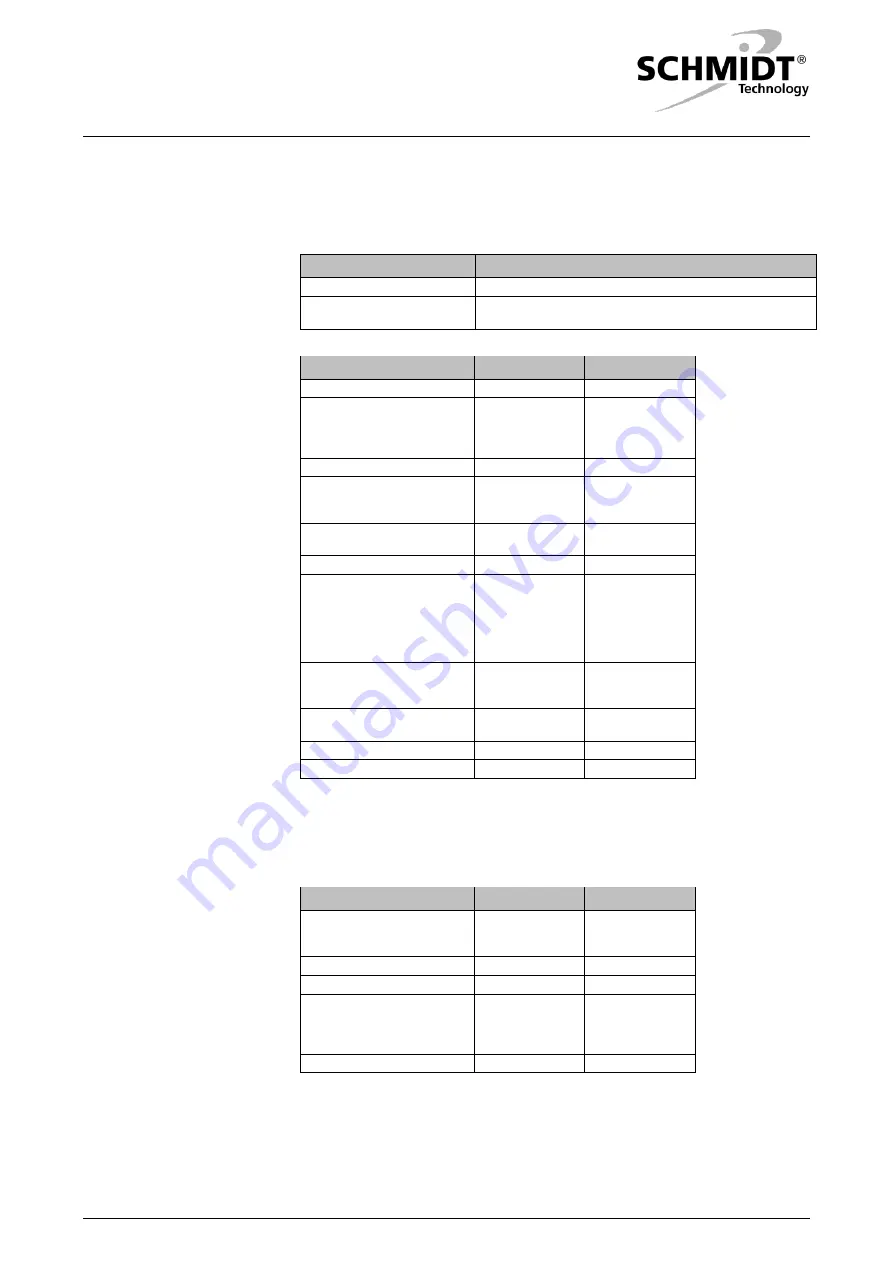
6 Appendix
SCHMIDT
®
ElectricPress 343-345
– V2.1
23
6 Appendix
6.1 Technical data
Press type
All presses listed below
Operating time
20 years
Environmental conditions
according to EN 60204-1:2007, EN 61000-6-2:2005 and EN
61000-6-4:2007
Press type
343
345
Working stroke
[mm]
0 - 100
0 - 150
Force
- F at 100% duty cycle
[kN]
- F
max
at 25% duty cycle 10 s
[kN]
2,5
4,0
6
10
Force sensor
[kN]
5
12
Resolution PDA
- Stroke
[mm/inc]
- Force
[N/inc]
0,00169
1,25
0,0024
3,0
Resolution
- Drive control
[µm]
< 1
< 1
Throat depth
[mm]
129
129
Ram
- Bore
[Ø mm]
- Dimension
[Ø mm]
- Temperature
[max.°C]
- Speed
[mm/s]
- Rotational play
[+- °]
10H7
35
60
0 - 200
0,1
20H7
40
60
0 - 200
0,1
Tool
- Weight
[max. kg]
- Dimensions
[max. mm]
10
150 x 110
15
180 x 150
Frame type
- optional
1)
7-420, 7-600
7-420
Weight
[approx. kg]
36
59
Noise level values
2)
[dB(A)]
< 60
< 60
1)
At extra cost
2)
in the idle run (without tool at th
e maximum speed) at the operator’s place (at a height of
1,6 m and approx. 1 m from the press). For measures to reduce noise, please refer to chapter
"1.4 Noise emission of the press".
Frame type
7-420
7-600
Working height
- ElectricPress (3)43
[mm]
- ElectricPress (3)45
[mm]
62 - 420
50 - 360
100 - 610
-
Frame height
[mm]
740
960
Mounting surface
[mm]
220 x 362
220 x 362
Table
- Size
[mm]
- Bore
[Ø mm]
- Height
[mm]
180 x 150
20H7
90
180 x 280
20H7
110
Weight
[approx. kg]
39
45
The performance data are related to 1000 m height above sea level.
The service life of the press amounts to 2 x 10
7
press cycles.