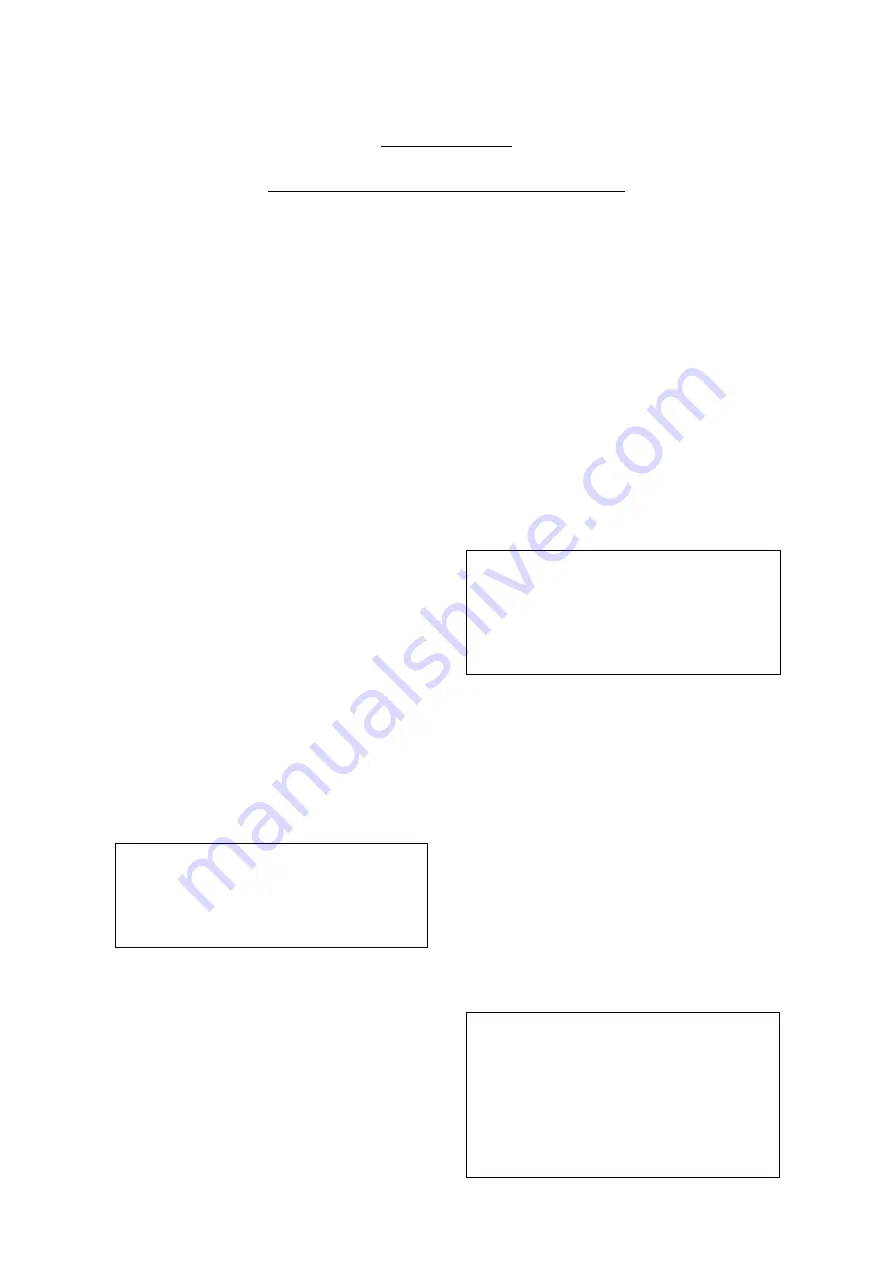
Page 20
Page 20
SECTION VII
MAINTENANCE & CLEANING INSTRUCTIONS
GENERAL
The periods and procedures for maintenance
and cleaning are given as guides and are not to
be construed as absolute or invariable. Cleaning
especially will vary, depending upon local water
conditions and the ice volume produced and,
each icemaker must be maintained individually,
in accordance with its own particular location
requirements.
ICEMAKER
THE FOLLOWING MAINTENANCE SHOULD
BE SCHEDULED AT LEAST TWO TIMES PER
YEAR ON THIS ICEMAKER. CALL YOUR
AUTHORIZED SCOTSMAN SERVICE AGENCY.
1.
Check and clean optional water line strainers
or water purification system.
2.
Remove screws and top and front panel.
3.
Remove cover from water reservoir and
depress the float to ensure that a full stream of
water enters each reservoir.
4.
Check that the icemaker cabinet is level, in
side-to-side and front-to-rear directions.
5.
Check that the water level in water reservoir
is below the overflow and is level to correspond
20 m/m below the ice discharge opening.
6.
Clean water reservoir and interior of the
freezer assembly, using a solution of SCOTSMAN
Ice Machine Cleaner. Refer to CLEANING-
Icemaker.
NOTE
. Cleaning requirements vary
according to local water conditions and
individual user operation. Visual inspection
of the auger before and after cleaning will
indicate frequency and procedure to be
followed in local areas.
7.
When doubtful about refrigerant charge,
install refrigerant gauges on Service valves and
check gauge. See Nameplate for refrigerant
charge specifications at liquid line: will be 1.7 Bar
(24 PSI).
8.
Check drive motor operation:
Normal operating temperatures about 70
°
which
is hot to touch. Check with Ammeter amps drawn
and make sure they are in the limits of Drive motor
windings.
9.
Check setting and function of all the pressure
controls also make sure that their corresponding
light will glow.
10. Inspect the top bearing in the ice breaker,
wipe clean of old grease and apply a coating of
food grade grease, SCOTSMAN P/N 263612.00
or equivalent.
11. Check for refrigerant leaks.
12. Check for water leaks. Pour water down
drain line to be sure that drain line is open and
clear.
13. Check the quality of ice. Ice should be
slightly wet when formed, but will cure rapidly to
normal hardness in the bin.
14. Check the bin thermostat control bulb, hold
ice on the control bulb of each system to test
icemaker shut-off.
NOTE
. The bin thermostat is factory se at
4
°
C differential and should keep the entire
icemaker system shut off at least 10 minutes
in high ambient temperatures, longer in low
ambients temperature during normal
operation. Settings are 1,5
°
C CUT-OUT and
4
°
C CUT-IN.
15. Check gear box oil level through its sight
glass every 6 months. Oil, on low speed section,
must be replaced every 25.000 hrs. Use
Syntetic Oil Shell Tivela SC320.
CLEANING
1.
Remove screws and the top, left and front
panel.
2.
Disconnect unit from power supply.
3.
Remove reservoir cover and block the float
in water reservoir.
4.
Drain the water reservoir and freezer
assembly using the drain tube attached to the
freezer water inlet. Return the drain tube to its
normal upright position and replace the end cap.
WARNING - SCOTSMAN Ice Machine
Cleaner contains Phosphoric and
Hydroxyacetic acids. These compounds
are corrosive and may cause burns. If
swallowed, DO NOT induce vomiting. Give
large amounts of water or milk. Call
Physician immediately. In case of external
contact flush with water. KEEP OUT OF
THE REACH OF CHILDREN.