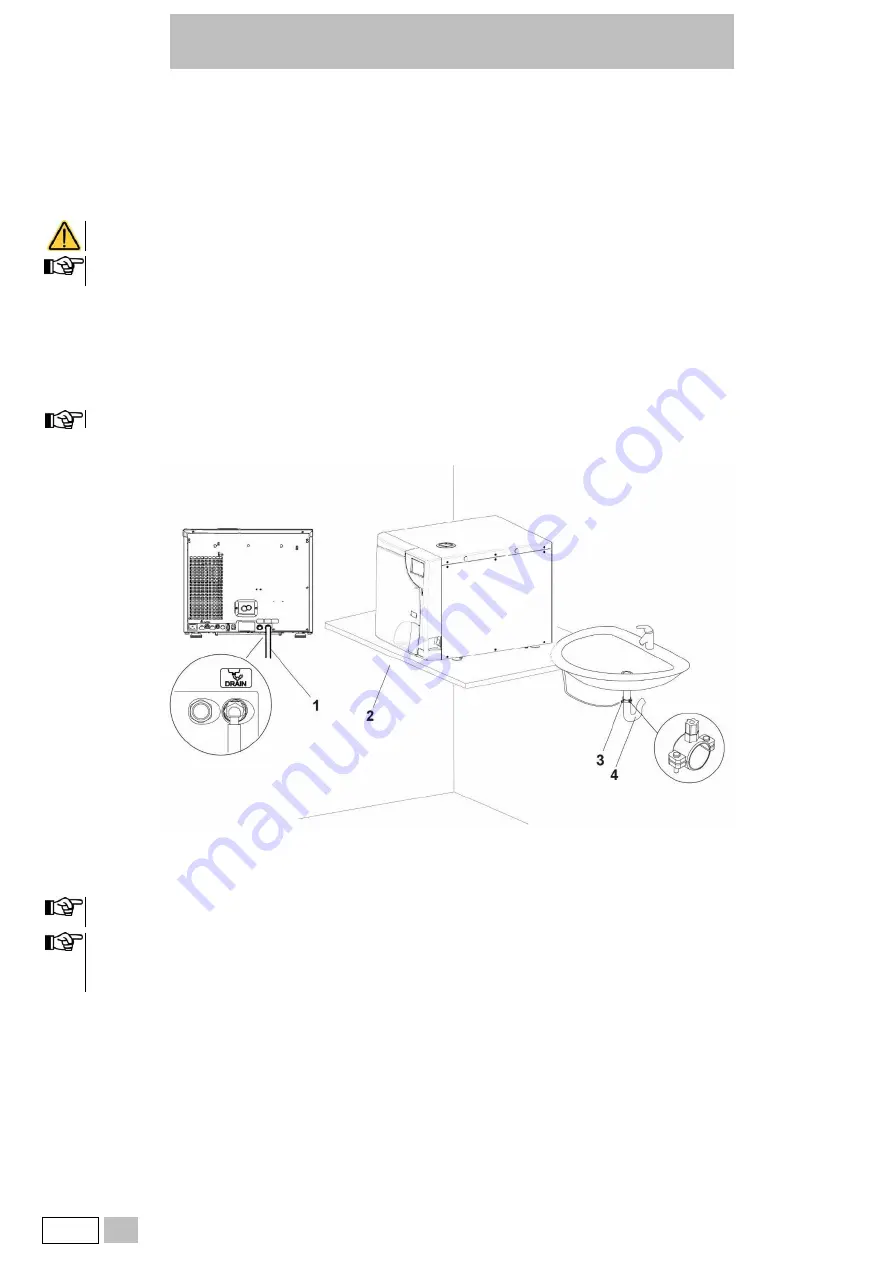
Bravo G4 17 / Bravo G4 22 / Bravo G4 28
22
EN
4.5. ELECTRICAL CONNECTIONS
This information is shown on the
back of the machine
.
The steriliser must be connected to a socket of the electric system having adequate capacity for the device and properly grounded, in accordance with
laws and/or regulations in force.
The socket must be properly protected through magneto-thermal and differential circuit breakers having the following characteristics:
•
Rated current I
n
16 A
•
Residual current I
Dn
0.03 A
The manufacturer is not responsible for any damage caused by the installation of the steriliser with unsuited and/or not properly
grounded electric systems.
Always connect the power cord directly to the power outlet.
Do not use extensions, adapters or other accessories.
4.6. DIRECT CONNECTION TO A CENTRALISED DRAINING POINT
•
Remove the cap holding clip and the cap on the rear of the autoclave;
•
Fit the plastic tube on the elbow union (supplied);
•
Fit the union and then refit the clip;
•
Fasten the clamp (supplied) to the drain siphon;
•
Cut the tube to the right length and insert its free end into the centralised draining point union locking it with the dedicated ring nut.
Make sure that the tube is not bent, crushed or obstructed in any way.
The following diagram provides an arrangement of the components:
1
At the centralised draining point;
3
Clamp;
2
Resting surface;
4
Drain siphon;
The position of the union of the centralised draining point must be lower than the resting surface of the steriliser.
Otherwise, the tank may not be emptied correctly.
If an automatic filling system (external pump or H
2
O AUX EV kit (AUX SV), Pure 100, Pure 500) is connected the use of the direct drain connection
is required.
In case of fault or failure, this system allows any excess water produced by the automatic filling system to flow into the centralised draining point,
thus preventing flooding.