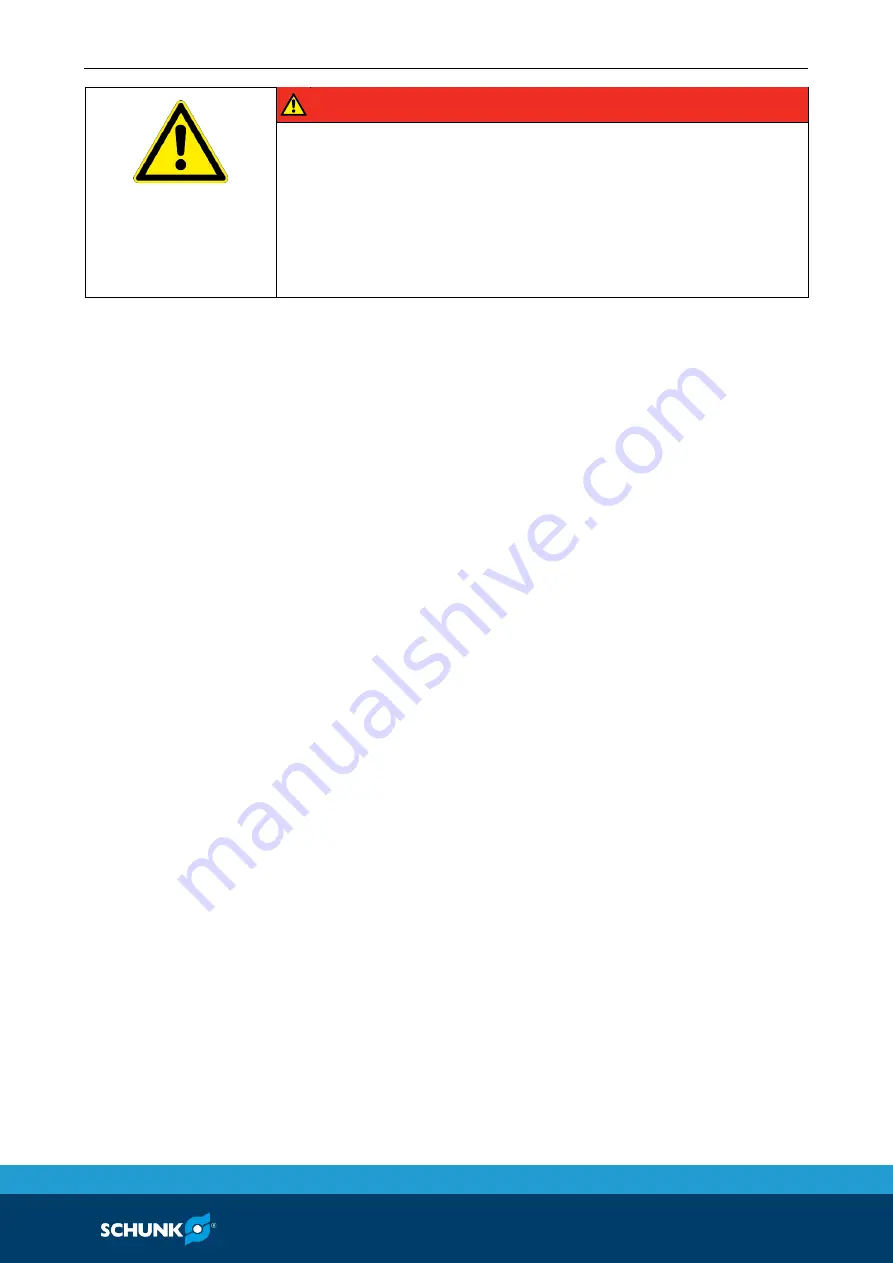
Basic safety notes
07.00|0889002_ROTA-S plus 2.0 with jaw lock |en-US
13
DANGER
Possible risk of fatal injury to operating personnel due to
toolholder failure if the maintenance and servicing instructions
for the toolholder are disregarded.
The servicing instructions specified by the manufacturer must be
complied with to ensure safe operation of the lathe chuck.
Work must be carried out by qualified specialist personnel with
the relevant safety training.
Use of special chuck jaws
When using customized jaws, please observe the following rules:
•
The chuck jaws should be designed to be as light and as low as
possible. The clamping point must be as close as possible to the
chuck face (clamping points at a greater distance lead to
greater surface pressure in the jaw guidance and can
significantly reduce the clamping force).
•
Do not use welded jaws.
•
If for constructional reasons the special chuck jaws are heavier
than the top jaws assigned to the clamping device, greater
centrifugal forces must be accounted for when defining the
required clamping force and the recommended speed.
•
Screw the jaw mounting bolts into the bore holes furthest
apart.
•
The maximum recommended speed may only be applied in
conjunction with the maximum clamping force and only with
the lathe chuck in optimum, fully functioning condition.
•
If the lathe chuck is involved in a collision, it must be subjected
to a crack test before using it again. Damaged parts must be
replaced with original SCHUNK spare parts.
•
Renew the chuck jaw mounting bolts if there are signs of wear
or damage. Only use bolts with a quality of 12.9.