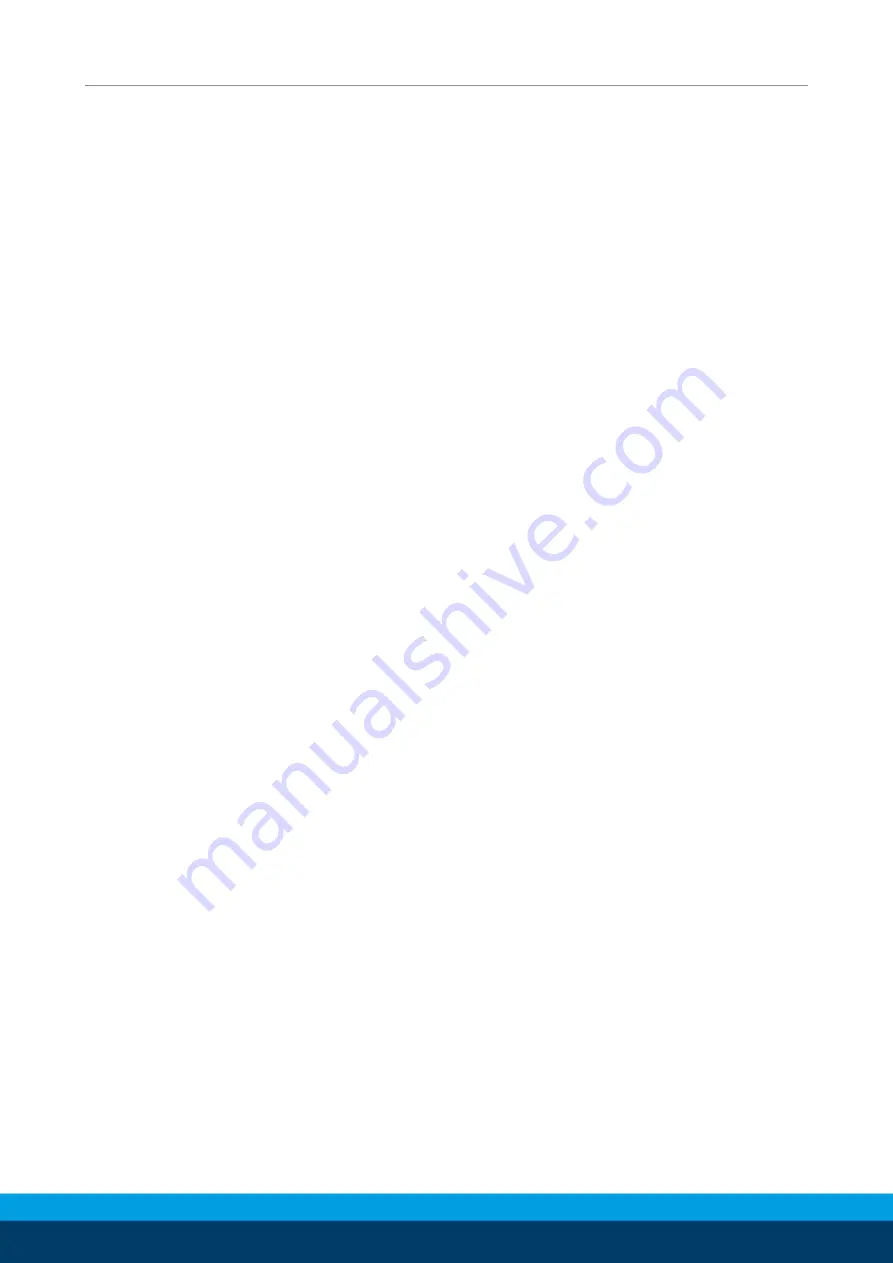
Function description and application examples
10
02.00 | FMS | Assembly and Operating Manual | en | 389074
4 Function description and application examples
4.1 Functional description
The FMS force measuring system allows you to measure forces
that act on the base jaw in the direction of the jaw movement. The
force must act centrally on the force measuring adapter.
Depending on the application, one to three active (equipped with
sensor systems) FMS-ZBA intermediate jaws are needed. The
remaining base jaws contain the passive FMS-ZBP intermediate
jaws (without sensor systems). Alternatively, the fingers can be
manufactured accordingly.
For each active intermediate jaw FMS-ZBA, an electronic processor
FMS-A1 is required for the evaluation, as well as a connection cable
FMS-AK for connecting the electronic processor with a power supply
unit and a force/torque sensor system controller (e.g. a PLC).
The active intermediate jaw is made to be deformed specifically in
the micron range. This deformation is detected by an integrated
DMS. Furthermore, the intermediate jaw is made in such a way
that a moment or force from a different direction only slightly
changes the measured value. It is therefore generally only the
gripping forces which are measured.
By means of the force/torque sensor system controller, the DMS
small signal is amplified and output to a voltage level proportional
to the gripping force.
When this is done, a positive value indicates a force acting from
the center of the gripper on the finger (e.g., a workpiece between
the gripper fingers), while a negative value indicates an external
force on the gripper fingers (e.g. reaching into a bore hole).
The output voltage level has a linear relationship to the occurring
force. However, only a change in force will be detected and not an
absolute force.
This means that when measuring, the force/torque sensor system
controller has to be reset to zero before gripping (button on the
force/torque sensor system controller or digital signal). After that,
gripping ought to be started immediately and the output
measured value ought to be evaluated.
To convert the measured value into a force, the factor included in
the data sheet and the value of the base gradient is required.
Since the pitch
m
is a function of the finger length, the distance
from which the gripping takes place is inserted into the formula
which has been provided by the factory. The distance is the length
between the base jaws of the gripper and the gripping point. The
result of this calculation is the gradient factor for the
corresponding finger length.