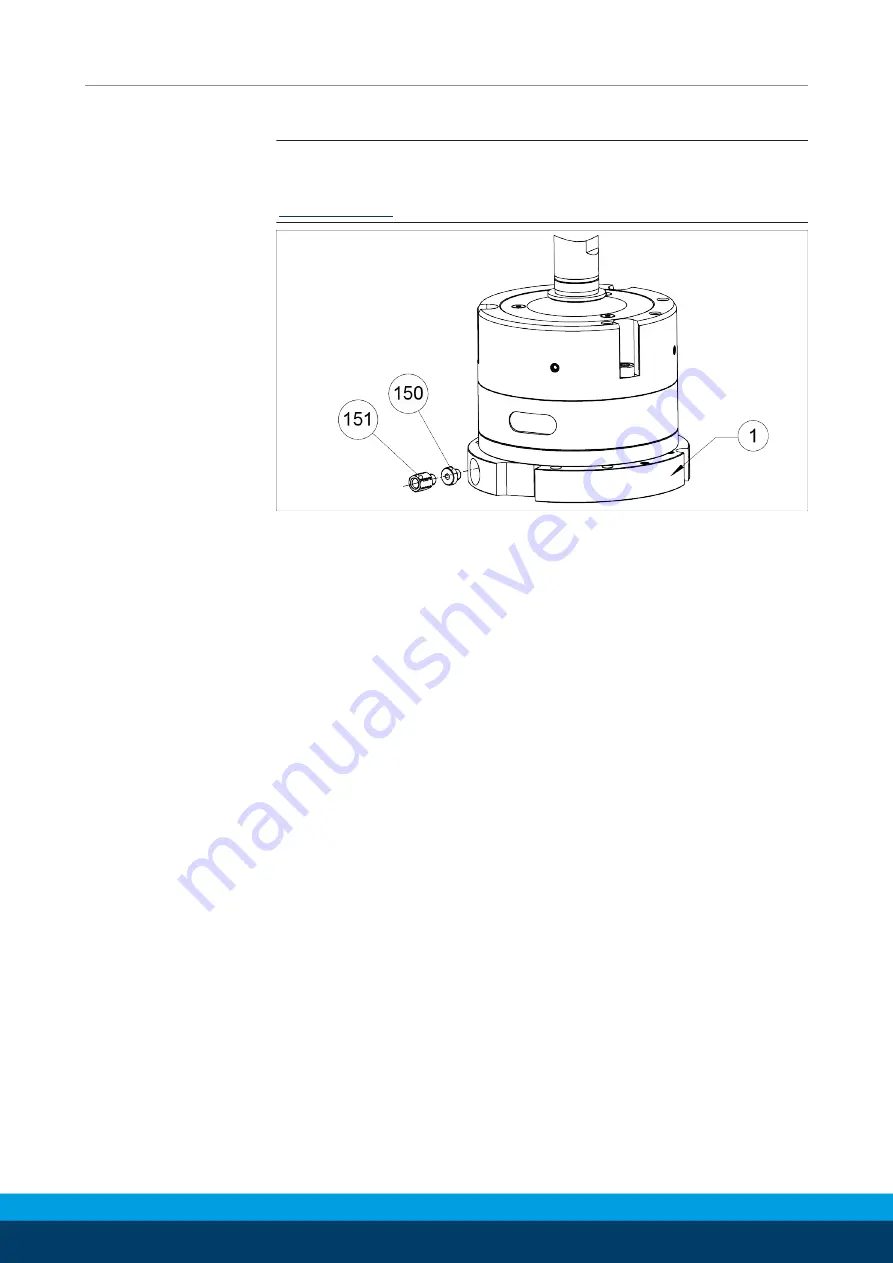
Assembly
18
03.00 | GSW-B-AGE | Assembly and Operating Manual | en | 389555
4.2 Pressure supply
NOTE
Observe the requirements for the compressed air supply,
The adapter plate GSW-B (1) is not included in the scope of delivery.
• Pressure supply with
compressed air
or
machine coolant
is
carried out by the machine spindle.
• If
compressed air
is used:
– On machines
without
check valve: Use screw plug (150).
– On machines
with
check valve: Replace screw plug (150) by
throttle (151).
• If
machine coolant
is used:
– The screw plug (150) must be replaced by the throttle (151).
• Only open the required compressed air connections to the
GSW-B-AGE and at the SCHUNK gripper. For hose-free direct
connection, please use the O-ring from the enclosed accessory
kit of the SCHUNK gripper.