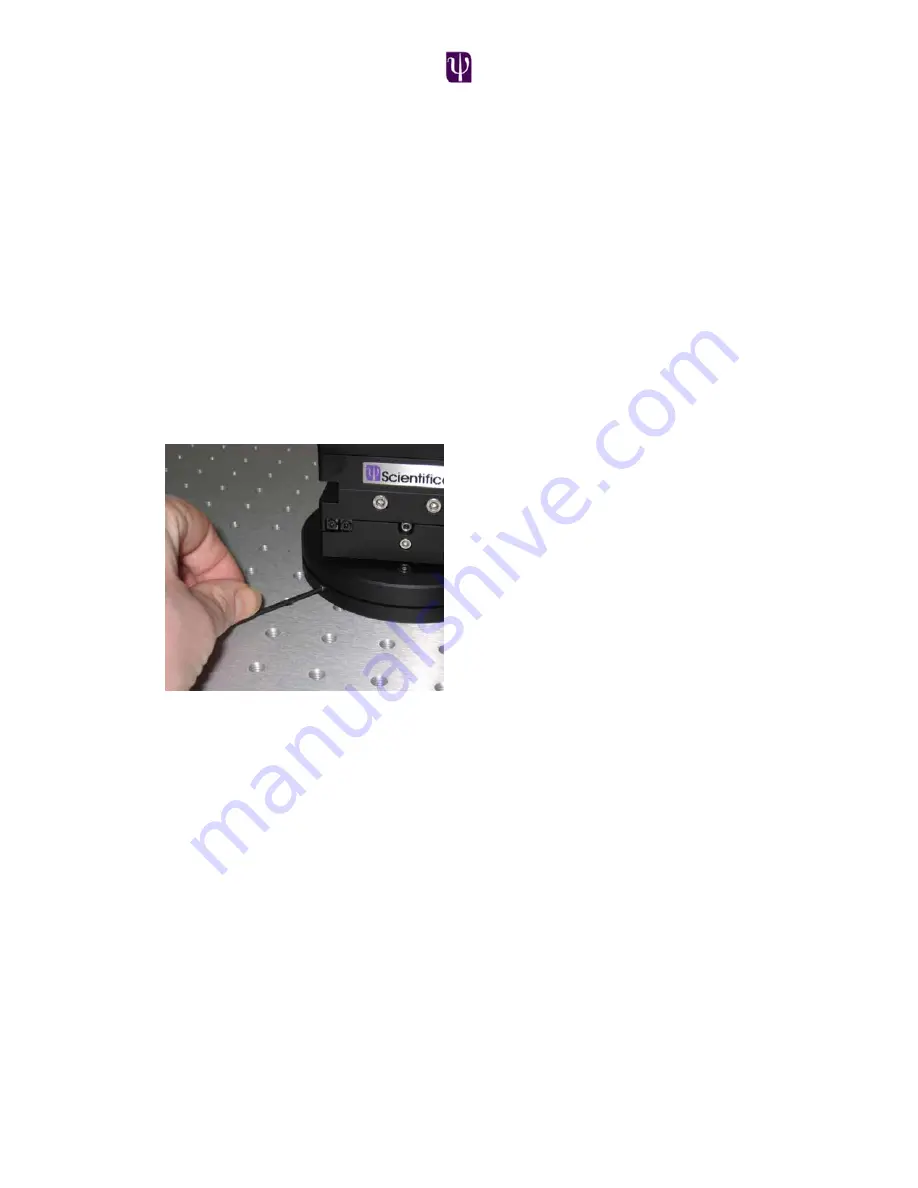
-
6 –
Setting the rotation stages
Each PatchStar manipulator includes two rotation stages which have user
settable stops. The rotary base has two magnetic stops which allow the user to
rotate the manipulator away from the experiment and then return to the original
position without having to undo any locking mechanism or use any tools. The
vertical rotary stage uses mechanical stops and a locking screw to allow the user
to rotate vertically. In addition, the vertical rotary stage incorporates a sensor that
measured the angle that the front plate is set to. The manipulator controller
automatically reads this angle and uses it to drive the manipulator in the virtual
fourth axis.
To set the stops for the rotary base; first ensure that the 2 set screws that fix the
rotary stop ring are loose thus enabling the manipulator to rotate 360º relative to
the base plate.
Rotate the manipulator until one of the magnetic stops engages with its mating
part. Rotate the manipulator (with the stop engaged) to the required orientation.
Now tighten the 2 set screws using a 1.5mm allen key to secure the rotary stop
ring. Ensure that the manipulator can be rotated in the direction and return as
required.