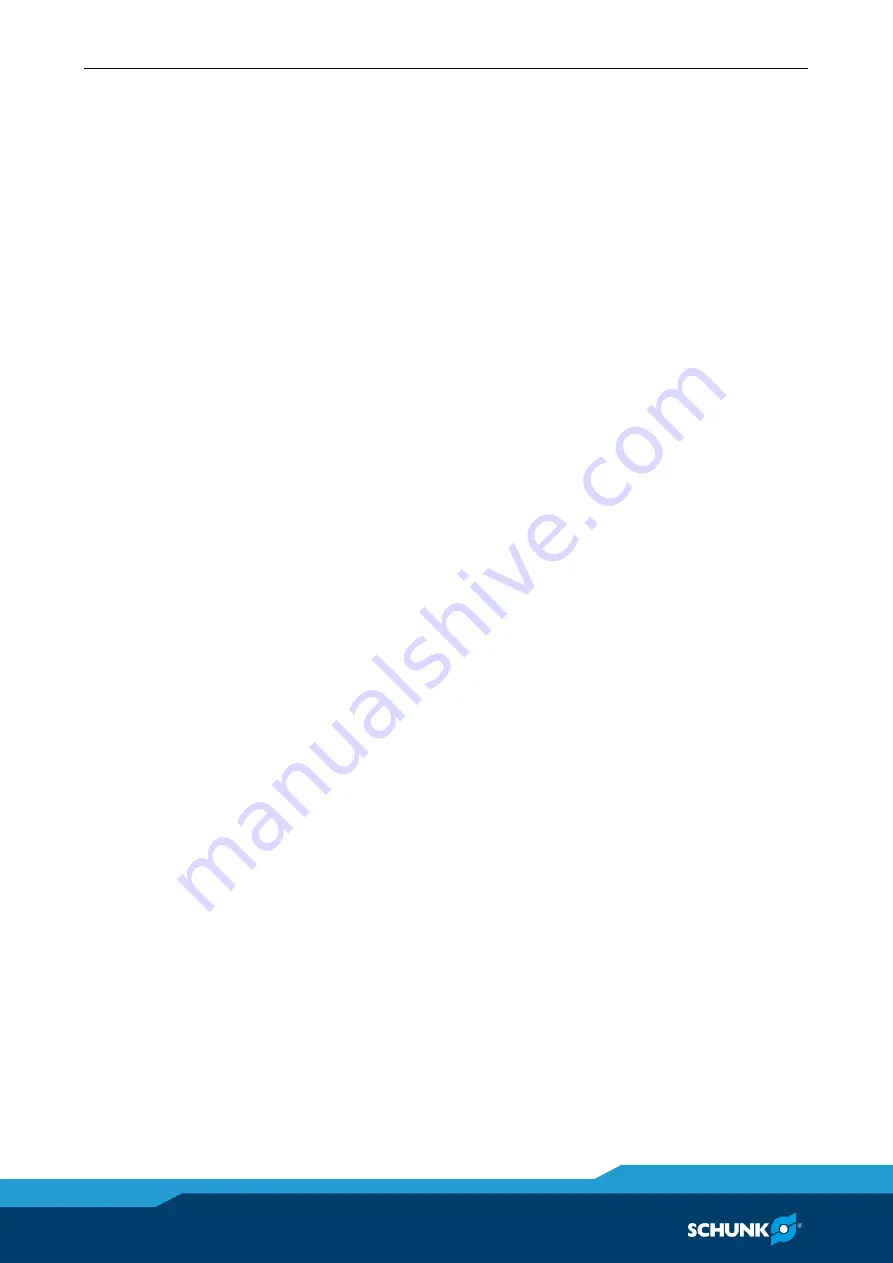
Assembly
38
04.00|0889132_ROTA TB2 / ROTA TB2 LH |en
Mounting with bracket
The console height dimension is calculated by adding together the
distances between the face side of the headstock and that of the
distributor ring. If the headstock face surface is machined, the
calculated dimension can be taken as the height dimension for the
spacing console. If the end face of the headstock is unmachined,
the height dimension should be calculated by adding together the
individual distances then subtracting 4 - 5 mm. In accordance with
the sketch overleaf, the spacing console comprises two shells and
is made of suitable steel plate. The main dimensions match the
individual chuck sizes, and can be taken from the sketch overleaf.
The spacing console can also be customized, but it should achieve
the stability of the design shown. The spacing console is mounted
using 6 M8 threaded holes in the chuck distributor ring, which
have been drilled in at a 60° angle. When the threaded mounting
holes in the headstock and the holes in the spacing console have
been drilled, the spacing console is screwed onto the distributor
ring.
The chuck with the distributor ring and the bolted-on spacing
console are now finally mounted on the spindle nose. The outer
diameter of the distributor ring matches the max. outer diameter
of the chuck. As such, the distributor ring can be centrally aligned
with the chuck using a ruler for complete accuracy, then screwed
onto it.
NOTE
The distributor ring must be aligned with the outer chuck diameter
in such a way that a radial and axial run-out tolerance of at least
0.1 mm is achieved.
When detaching the chuck from the spindle nose, the spacing
console remains attached to the distributor ring, and is only
detached from the headstock. No more adjustments must be
made to the positioning sleeves. When detaching the chuck from
the spindle nose, the spacing console remains attached to the
distributor ring, and is only detached from the headstock. No more
adjustments must be made to the positioning sleeves.
5.2.1