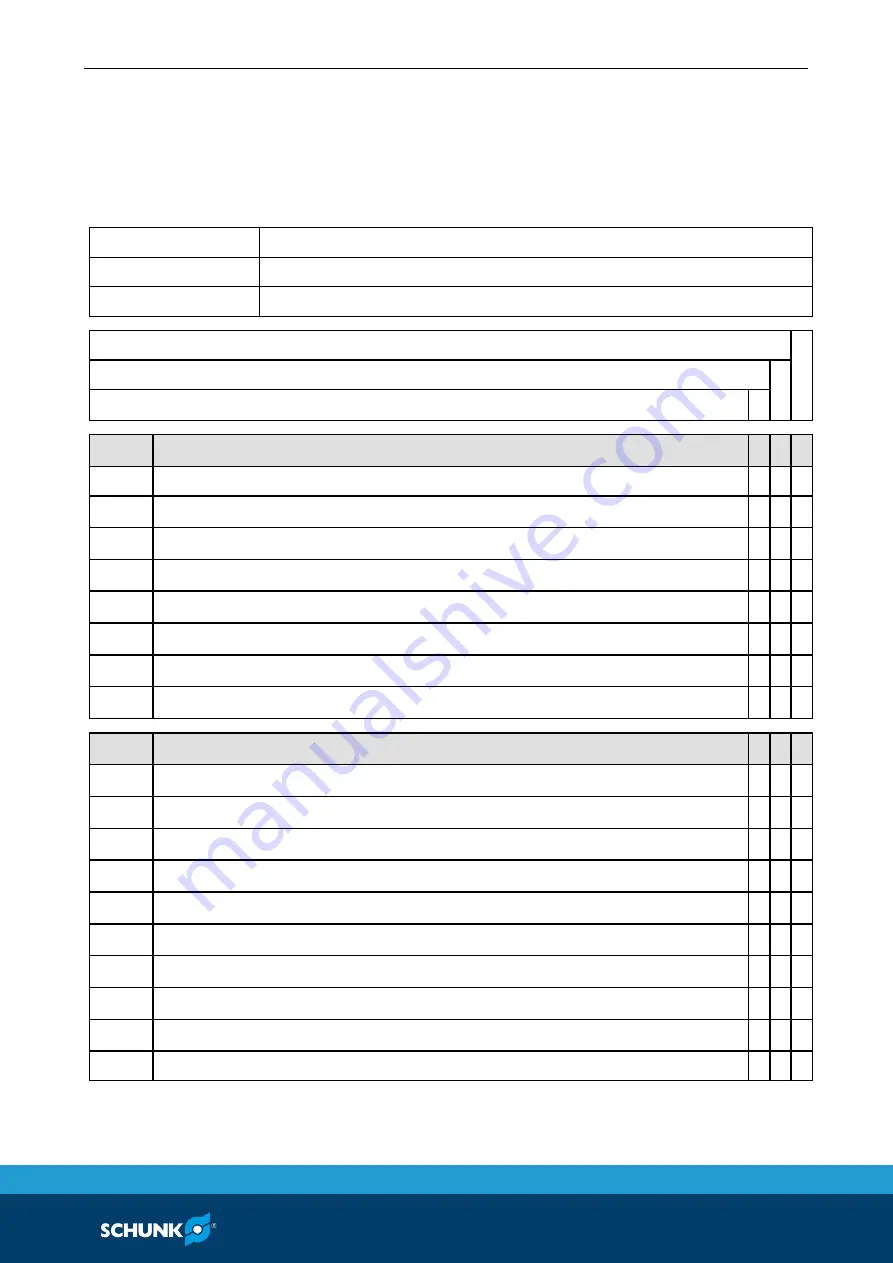
Appendix on Declaration of Incorporation, as per 2006/42/EC,
annex II, No. 1 B
04.00|1411420_NSE mini 90-25, NSE mini 90-25-V10 |en
41
Appendix on Declaration of Incorporation, as per
2006/42/EC, annex II, No. 1 B
1. Description of the basic safety and health protection requirements, as per 2006/42/EC,
Annex I, that apply to and are fulfilled for the scope of the incomplete machine:
Product designation VERO-S quick-change pallet system
Type designation
NSE-HT mini 88-20, NSE-HT mini 88-20-V10
ID number
1419192, 1419193
To be provided by the System Integrator for the overall machine
⇓
Fulfilled for the scope of the partly completed machine
⇓
Not relevant
⇓
1.1
Essential Requirements
1.1.1
Definitions
X
1.1.2
Principles of safety integration
X
1.1.3
Materials and products
X
1.1.4
Lighting
X
1.1.5
Design of machinery to facilitate its handling
X
1.1.6
Ergonomics
X
1.1.7
Operating positions
X
1.1.8
Seating
X
1.2
Control Systems
1.2.1
Safety and reliability of control systems
X
1.2.2
Control devices
X
1.2.3
Starting
X
1.2.4
Stopping
X
1.2.4.1 Normal stop
X
1.2.4.2 Operational stop
X
1.2.4.3 Emergency stop
X
1.2.4.4 Assembly of machinery
X
1.2.5
Selection of control or operating modes
X
1.2.6
Failure of the power supply
X
12