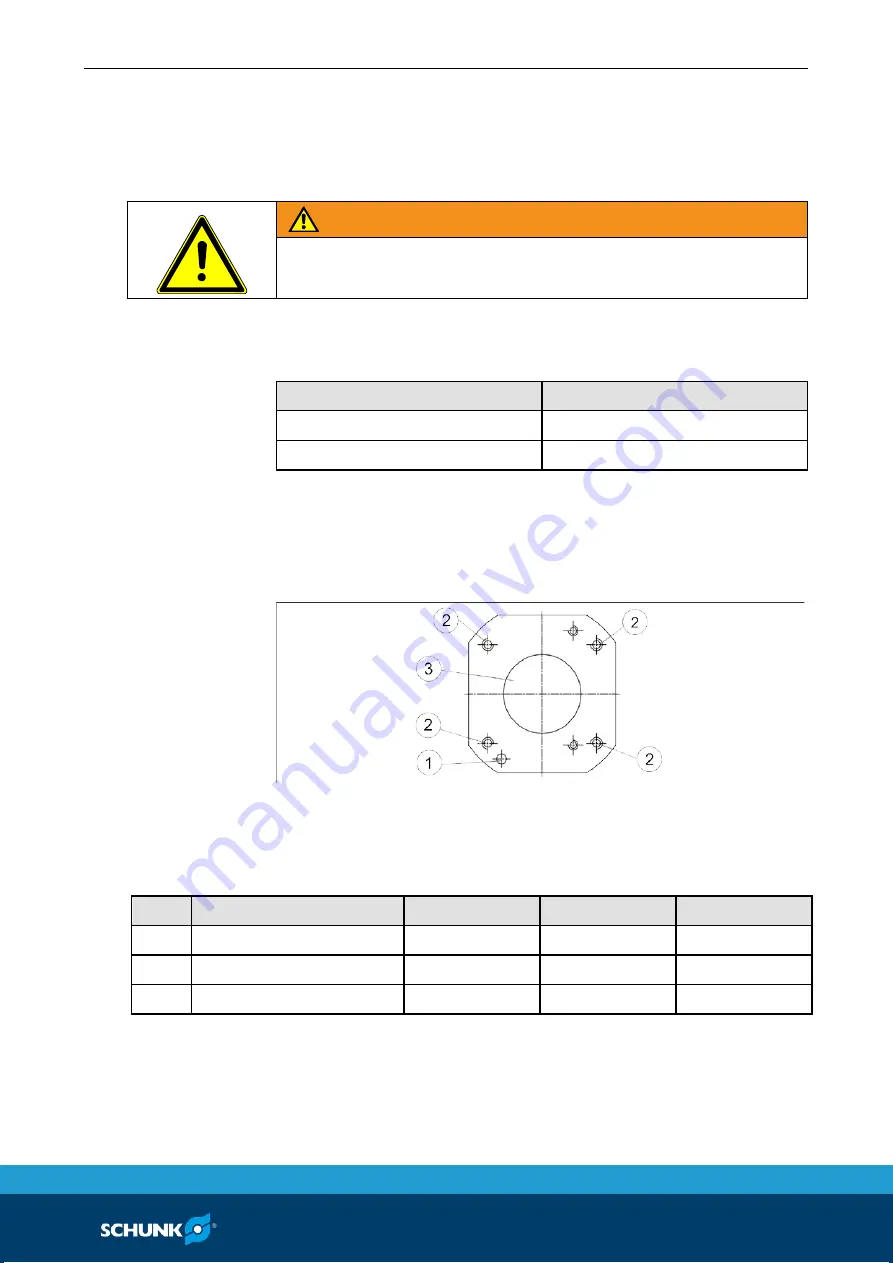
Assembly
02.02|PWG-S 40 - 80|en
13
Assembly
Mechanical connection
WARNING
Risk of injury when the machine/system moves unexpectedly!
Switch off power supply.
The values relate to the entire bolting surface.
Requirements for levelness of the bolting surface (Dimensions in mm)
Diameter
Permissible unevenness
< 100
< 0.02
> 100
< 0.05
Fasten the gripper to the base surface using four threaded holes:
A centering bore and fixing bore are in the base surface in order to
position the gripper.
Fig. 1
Maximal screw-in depth of the fastening screws provided by the
customer.
Item Type
40
60
80
1
Mounting thread
M4 (10 deep)
M5 (14 deep)
M6 (16 deep)
2
Centering bore
Ø20H7
Ø25H7
Ø40H7
3
Fixing bore
Ø4H7
Ø4H7
Ø5H7
7
7.1
Check the evenness
of the bolting surface
Mounting
www.comoso.com