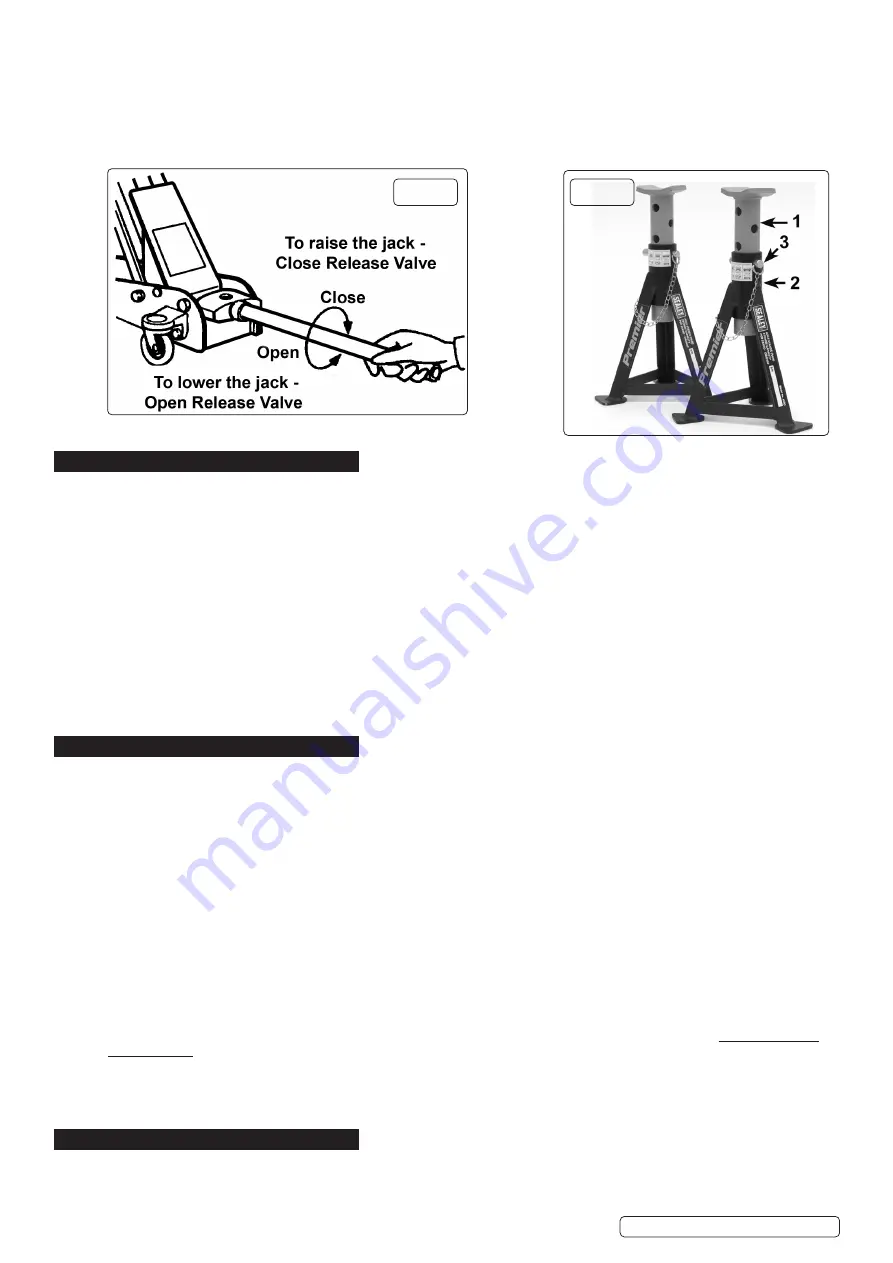
WARNING!
The jack is a lifting device only and must not be used to support the load. Use correctly rated axle stands to support the load.
4.3.
LOWERING THE VEHICLE
WARNING!
Ensure there are no persons or obstacles beneath the vehicle, or in the path of it’s descent.
4.3.1.
Raise the jack high enough for the axle stands to be easily removed. Then turn the handle slowly anti-clockwise to open the release
valve (fig.1).
4.3.2.
