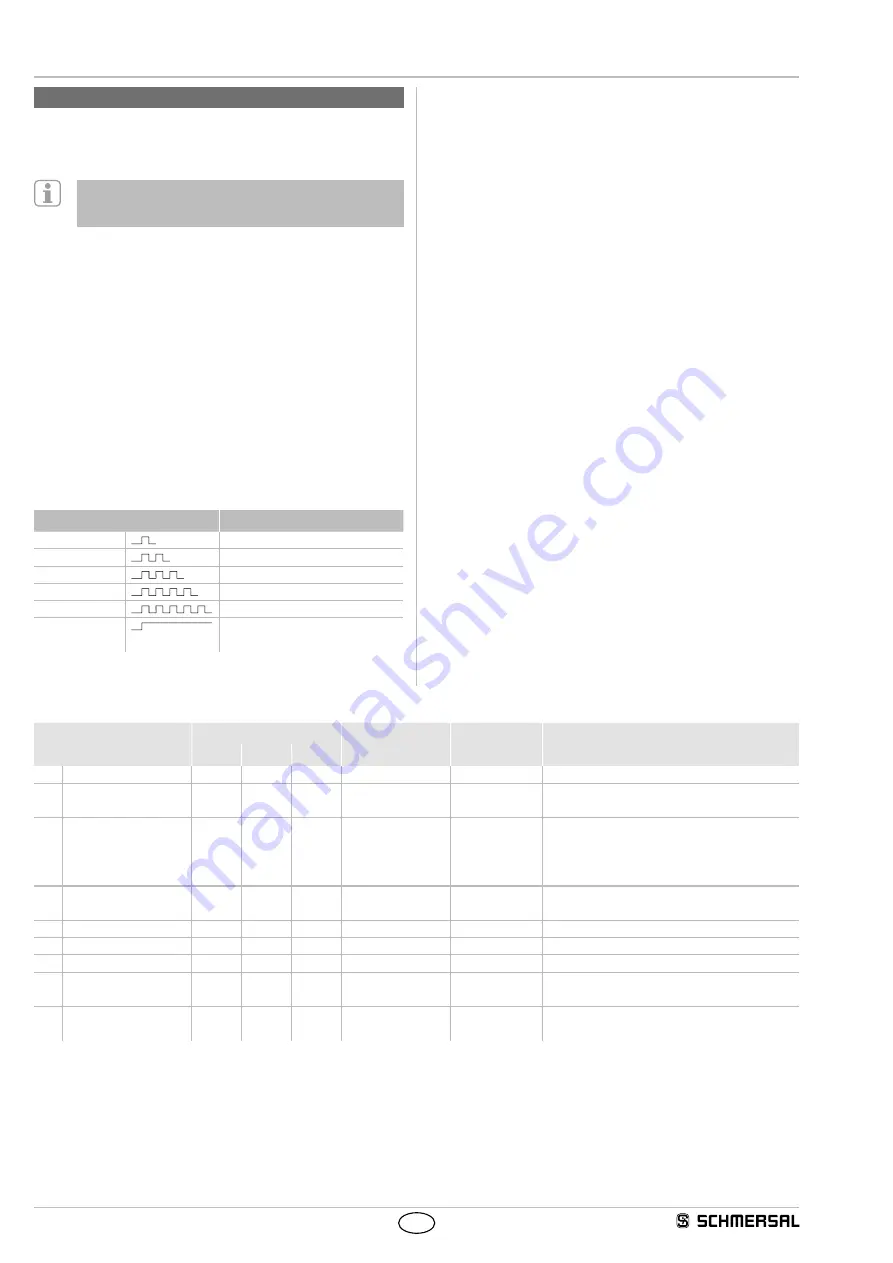
6
Operating instructions
Safety sensor
RSS 36
EN
6. Diagnostic functions
6.1 Operating principle of the diagnostic LEDs
The safety sensor indicates the operating condition and faults by means
of three-colour LEDs located in the lateral surfaces of the sensor
The following LED indicators are the same for safety
sensors with conventional diagnostic output as for those
with a serial diagnostic function
The green LED indicates that the safety sensor is ready for operation
The supply voltage is on and all safety inputs are present
Flashing (1Hz) of the green LED signals that a voltage is missing on
one or both of the safety inputs (X1 and/or X2)
The yellow LED always signals the presence of an actuator within
range If the actuator is operating near the limit of the hysteresis range
of the safety sensor, the LED is flashing
The flashing can be used to prematurely detect variations in the
clearance between the sensor and the actuator (eg sagging of a safety
guard) The sensor must be adjusted before the distance to the actuator
increases and before the safety outputs are disabled, thus stopping the
machine If an error is detected, the red LED will be activated
Flash codes red diagnostic LED
LED indication (red)
Error cause
1 flash pulse
Error output Y1
2 flash pulses
Error output Y2
3 flash pulses
Cross-wire Y1/Y2
4 flash pulses
ambient temperature too high
5 flash pulses
Wrong or defective actuator
Continuous red
Internal fault, with yellow flashing
teaching procedure
6.2 Operating principle of the electronic diagnostic output
A diagnostic output additionally indicates the operating condition
(refer to table 1) These signals can be used in a downstream control
The short-circuit proof diagnostic output OUT can be used for central
visualisation or control functions, eg in a PLC It indicates the
switching condition as shown in the table 1
Error
Errors, which no longer guarantee the function of the safety sensor
(internal errors) cause the safety outputs to be disabled within the risk
time Any error that does not immediately affect the safe functionality of
the safety sensor (eg the ambient temperature too high, interference
potential at a safety output, cross-wire short) will lead to a delayed
shut-down (refer to table 2)
After the rectification of the error, the error message is reset by opening
the corresponding safety guard
Error warning
The diagnostic output can also be used to detect clearance variations
between the sensor and the actuator in the same way as the yellow
LED An active fault causes the diagnostic output to be disabled The
safety outputs are disabled after max 30 minutes if the fault is not
rectified This signal combination, diagnostic output disabled and safety
channels still enabled, can be used to stop the production process in a
controlled manner
Table 1: Examples of the diagnostic function of the safety-sensor with conventional diagnostic output
Sensor function
LEDs
Diagnostic output Safety outputs Note
Green
Red
Yellow
Y1, Y2
I
Supply voltage
On
Off
Off
0 V
0 V
Voltage on, no evaluation of the voltage quality
II actuated
Off
Off
On
24 V
24 V
The yellow LED always signals the presence of
an actuator within range
III Actuated in limit area
Off
Off
Flashes
(1Hz)
24 V
pulsed
24 V
The sensor must be adjusted before the
distance to the actuator increases and before
the safety outputs are disabled, thus stopping
the machine
IV Error warning,
sensor actuated
Off
Flashes
Off
0 V
24 V
After 30 minutes if the error is not rectified
V
Error
Off
Flashes
Off
0 V
0 V
Refer to table with flash codes
VI Teach actuator
Off
On
Flashes
0 V
0 V
Sensor in teaching mode
VII Protection time
Flashes
Off
Off
0 V
0 V
10 minutes pause after re-teaching
VIII Error in input circuit
X1 and/or X2
Flashes
(1Hz)
Off
Off
0 V
0 V
Example: door open; a door in the safety circuit
upstream is also open
IX Error in input circuit
X1 and/or X2
Flashes
(1Hz)
Off
On
24 V
0 V
Example: door closed, a door in the safety circuit
upstream is open