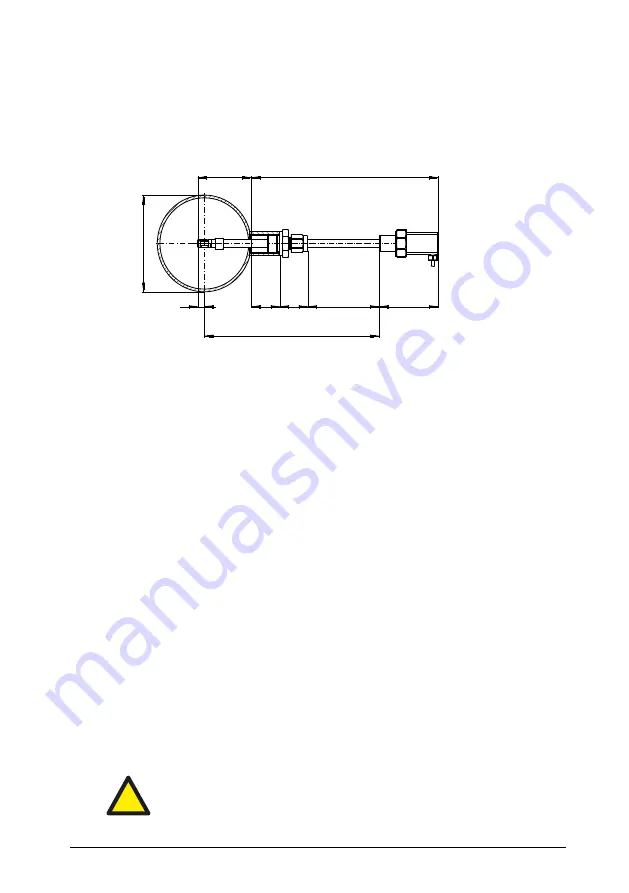
Instructions for Use
– SCHMIDT
®
Flow sensor SS 20.260
Page 9
Mounting with a through-bolt joint
The sensor is installed using a special through-bolt joint (517206). Nor-
mally, a sleeve is welded as a connecting piece onto a bore in the medium-
guiding pipe, in which the external thread (G½) of the through-bolt joint is
screwed (see Figure 3).
Figure 3
L
Sensor length [mm]
D
A
Outer diameter of the pipe [mm]
SL
Length of the weld-in sleeve [mm]
E
Sensor tube setting length [mm]
AL
Projecting length [mm]
MID
Minimum immersion depth [mm]
Bore a mounting opening in a pipe wall.
Weld connecting piece with an internal thread G½ resp. Rp½ centered
above the mounting opening of the pipe.
Recommended length of sleeve:
15 ... 40 mm
If necessary wrap thread of through-bolt joint with common sealing
tape, for example made of PTFE.
Screw thread of through-bolt joint by hand into connecting piece then
tighten it firmly with a fork wrench (SW27).
Remove spigot nut of through-bolt joint and extract both seal halves.
Remove protective cap from sensor tip and attach spigot nut on sen-
sor probe.
Insert probe in threaded part of through-bolt joint, attach seal halves
and screw on spigot nut manually to such an extent that the sensor
probe can be inserted without jamming.
In case of a longer sensor probe push it partly into the pipe as re-
quired.
Always avoid bending of the probe tube during screwing.
L
AL
66
SL
32
MET=20
8
E
D
A
!
MID = 20