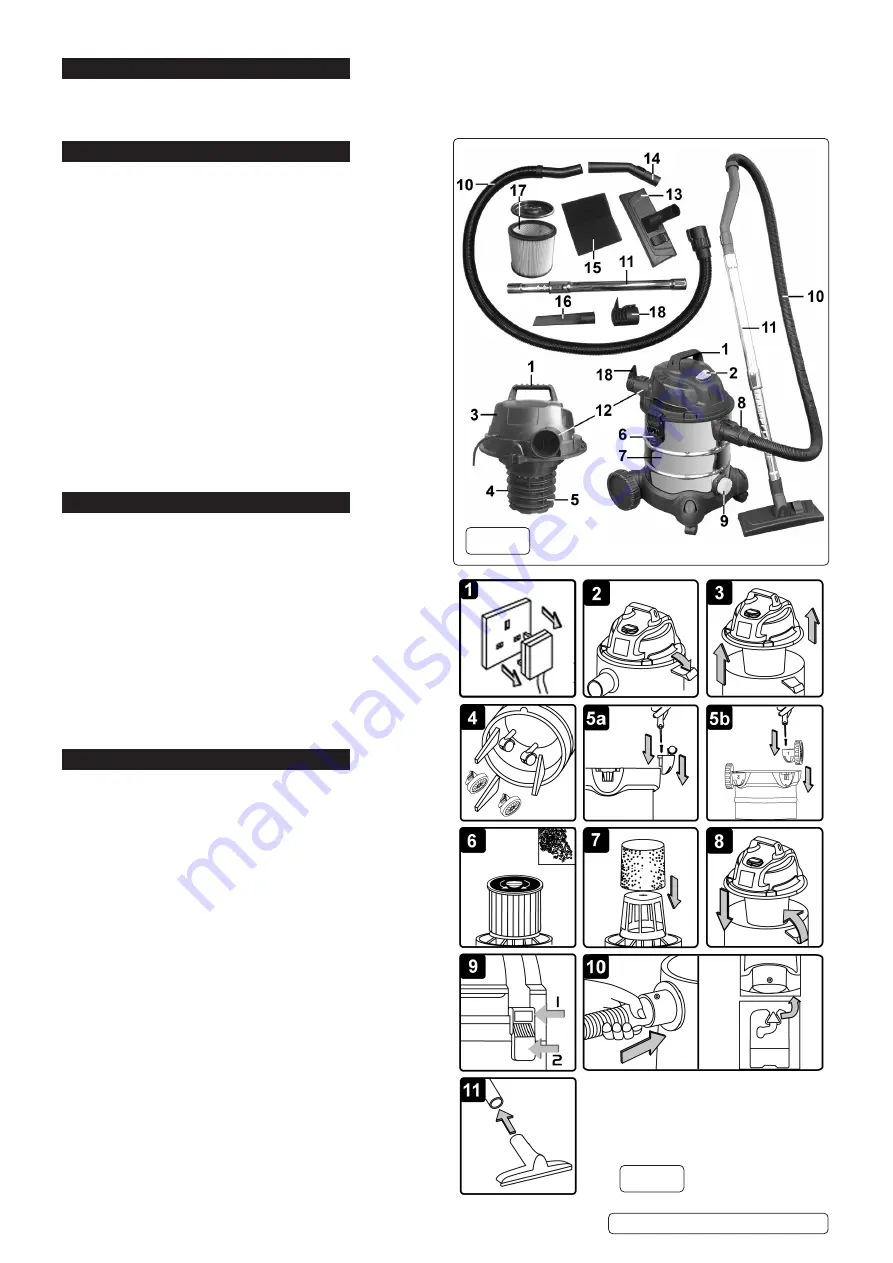
2. INTRODUCTION
High powered, lightweight industrial unit with blower facility. Constructed from stainless steel, the drum unit is mounted on two
castor and two fixed wheels. Tool storage points on head and base. Supplied with 4.5m cable with 3-pin plug, deluxe tool kit,
including stainless steel telescopic rigid extension tube, cartridge filter and wet-use foam filter.
3. CONTENTS
3.1.
CARTON CONTENT
3.1.1.
Carefully unpack the carton.
3.1.2.
Locate the two side clasps (fig.1.6) which hold the top
section (fig.1.3) in place.
3.1.3.
Undo the clasps, remove the power head and take out
the items in the container.
3.1.4.
Check and identify each component as listed below.
If anything is missing or damaged please contact your supplier
immediately.
4. SPECIFICATION
MODEL NO: ...........................................................PC200SD.V3
A
irflow:
.........................................................................
120 m³/hr
Drum Size: ...........................................................................20 L
Filter Type: ................................................................... Cartridge
Maximum Vacuum Pressure: ........................................140 mbar
Motor Power: ...................................................................
1250 W
Supply: .............................................................................. 230 V
Vacuum Accessories Diameter: .....................................
Ø35 mm
Optional Accessories:
P
C200PB5
.................................
Optional Dust Bags (Pack of 5)
Replacement Parts:
PC200CFL .......................................................... Cartridge Filter
PC200FF10 .........................................Foam Filters (Pack of 10)
5. ASSEMBLY
5.1.
Ensure the mains plug is disconnected. (fig.2.1)
5.2.
Undo clasps. (fig.2.2)
5.3.
Lift off the power head assembly. (fig.2.3)
5.4.
Remove contents from inside the container. (fig.2.4)
5.5.
Turn the drum upside down and insert the castor assembly
mouldings into the slots in the base either side of the blue
drain cap. Ensure they are pushed all the way in and fix them
with the self tapping screws provided. (fig.2.5a)
DO NOT
overtighten.
5.6.
The wheel assembly mouldings are marked 1 and 2. Insert
the wheel assembly mouldings into the two remaining slots
in the base ensuring that the number on each moulding
matches the number to be found on the base. Ensure they
are pushed all the way in and fix them with the self tapping
screws provided (fig.2.5b)
DO NOT
overtighten.
5.7.
For dry vacuum cleaning use the locking cartridge filter
supplied and with the raised rim uppermost fit the cartridge
filter tube down over the filter basket and push fully home.
Place the locking disc onto the top of the filter and turn
the locking bar until the latch drops into the slot in the top
of the filter basket. Continue turning until the filter is fully
locked down. (fig.2.6)
5.8.
For wet vacuum cleaning fit the supplied foam filter. (fig.2.7)
NOTE:
DO NOT
operate the cleaner without a cartridge filter
fitted as this will damage the machine and invalidate your
warranty.
5.9.
Replace the power head assembly onto the drum ensuring
Original Language Version
© Jack Sealey Limited
Item Description
1 Handle
2 ON/OFF switch
3 Top section
4 Filter basket
5 Safety float valve
6 Clasp
7 Stainless Steel drum
8 Vacuum hose connection
9 Drain Cap
10
Flexible vacuum hose
Item Description
11 Telescopic suction tube
12 Blow connection
13 Combination brush
14 Elbow tool
(Air regulator handle)
15 Foam filter
16 Crevice tool
17 Locking Cartridge filter
(fitted as standard)
18 Noise muffler
fig.2
fig.1
P
C200SD.V3 Issue 4 (4,F) 08/09/20