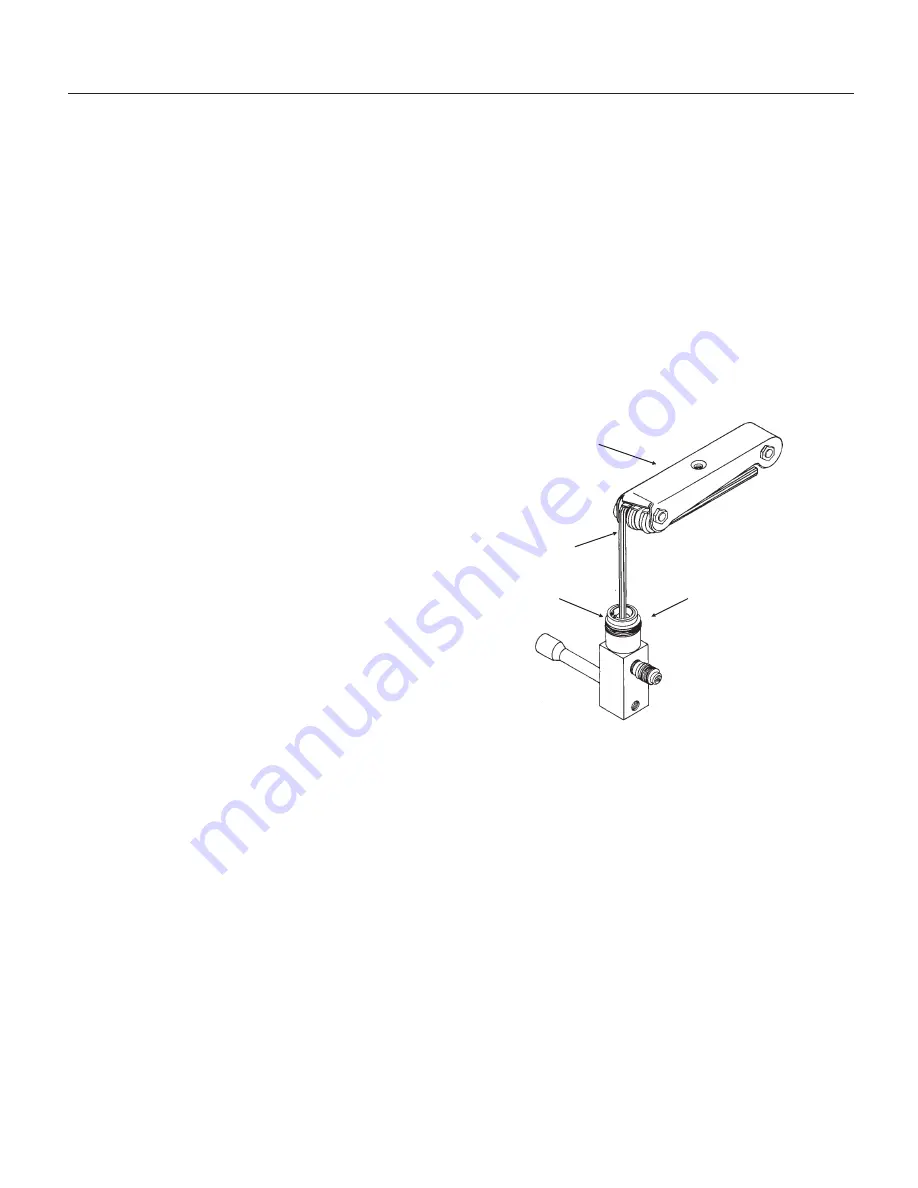
REFRIGERATION SERVICE
General Information:
Work on the refrigeration system should only be
done when it is certain that the system needs
repair.
•
Refrain from checking refrigeration
pressures without reason. Visual
inspection of the water system, observation of
the ice formation, amp draw, voltage, and
other techniques will lead to proper diagnosis.
Scotsman also recommends that, at the time
of initial start up, gauges not be used.
•
If gauges must be used, don’t always check
the high side pressure. If the condenser is
clean and seems to be operating correctly, it
most likely is. The low side pressure is more
important on an ice machine than the high
side.
•
If gauges must be used, use very short hoses
to minimize refrigerant discharged into the air.
•
Refrigerant should not be added except as a
way to determine the proper operation of the
product. If the system was low on refrigerant,
there is a leak, and it must be found and
repaired.
•
This system has a critical charge, it must be
recharged with the correct amount of
refrigerant as listed on the nameplate of the
ice machine, or performance will suffer.
•
Anytime the refrigeration system has been
opened, the dryer should be replaced. Note:
Only a HFC type dryer should be used.
•
When brazing the tubing connections to
components such as the TXV, the component
must be protected by heat sink material.
Recover, reclaim or recycle refrigerant. The
method chosen is up to the service company. Any
refrigerant placed into a Scotsman ice machine
must meet ARI spec 700-88. Reclaim programs
are available through most refrigerant wholesalers.
Access Valves: To use the access valves:
Remove the cap from the stem, use a 3/16" allen
wrench to check that the valve is CLOSED. The
remove the core cap.
Close the valve and replace the caps when the
job is finished. The valve must be closed and
the caps must be on or the valve will leak.
Torque Stem Cap to
8-12 ft. lb.
Torque Stem to
6-8 ft. lb.
Torque
Core Cap to
7-12 ft. lb.
Access Valves
Note: There are no valve
cores in this valve.
Allen
Wrench
TDE550 & TDE650
November 1995
Page 31