSEMBLY
p
WARNING:
Use a welding mask to protect your eyes and avoid exposing skin to the ultraviolet rays given off by the electric arc.
Always wear protective clothing, insulating gloves and shoes.
Keep all protective items clean and undamaged.
3
Keep unauthorised persons away from the work area. Any persons working within the area must wear the same protective items.
3
Remove ill-fitting clothing before wearing protective clothing, also remove ties, watches, rings and other loose jewellery and contain long hair.
3
Stand correctly keeping a good footing and balance and ensure that the floor is not slippery. Wear non-slip shoes.
3
Ensure the workpiece is correctly secured before operating the plasma cutter.
3
Avoid unintentional contact with workpiece. Accidental or uncontrolled switching on of the torch may be dangerous and will wear the nozzle.
7
DO NOT use cables and torch if the insulation is worn or connections are loose.
7
DO NOT attempt to fit any unauthorised torches or other components to the plasma cutter.
7
DO NOT cut surfaces that are painted, galvanic coated, oily or greasy.
7
DO NOT use any metallic structure which is not part of the workpiece, other than the supporting work bench, as a substitute for the return
cable of the plasma current.
s
DANGER!
DO NOT cut near inflammable materials, solids, liquids, or gases. Remove all flammable materials such as waste rags etc.
7
DO NOT cut containers or pipes which have held flammable materials or gases, liquids or solids. DO NOT cut materials that have been
cleaned with chlorinated solvents (or near such solvents) as vapours from the arc action may be toxic.
7
DO NOT operate cutter while under the influence of drugs, alcohol or intoxicating medication, or if tired.
7
DO NOT use the plasma cutter for a task it is not designed to perform.
7
DO NOT operate the plasma cutter if any parts are damaged or missing as this may cause failure and/or personal injury.
7
DO NOT carry, or pull cutter by cables. DO NOT strain or bend cables and protect them from sharp or abrasive items. DO NOT stand on
cables. Protect from heat. Long lengths of slack must be gathered and neatly coiled. DO NOT place cables where they endanger others.
7
DO NOT hold the workpiece in your hand.
7
DO NOT get the plasma cutter wet or use in damp or wet locations, or areas where there is condensation.
7
DO NOT touch the workpiece close to the cut as it will be very hot. Allow to cool. The cut edge of the workpiece will also be very sharp.
7
DO NOT touch the torch immediately after use. Allow the torch to cool.
3
When not in use store the unit in a safe, dry, childproof area.
1.3. GENERAL SAFETY - AIR SUPPLY
p
WARNING!
Ensure correct air pressure is maintained and not exceeded. Recommended pressure is 55-70psi.
p
WARNING!
DO NOT exceed maximum entry pressure of 116psi (8 bar). Excessive pressure may cause damage and/or personal injury.
3
Keep air hose away from heat, oil and sharp edges. Check air hose for wear before each use and ensure that all connections are secure.
7
DO NOT carry the cutter by the hose, or yank the hose from the air supply, and DO NOT direct air from the air hose at yourself or others.
If not already fitted, assemble the carrying
strap as shown:
4. AIR SUPPLY
Output . . . . . . . . . . . . . . . . . . . . . . . . . . .15-30A
Duty cycle . . . . . . . . . . . . . . . . . . . .30% @ 30A
Air requirements . . . . . . . . . . . . . . . . . .100 l/min
Air pressure . . . . . . . . . . . . . . . . . . . . . .55-70psi
Power . . . . . . . . . . . . . . . . . . . . . . . . . . .3.5 kW
Mains Voltage . . . . . . . . . . . . . . . . . .230V - 1ph
Insulation class . . . . . . . . . . . . . . . . . . . . . . . . .H
Electrical protection . . . . . . . . . . . . . . . . .Class 1
Case protection . . . . . . . . . . . . . . . . . . . . . .IP23
Weight . . . . . . . . . . . . . . . . . . . . . . . . . . . . .10kg
INPUT
Absorbed current . . . . . . . . . . . . . . . . . . 12-21A
Power factor . . . . . . . . . . . . . .(cos
j
) 0.68 - 0.72
Delayed fuses . . . . . . . . . . . . . . . . . . . . . . . .16A
OUTPUT
No load voltage . . . . . . . . . . . . . . . . . . . . . .370V
Rated cutting voltage . . . . . . . . . . . . . .86.8-92V
Rated cutting current . . . . . . . . . . . . . . . .17-30A
2. INTRODUCTION & SPECIFICATION
The PP30 is an inverter power supply fitted with a plasma cutter control circuit with a 4 LED information panel. The plasma cutter is suitable
for cutting steel, stainless, aluminium and brass. Includes integrated air filter and regulator unit and panel mounted pressure gauge.
PLASMA TORCH
Gas . . . . . . . . . . . . . . . . . . .DRY compressed air
Air pressure . . . . . . . . . . . . . . . . . . . . . .55-70psi
Cooling flow rate . . . . . . . . . . . . . . . . . .100l/min
Striking system . . . . . . . . . . . . . . . . . . .Pilot arc
Max. cutting current . . . . . . . . . . . . . . . . . . .30A
Max. cutting thickness (carbon steel) . . . . .10mm
p
WARNING! Ensure you have read and understood the safety instructions in 2.3. before connecting or operating the air supply.
4.1. An external compressed air supply must be attached to the plasma cutter. The supply must produce a minimum of 55-70psi with a
capacity of 100l/min. The supply pressure to the unit must not exceed 90psi.
4.2. To avoid damage to the cutter and torch, ensure that the air supply is clean and free from moisture. Fit the regulator/filter unit (supplied)
to the air inlet at the rear of the cutter. Support with the bracket provided (see above right).
4.3. The air system inlet filter should be cleaned weekly.
4.4. Line pressure should be increased to compensate for unusually long air hoses (over 8 metres).
Minimum hose diameter should be 10mm I.D., with fittings having the same bore.
4.5. Keep hoses away from heat, oil and sharp edges.
Check hoses for wear, and make certain that all
connections are secure.
Note
: DO NOT use an oiler with the
air system, the air must remain
clean and
DRY
at all times (see hook-up diagram to right).
TO REGULATOR/FILTER ON
PLASMA CUTTER
PP30 - 1 - 130901