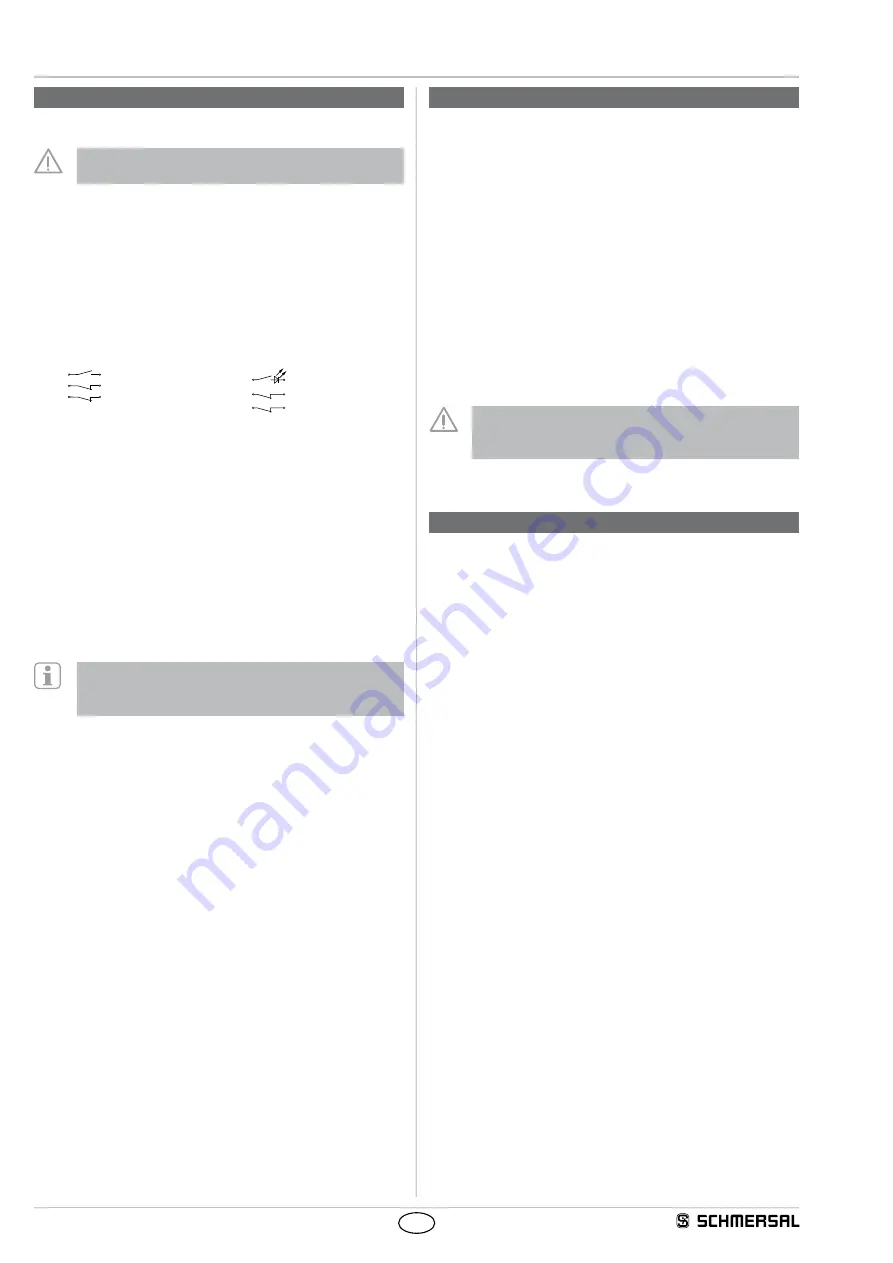
4
Operating instructions
Safety sensor
EX-BNS 303-2187
EN
4. Electrical connection
4.1 General information for electrical connection
The electrical connection may only be carried out by
authorised personnel in a de-energised condition.
The safety sensors must be wired in accordance with the specified
wire colours.
4.2 Contact variants
The contact position shows the actuated sensor function when the
safety guard is closed.
1 NO contacts / 2 NC contacts
with LED
EX-BNS 303-12Z-2187-3G/D
EX-BNS 303-12ZG-2187-3G/D
GY 13
GN 21
WH 31
14 PK
22 YE
32 BN
GY 13
GN 21
WH 31
14 PK
32 BN
22 YE
4.3 Connection
For safety-monitoring modules with two NC inputs, the wires of the
safety sensor must be wired as follows:
NO contacts: GY (13) and PK (14)
at the "NO input" of the
safety-monitoring module
NC contacts: GN (21) und YE (22)
at the "NC input" of the
safety-monitoring module
NC contacts: WH (31) und BN (32)
can be used for signalling
purposes.
Information for the selection of suitable safety-monitoring
modules can be found in the Schmersal catalogues or in the
online catalogue on our website: www.schmersal.net.
Technically, multiple safety sensors can be wired to one AES safety-
monitoring module (check if authorised!). The NO contacts are wired
parallel and the NC contacts in series. The input expander modules
PROTECT-IE-11 and -02 or PROTECT-PE-11(-AN) and -02 can be
used for joint connection up to 4 safety sensors with NC/NC or NC/NO
contacts.
Connecting more than two EX-BNS 303-12Z safety sensors to the
AES 7112 or AES 1102/1112 safety-monitoring module is not
possible. For connecting only one safety sensor: refer to the operating
instructions manual of the AES 7112 or AES 1102/1112.
Safety sensors equipped with LED's shall not be wired in series, except
for the PROTECT-IE or PROTECT-PE input expander module. As a
result of this, the luminosity of the LED's would considerably decrease
and the voltage could drop below the minimum input voltage of the
downstream safety-monitoring module.
In case of series-wiring at SRB max. 1 sensor with LED indication for U
N
.
5. Set-up and maintenance
5.1 Functional testing
The safety function of the safety components must be tested.
The following conditions must be previously checked and met:
1. The installation is executed according to the instructions
2. The connection is executed correctly
3. The safety component is not damaged
4. The system is free of dirt and soiling (in particular metal chips)
5. Check cable entry and connections in a de-energised condition
5.2 Maintenance
In the case of correct installation and adequate use, the safety sensor
features maintenance-free functionality. A regular visual inspection and
functional test, including the following steps, is recommended:
• Check the fitting of the sensor and the actuator
• Remove possible metal chips
• Check the cable for damage.
• Check cable entry and connections in de-energised condition
Adequate measures must be taken to ensure protection
against tampering either to prevent tampering of the safety
guard, for instance by means of replacement actuators.
Damaged or defective components must be replaced.
6. Disassembly and disposal
6.1 Disassembly
The safety switchgear must be disassembled in a de-energised
condition only.
6.2 Disposal
The safety switchgear must be disposed of in an appropriate manner
in accordance with the national prescriptions and legislations.