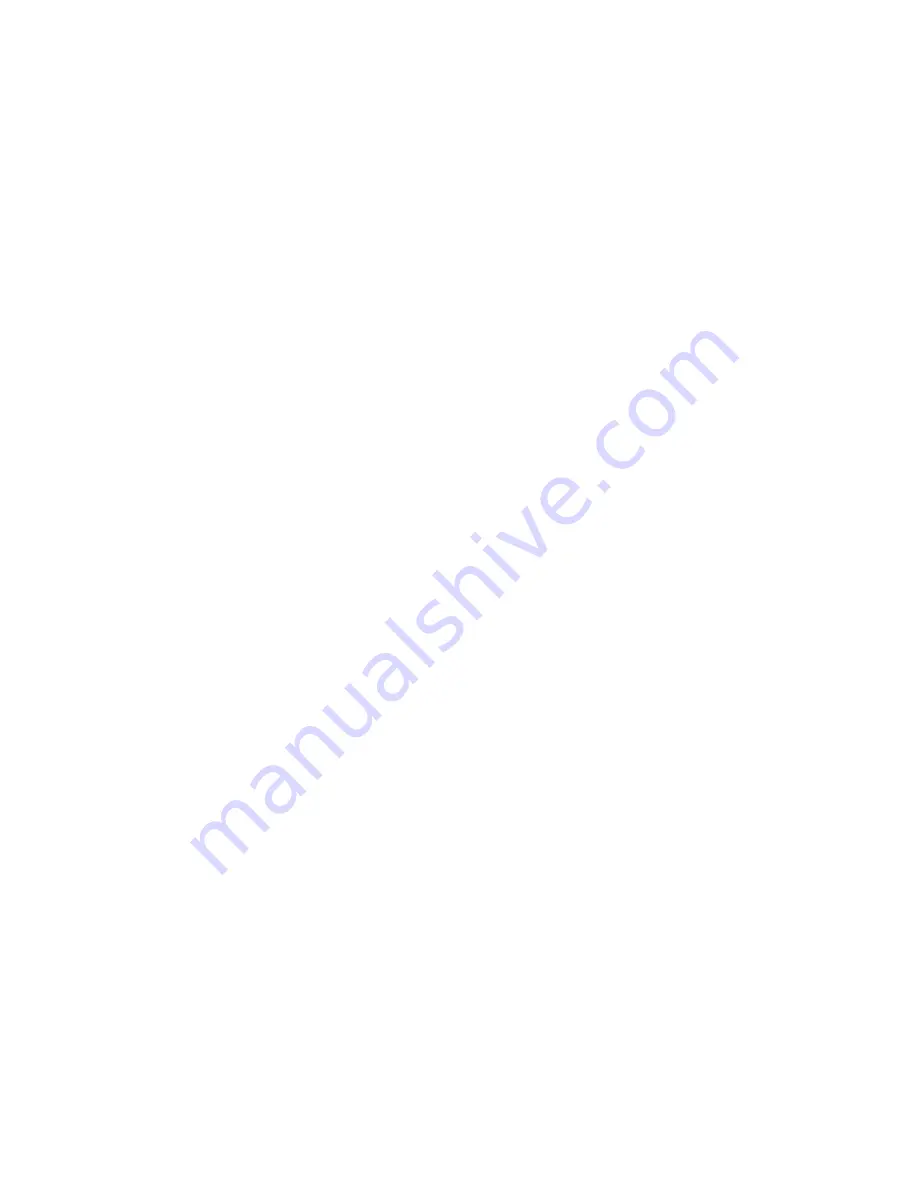
DD40
Start Up
(Only after ice bank has formed)
1. Turn CO2 on.
2. Set high pressure regulator to 80-100 PSI
3. Set low pressure regulator to 40-50 PSI
4. Set diet pressure regulator (if used) to 8-10 psi.
5. Connect syrup tanks and gas disconnects to syrup tanks.
6. Check for CO2 leaks by turning CO2 tanks off for 4-5 minutes. If the high pressure guage
drops, there is a CO2 leak. Then check each fitting with a soap solution.
7. Turn on the water.
8. Plug in or switch on the carbonator.
9. Purge CO2 gas pressure from the carbonator once or twice while filling by pulling up on
pressure relief valve on the top of the carbonator.
10. Actuate each valve until both water and syrup flow.
11. Check each valve for proper adjustment. Flow rate per valve should be 1.25 oz. per
second of carbonated water, and .25 oz. per second syrup for standard valves. For a fast
flow valve, flow rate should be 2.5 oz. per second of carbonated water, and .5 oz. per
second syrup.
12. Replace cover and screws.
13. Check that the CO2 tanks are secure from falling over.
14. If water noise occurs, add water to bath.
15. Allow machine to build ice bank before dispensing product at maximum draw rate.
February, 1988
Page 6