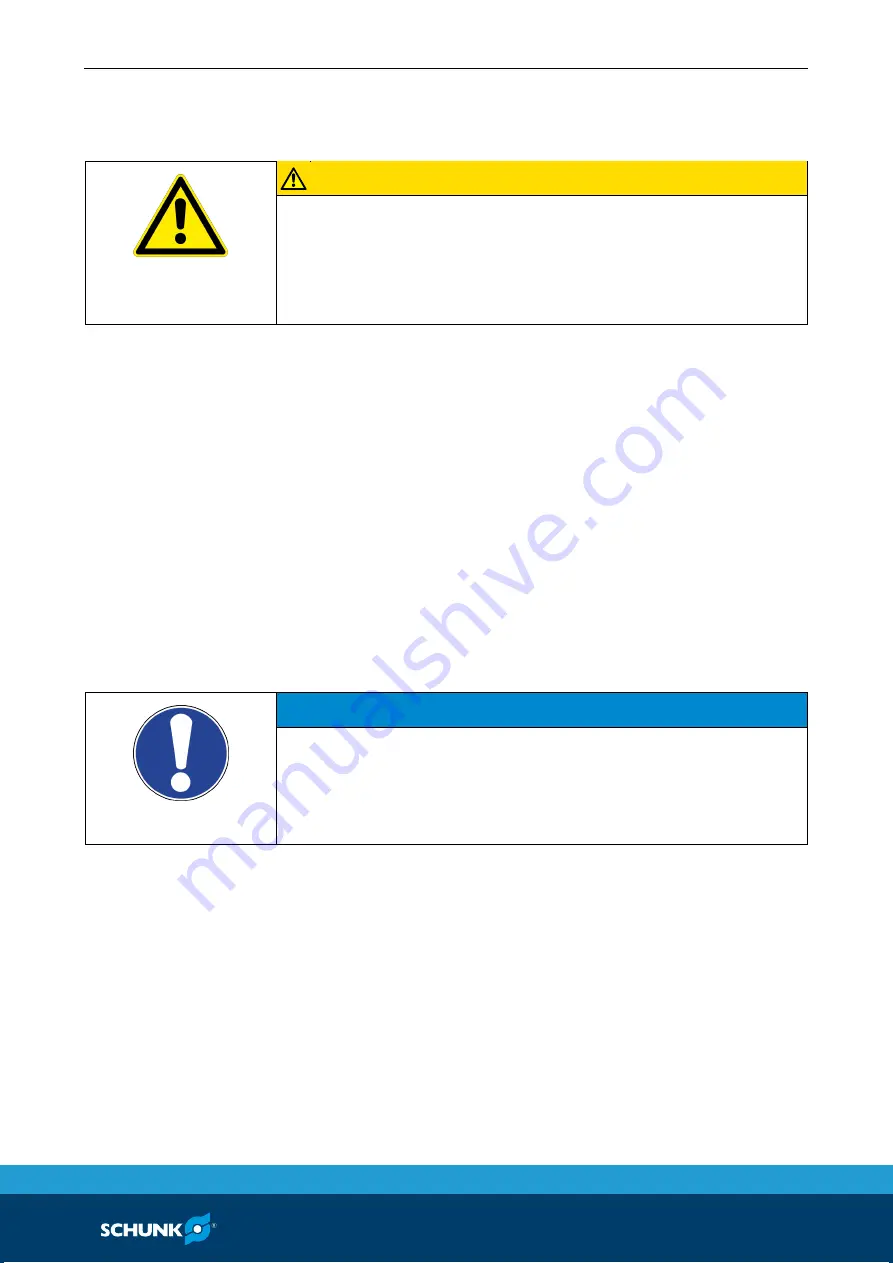
Assembly
01.00|SWS-001 |en
17
Lock/Unlock Pneumatic Connections and Valving
CAUTION
Failure to use a 4-way valve and properly vent to atmosphere
may cause the locking mechanism to operate incorrectly and
may cause the Tool Changer to not lock or unlock as expected.
This could result in damage to the product, attached tooling, or
personnel.
Air must be supplied to the “Lock” air port on the SWK to move
the internal piston, which moves the cam, and forces the locking
balls outward. The locking balls move outward until they contact
the alignment locking post on the mating SWA. This will rigidly en-
gage the SWK and SWA providing high load capacity and positional
accuracy. In a fail-safe condition the cam profile prevents the SWA
from becoming disengaged in the event that there is a loss of air in
the locked state. To unlock the SWA from the SWK, lock air must
be vented and air supplied to the “Unlock” air port on the SWK.
Air Requirements
For proper operation of the Tool Changer, the SWK must be supplied
with clean, dry, non-lubricated air supplied between 4.5 – 5.5 bar.
NOTICE
Possible damage to the locking mechanism could occur.
• Do not use the Tool Changer in the fail-safe condition for ex-
tended periods of time.
• Do not transport the Tool Changer in the fail-safe condition.
6.3
6.3.1
Summary of Contents for SWS-001
Page 35: ...Drawings 01 00 SWS 001 en 35 Drawings Tool Changer SWS 001 Tool Changer 11 11 1...
Page 36: ...Drawings 36 01 00 SWS 001 en quick change head SWK 001...
Page 37: ...Drawings 01 00 SWS 001 en 37 quick change adapter SWA 001...
Page 38: ...Drawings 38 01 00 SWS 001 en E04 Electrical Module Electrical Module 11 2...
Page 40: ...40 01 00 SWS 001 en...