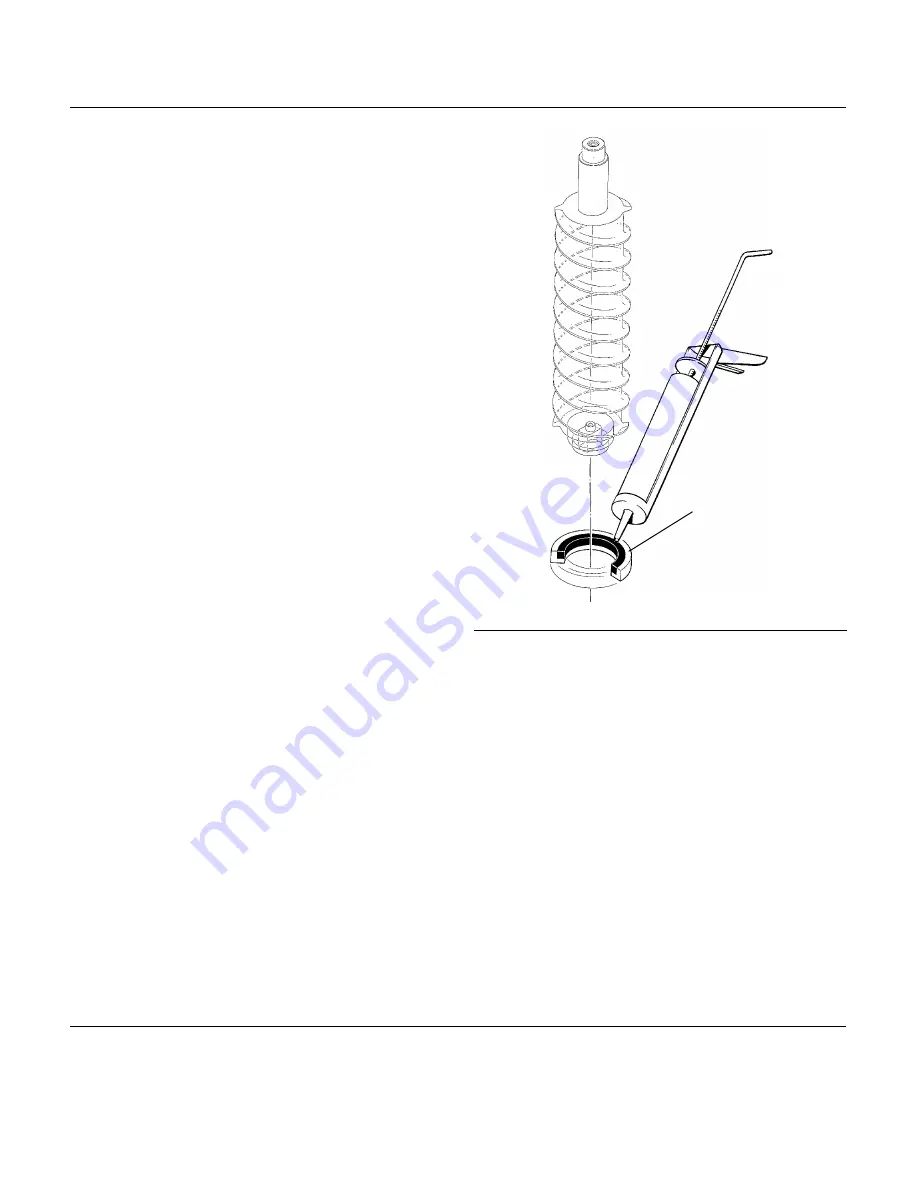
To Replace the Evaporator:
(Assuming all the steps for removal of the
thrust bearing, breaker, auger, and water seal
have been performed.)
1. Discharge the refrigerant from the ice
maker.
2. Unsweat the refrigerant connections:
a) At the thermostatic expansion valve outlet.
//////////////////////////////CAUTION///////////////////////////
Heat sink the TXV body when unsweating
or resweating the adjacent tubing.
//////////////////////////////////////////////////////////////////////////
b) At the suction line at the joint about 3" from
the evaporator.
3. Remove the evaporator.
4. Unsweat the drier from the liquid line.
5. After installing a new water seal in the new
evaporator ( see “To Replace the Water Seal”)
resweat the tubing connections.
6. Install an new drier in the liquid line.
7. Evacuate the system until dehydrated, then
weigh in the nameplate charge. Check for
leaks.
8. Install auger, breaker, breaker bearing
assembly, and ice discharge chute in reverse
order of disassembly. See “To Reassemble
Evaporator and Auger”
To Reassemble the Evaporator and Auger
1. After the gearmotor has been inspected,
fasten the evaporator to the gear motor, be
sure that the number of shims indicated on the
gear case cover is in place between the
gearcase cover and the drip pan gasket.
Torque the bolts to 110 inch pounds.
2. Lower the auger into the evaporator barrel,
slightly turning it to match up with the drive
end. Do Not Drop Into the Evaporator.
3. Complete the reassembly by reversing the
disassembly for the breaker & thrust bearing
assembly.
PLACE A BEAD
OF FOOD GRADE
SEALANT HERE
REMOVAL AND REPLACEMENT: Evaporator
Head Pressure Control Valve
1. Purge system of refrigerant
2. Break off process tube on the top of the
OLD head pressure control valve.
3. Unsweat old valve from tubing.
4. Unsweat old dryer from tubing.
5. Install new valve in place, check for correct
connections and be sure the number on the
side of the valve is “220"
6. Wrap the new valve body in wet cloths to
heat sink the valve body.
7. Sweat in the new valve and the new dryer.
8. Evacuate the system, and weigh the
nameplate charge into the receiver.
Charging Procedures
Extra care must be taken when recharging this
remote system. No liquid refrigerant may be
placed in the system at the compressor. DO
NOT use the schrader valves at the front of
the unit for weighing in the charge. All liquid
R-502 must be weighed into the receiver
through the “front seated” king valve.
NM950R
May, 1989
Page 34