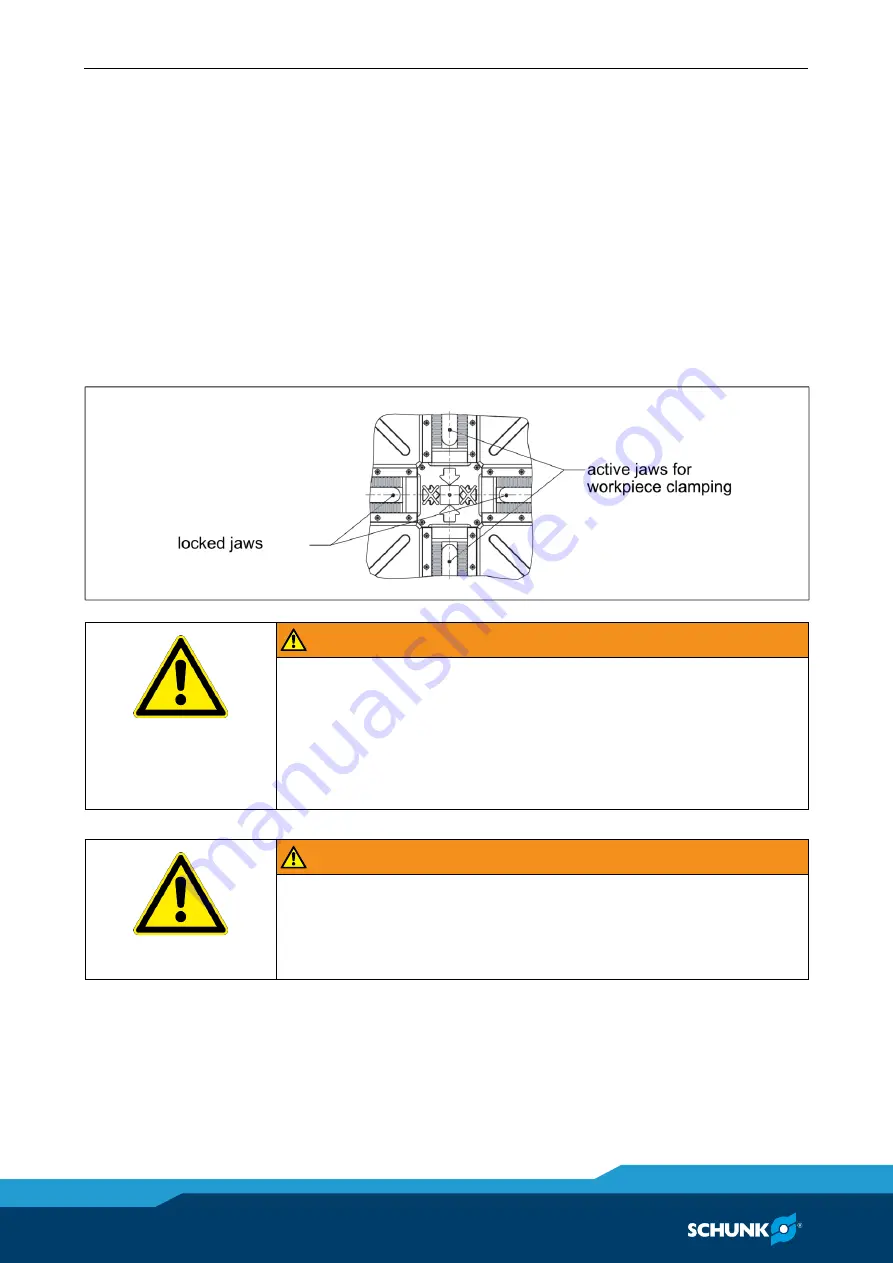
Function
44
02.00|1416054_ROTA-M2 + 2 |en-US
Assembly of the locking cover
If a clamping structure is to be realized that only contains one
active level of jaws (centric clamping vise and vise) using fixed
workpiece stops and/or stop jaws, then it is necessary to install the
locking cover:
1 Loosen the screws (item 33) and remove the cover (item 3)
with the O-ring (item 37).
2 Install the pre-assembled locking cover (consisting of items 61,
62, 72, 73) so that the arrows are in line with the jaws with
which the workpiece is to be clamped.
WARNING
The locking cover must be used when using the centric clamping
vise and vise clamping structure. This prevents the lathe chuck
gear from moving/staying against the stop.
If this is not observed, there is a danger of damaging the lathe
chuck and a risk of injury from the workpiece being flung out.
Use of the locking cover in the corresponding direction.
WARNING
Only O.D. clamping is permissible when using a locking cover.
If this is not observed, there is a danger of damaging the lathe
chuck and a risk of injury from the workpiece being flung out.
Use of the locking cover only for O.D. clamping.
6.6.2