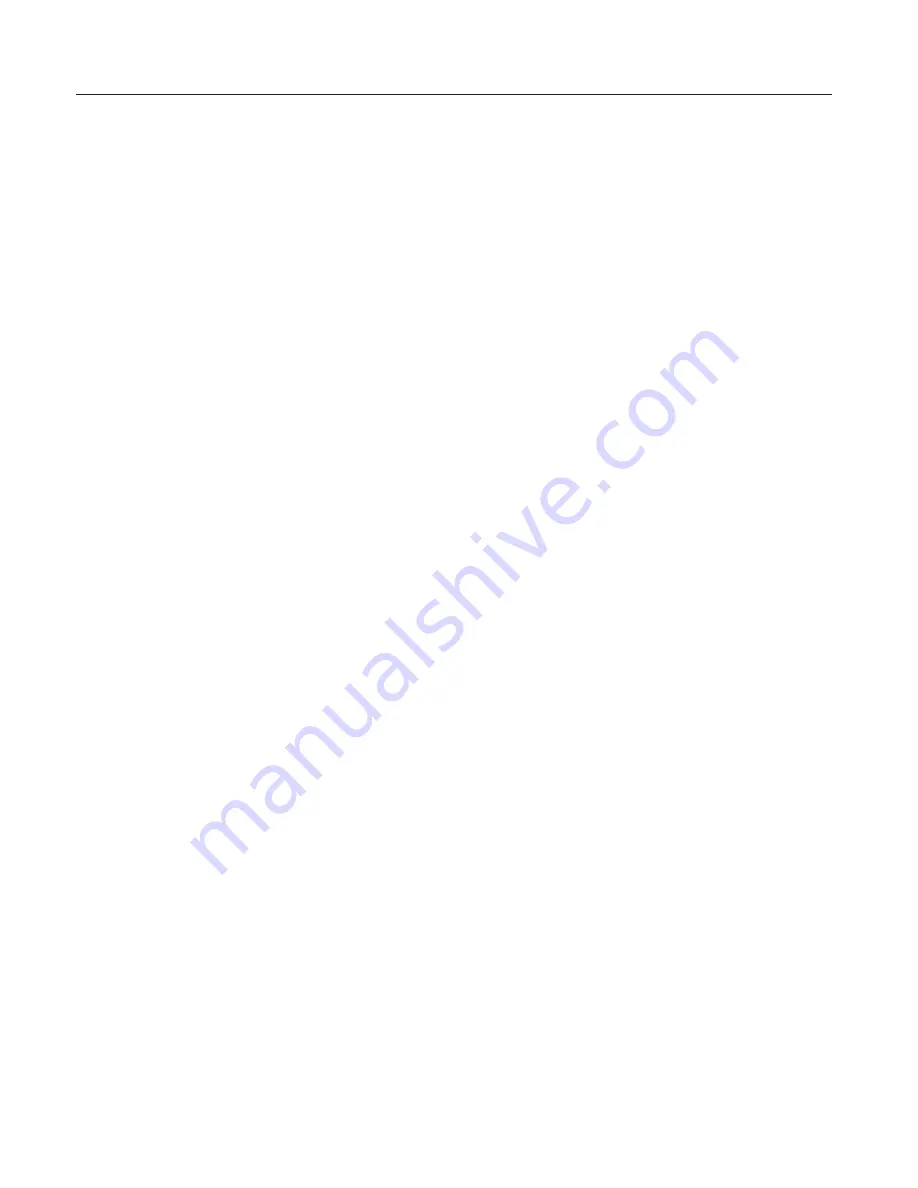
MAR Split - Electrical / Refrigeration
The electrical circuit consists of drive motor, water
pump, water pressure switch, spout switch and
time delay safety device.
A.
Drive motor
The evaporator drum drive motor is a single phase
motor of 1/2 HP wired for 220 Volts 60 Hz – 2.1
Amps - 1400 R.P.M. with inherent thermal
protector. In normal operation this motor draws
between .8 and .9 amps.
IMPORTANT Make sure that drive motor
rotates clockwise facing the unit’s front.
Failure to this, may result in wrong rotation of
evaporator drum with the risk of major damages to
the system.
B.
Water failure Switch
This switch used as safety device when low or
interrupted supply water conditions are
encountered.
Operates on pressure between supply line and
feed line to water reservoir.
Range is 0,8 atm (10 psi) off and 1,2 (17 psi).
Cuts off complete unit and Resets automatically.
C.
Ice Spout Safety Switch
Located on top of the Ice Spout, the Safety Switch
is operated by a plate on top of the ice chute by
the ice backing up in the spout.
The switch will shut-off the liquid line valve and
gear drive motor. It will automatically reset when
the ice melts.
D.
Timer
- Time Delay - With settings from 0 to 30
min. It delays the energizing of main contactor in
relation to its time setting, preventing short cycling
of unit’s motor compressor and drive motor.
E.
Automatic Expansion Valve (A.E.V.)
The automatic expansion valve meters the
refrigerant from the liquid line to the evaporator. As
the pressure decreases on the low side, the
expansion valve opens and refrigerant escapes
into the evaporator drum channel where it absorbs
heat from water while evaporating. The valve
maintains a constant pressure in the evaporator
coil when the system is running independently of
the amount of refrigerant in the system.
This valve has a manual adjustment to give the
evaporator coil the desired pressure of refrigerant.
Turning the adjustment to the left,
counterclockwise, will increase the rate the
pressure in the evaporator.
When the compressor is not running the valve will
remain closed as the low side pressure will be high
enough to close the expansion valve.
- MAR1400 or MAR2000 are each equipped with
an expansion valve having an orifice of 2,5 m/m.
F.
Evaporator Drum
Refrigerant inlet/outlet takes place on left side
journal.
The drum body is covered by a jacket in special
stainless steel resistant to the water corrosion.
The front edge of the scraping blade must have
a minimum clearance of 0.10 m/m(.004 inch)
from cylinder metal jacket.
G.
Refrigerant Seal System
Housed in the refrigerant inlet/outlet manifold
located on the evaporator drum left side journal, is
a leakproof joint. This joint is made with seals that
are carefully designed and installed. The seals use
two rubbing surfaces. One surface turns with the
cylinder journal and is sealed to it with on O ring of
synthetic material. The other surface is stationary
and fitted in its housing with leak-proof O rings.
The rubbing surfaces (optically flats) are made of
two different materials: hardened steel for the
rotating ring and graphite for the stationary ring.
The rotating parts are:
a) the spring collar
b) the compression spring
c) the stainless steel seal ring with O ring.
The stationary parts are:
a) the graphitic ring with O ring
b) the stainless steel housing ring with gasket and
O rings.
H.
Heat Exchanger
There is a heat exchanger mounted in the suction
and liquid line to reduce flash gas in the liquid line,
to reduce liquid refrigerant in the suction line, and
to subcool the liquid refrigerant thereby increasing
the operating efficiency.
MAR1400 & MAR2000
December 2000
Page 22