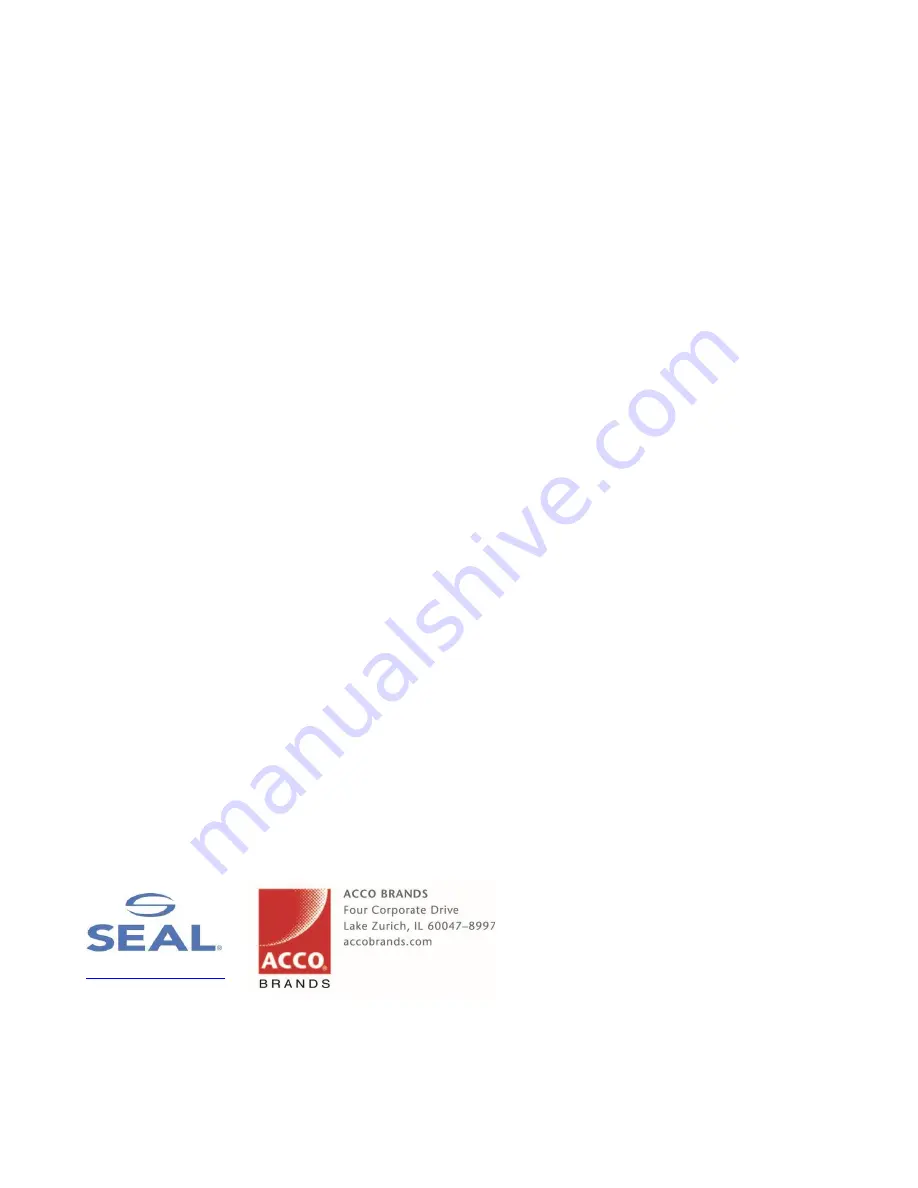
Contact Us:
SEAL Brands Technical Service
– US & Canada
Ph:
1-800-486-6502
Fax:
1-800-966-4554
Email: [email protected]
SEAL Brands Customer Service
– US & Canada
Ph:
1-800-257-7325
Fax:
1-800-966-4554
Email:
Summary of Contents for 54Base
Page 1: ...62 54Base Mounter and Laminator User Manual A Version Models Rev C December 2017...
Page 10: ......
Page 35: ...25 English...