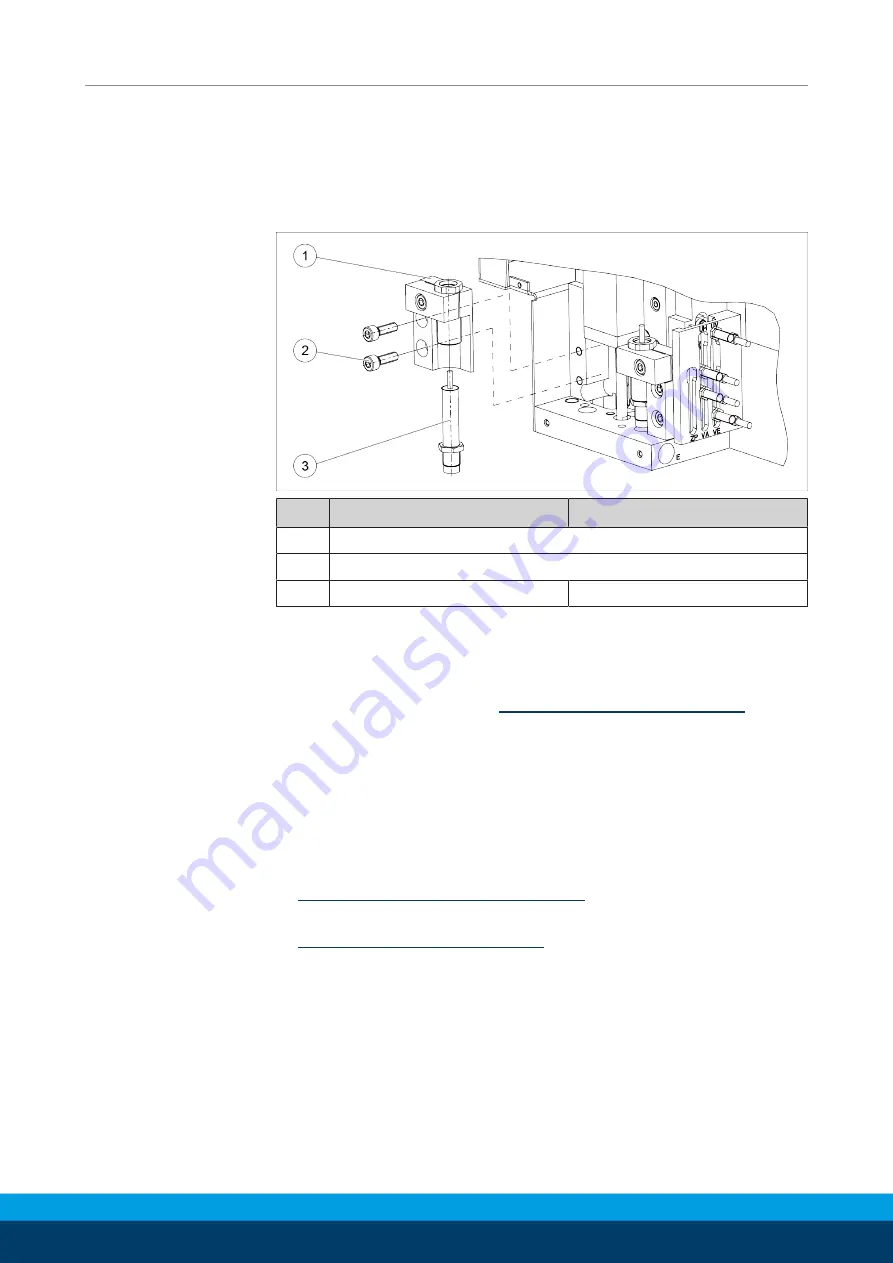
Assembly
36
06.00 | PPU-P | Assembly and Operating Manual | en | 389323
Ø
Check shock absorption during operation and correct, if necessary.
✔
The shock absorber is set correctly when the unit reaches its
end position quickly and without mechanical impact.
4.7.2 Replacement of shock absorbers
Item
PPU-P 10
PPU-P 30
1
Mount
3
Shock absorbers
2
Screw ISO 4762 M5x16
Screw ISO 4762 M6x20
Ø
Unscrew the front cover plate from the cover.
Ø
Remove the entire mounting assembly, with the clamp, sleeve
and shock absorber.
Ø
Write down dimension A
35].
Ø
Unscrew the shock absorber (110) from the sleeve and replace
with a new shock absorber.
Ø
Set to dimension A and fix with a lock nut.
Ø
Reinstall the entire mounting assembly, with the clamp, sleeve
and shock absorber, pressing the assembly onto the surface of
the base plate.
Ø
Check the position of the end position and correct if necessary
Adjustment of vertical end positions
Ø
Readjust shock absorber if necessary