The lowering speed is controlled by the amount the release valve is opened. Lower carefully, avoiding any sudden changes in descent
rate which could shock load the hydraulic system.
5. OPERATION - AXLE STANDS
5.1.
Familiarise yourself with the product. Check that the stands are in good condition and that no damage has been sustained during
transit. Insert the centre column
(fig.2.1) in the centre tube (fig.2.2), adjust to height required and insert the locking pin (fig.2.3).
5.2.
Ensure the maximum load does not exceed 6tonne per pair of axle stands, (3tonne for each stand).
5.3.
Refer to vehicle manufacturer’s instructions for recommended support points.
Check that the points are in good condition.
5.4.
Ensure the vehicle brake is on (or in park mode) and wheels are chocked.
5.5.
Adjust height of stand to correspond with the raised vehicle.
5.6.
Check that the locking pin is correctly pushed all the way through the centre column and out of the other side, then position stands
under vehicle at points recommended by vehicle manufacturer.
5.7.
Carefully and slowly lower the load onto stands. Ensure the load bearing points sit in the center of the stand saddle and check that the
stands are stable and not leaning. Also ensure that there are no objects or persons that could impede the safe lowering of the vehicle
onto the stands.
5.8.
To remove stands jack vehicle slightly so that stand can be removed.
5.9.
After use, hold the centre column
(fig.2.1) firmly when removing the locking pin (fig.2.3). Failure to do so will
allow the center column
to fall freely through the main center tube which could be dangerous.
WARNING!
Ensure you follow all instructions carefully.
Failure to note these warnings may cause damage, serious injury or loss of life
.
6. MAINTENANCE - JACK
6.1.
When the jack is not in use, the ram and the handle socket should be in their lowest positions to minimise corrosion.
Remove the handle to deactivate the jack.
6.2.
Keep the jack clean and lubricate all moving parts on a regular basis.
6.3.
Before each use, check for broken, cracked, bent, or loose parts, or any visible damage to ram, pump, saddle, lifting arm, frame and
all parts including nuts, bolts, pins and other fasteners. If any suspect item is found remove jack from service and take necessary
action to remedy the problem.
8
DO NOT
use the jack if believed to have been subjected to abnormal load or shock load.
6.4.
Periodically check the pump piston and piston rod for signs of corrosion. Clean exposed areas with a clean oiled cloth.
6.5.
After one year the oil should be replaced in order to extend the life of the jack. Use hydraulic jack oil only.
6.6.
IMPORTANT:
Only fully qualified personnel should attempt hydraulic maintenance or repair.
6.7.
To check the hydraulic oil level, fully lower the jack and the handle and remove the tray covering the oil filler plug, remove the oil
filler plug. The correct oil level should be approximately 5mm below the
filler opening. If oil level is low, fill as required. Make sure
that dirt is not allowed to enter the hydraulic system. Carefully pump unloaded jack 5 or 6 times to expel any air and then refit oil filler plug.
NOTE:
Use a good quality hydraulic jack oil, such as SEALEY HYDRAULIC JACK OIL.
WARNING: DO NOT
use brake fluid, or any fluid other than hydraulic jack oil, as this may cause serious damage to the jack and will
invalidate the warranty!
IMPORTANT:
NO RESPONSIBILITY IS ACCEPTED FOR INCORRECT USE OF THE JACK.
Hydraulic products are only repaired by local service agents. We have service/repair agents in all parts of the UK.
DO NOT RETURN
JACKS TO US.
Please telephone 01284 757500 to obtain address and ‘phone number of your local agent. If Jack is under
guarantee please contact your dealer.
6.8.
DE-COMMISSIONING THE JACK.
6.9.
Should the jack become completely unserviceable and require disposal, draw off the oil into an approved container and dispose of the
jack and the oil according to local regulations.
7. MAINTENANCE - AXLE STANDS
7.1.
Before each use, check that stands and stand welds are not cracked and that there are no missing or damaged parts.
7.2.
Any suspect axle stands must be removed from service immediately.
7.3.
Due to the potential hazards associated with stands,
DO NOT
misuse, or make any modification to, the stands or components.
fig.1
Original Language Version
© Jack Sealey Limited
fig.2
3015CXHV.V2 Issue 1 28/01/21