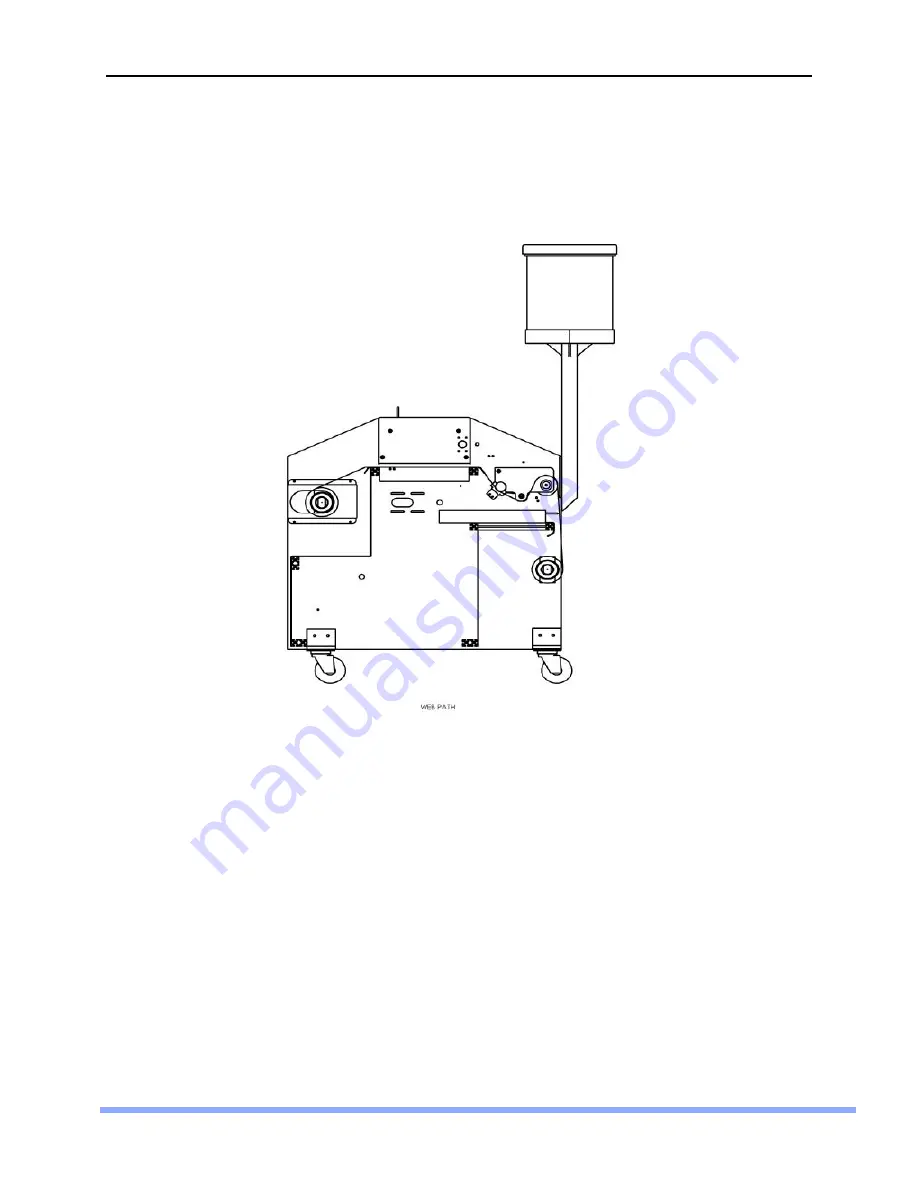
Section 2. Operating Procedures
13
3. Web the Laminator
A Web diagram is provided in Figure 2.3 Below
Figure 2.3 Web Diagram
Method
1. Lift Unwind Assembly to the UP position.
2. Load a take-up core onto the Take-up Mandrel and align with the edge of the
roll of media on the Unwind Mandrel.
3. Pull media up over the web Idler, under the Draw down Assembly and under
the Dryer Assembly to the Take-up Core.
4. Tape material to the Take-up core.
Note:
It is important to get the material as straight as possible to ensure a
minimal amount of “telescoping” on the Take-up Roller.
Summary of Contents for AquaSEAL AS-1600
Page 19: ...Section 3 Troubleshooting 18...