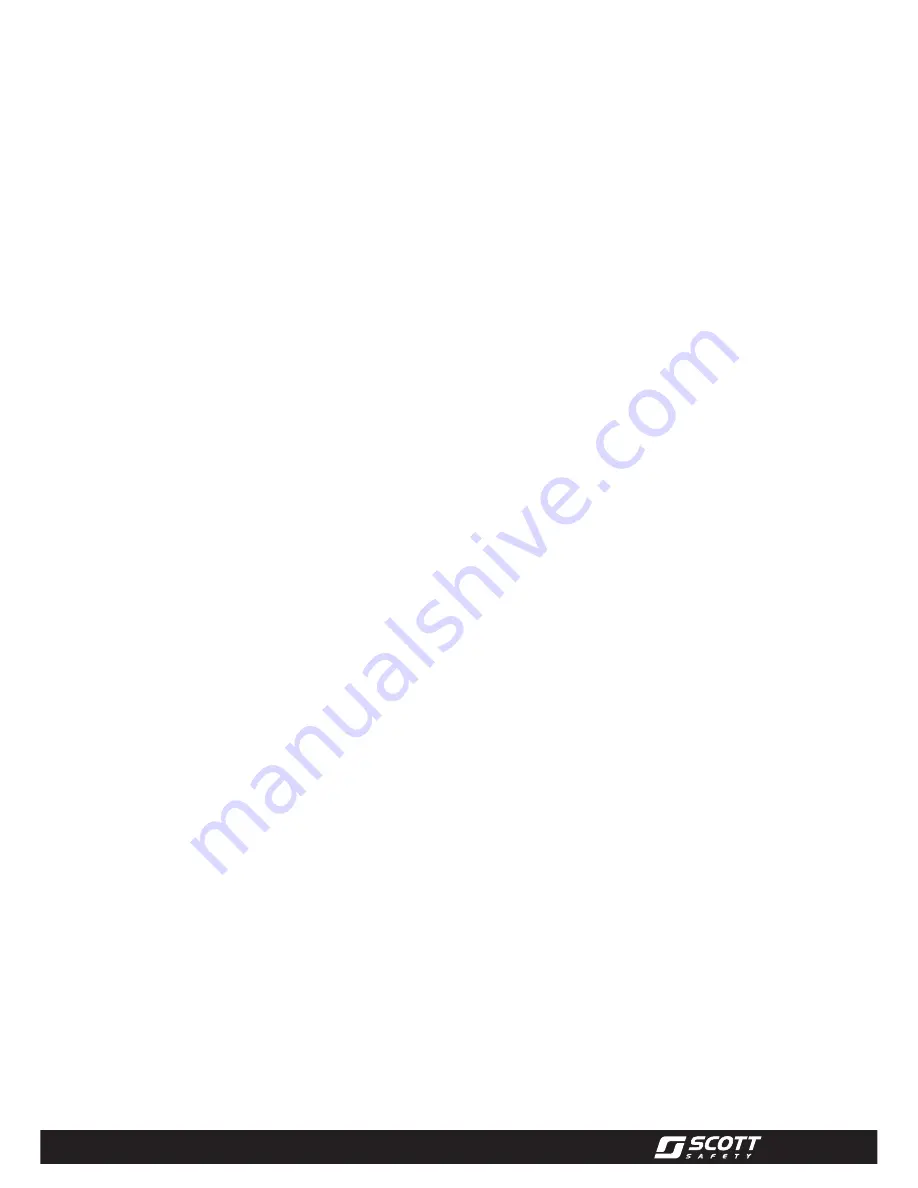
4
AFU 2 & AFU 4
INSTALLATION
AND OPERATING
PROCEDURE
CHECK COMPRESSOR/
SUPPLY
Check compressor inlet to verify that
there are no obstructions and ensure
that no exhaust fumes, vapours or other
contaminants enter the inlet connection.
Ensure that the compressor is operating
correctly and not overheating.
WARNING:
The AFU WILL NOT remove
contaminants such as Carbon
Monoxide (CO), Carbon Dioxide (CO2),
or other harmful gases of vapours.
If these or other harmful gases/
vapours are present, a suitable air
purifier MUST be used.
If using cylinder supply, ensure that
sufficient air is available for the
anticipated tasks.
16 bar. If the supply pressure exceeds
this, it will be necessary to fit an in-line
regulator and pressure relief valve
(PRV) to protect the AFU from over-
pressurisation. A pressure gauge on the
inlet provides a clear indication of the
supply pressure.
The 3/8” BSP male inlet connection on
the pressure gauge can accommodate
a suitable supply hose or medium-
pressure airline coupling.
The outlets are CEJN female couplings,
of which, two are provided on the AFU
2 and four on the AFU 4.
The filter elements are located in robust
metal housings fitted to a central yoke.
The housings may be removed by hand
to facilitate quick and easy replacement
of filter elements.
The element should be changed as per
our recommendations.
The recommended frequency of filter
element replacement is as follows:
Filter Element
Replace After
First Stage -
(AO Filter)
Maximum 6000
hours use
OR
Every 12 months
Second Stage -
(AA Filter)
Maximum 6000
hours use
OR
Every 12 months
Third Stage -
(AC Filter)
Maximum 1000 hours
use
OR
Every 2 months
Table 3: Frequency of Filter Element
Replacement
Note: It may be necessary to change
filter elements more frequently if the
airline supply is heavily contaminated.
PURGE AIR
Before installing the AFU to an airline
supply, purge the supply hose with air
to remove any water or loose debris
which may have become trapped within
the line.
CHECK HOSES
Ensure that all supply hoses are of
a type approved for the supply of
breathing air and that they are clean
and un-damaged. Check the operation
of all hose couplings to ensure that they
connect and disconnect correctly.
CHECK APPARATUS
Check the AFU to ensure that all
components are clean and un-damaged.
Any components showing signs of
damage should be replaced immediately.
Check breathing apparatus and
associated equipment in accordance
with the manufacturer’s instructions,
ensuring that all components are clean
and un-damaged.