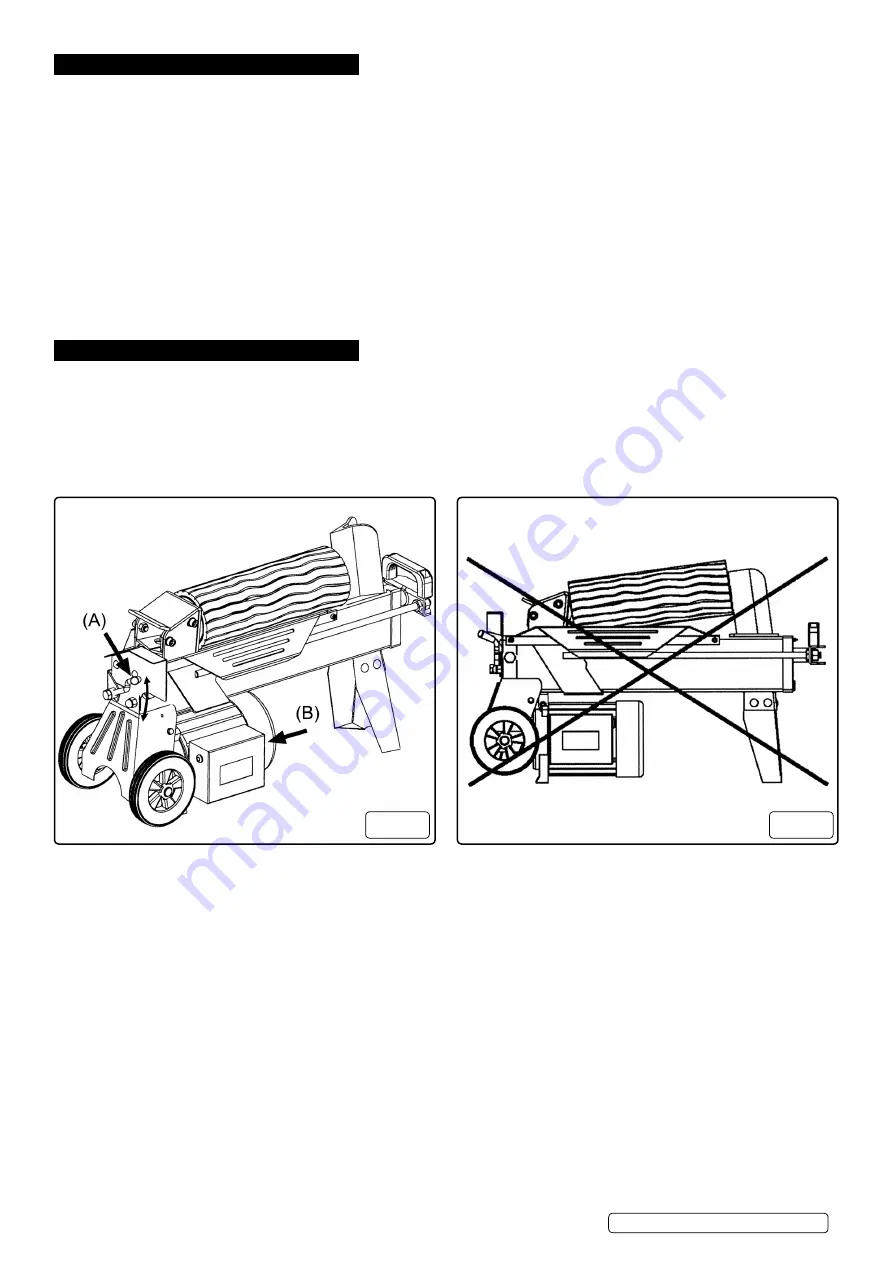
5. set up & preparation
5.1.
Assembly. Bolt the support leg (5) to the log splitter using the 5 nuts and bolts provided.
5.2.
moving the log splitter. the log splitter rests on the support leg and two rubber feet just in front of the wheels which are slightly off the
ground. To move the log splitter take hold of the handle (4) and lift the front end up by about 30° so that the unit tips off the feet and onto
the wheels. move the unit to the required position. As you lower it to the ground it will rest back onto the rubber feet.
5.3.
Operating position. We do not recommend that the log splitter is used on the ground as the operators face will tend to be too near to the
area of operation and therefore vulnerable to flying wood chips and debris.
5.4.
With the help of another person lift the log splitter onto a stable, flat and level work surface 60 to 75cm high.
5.5.
Ram extension. Remember that when the unit operates the ram will extend out of the front of the main beam by up to 52cm. Therefore
allow plenty of clearance beyond the front of the unit.
5.6.
Bleed Screw. See fig.2 -13. Before operating the log splitter the bleed screw should be opened by 3 turns to allow air to pass in and out of
the oil tank. Air flow through the bleed screw should be detectable during operation. When moving the log splitter close the bleed screw to
avoid spilling oil. remember to open it again before the next operation.
Warning!
Failure to open the bleed screw (see 4.5 above) will trap air within the system. The continued compression and
decompression of this air will blow out the seals of the hydraulic system and cause permanent damage to the log splitter thus
invalidating your warranty.
6. operating
Warning!
ensure you read, understand and apply the safety instructions before use.
6.1.
the control system of the log splitter requires the operator to use both hands. the left hand will control the hydraulic control lever
(A) and the right hand controls the motor push button (B) as shown below in fig.3. If either hand is removed from the controls the log
pusher stops. When both hands are removed from the controls the ram retracts and the log pusher automatically returns to the start
position.
Warning!
this system has been designed to prevent the operator from handling the log during the splitting process. for safety reasons
the operator must not ask a second person to place or handle the log. the system is designed to be operated by one person only.
6.2.
A number of factors will affect the way a log splits including the hardness of the wood and the complexity of the grain. A log which includes
the junction of another branch or branches may be more difficult to split. ideally the ends of the log should be cut square otherwise the log
may change position when pressure is applied to it.
6.3.
Always split a log along its grain. never attempt to split a log laid across the machine as this could be dangerous for the operator and
could seriously damage the machine.
6.4.
Place a log onto the table as shown above in fig.3 ensuring that it sits
between the log guides and the grain is aligned with the splitting
wedge.
6.5.
operate the controls. if the log becomes misaligned between the log pusher and the splitting wedge when the log pusher first makes
contact with the log, let go of the controls and allow the ram to retract. Rotate/reposition the log and try again. If the log will not sit properly
on the table or continues to be misaligned under pressure it should be discarded or have the ends recut square.
Warning!
If the log does not split within 5 seconds the controls must be released. After more than 5 seconds use the oil will
become overheated and the machine could be damaged. failure to split the log means that its hardness is beyond the capacity of the
machine
and the log should be discarded to protect the log splitter.
6.6.
Do not
allow logs to ride up the splitting wedge as shown in fig.4. When pressure is applied to the upper part of the wedge only this
could break the wedge or damage the machine.
6.7.
Do not
attempt to split a short log by pushing it with another log as one of the logs may fly up and hit you.
6.8.
Do not
attempt to free a jammed log by striking it with a hammer as this may damage the machine or cause a sudden release of the
log which could be dangerous. See fig.5.
fig.3
fig.4
l
S370H, LS520H | Issue 4 02/05/17
Original Language Version
© Jack sealey limited