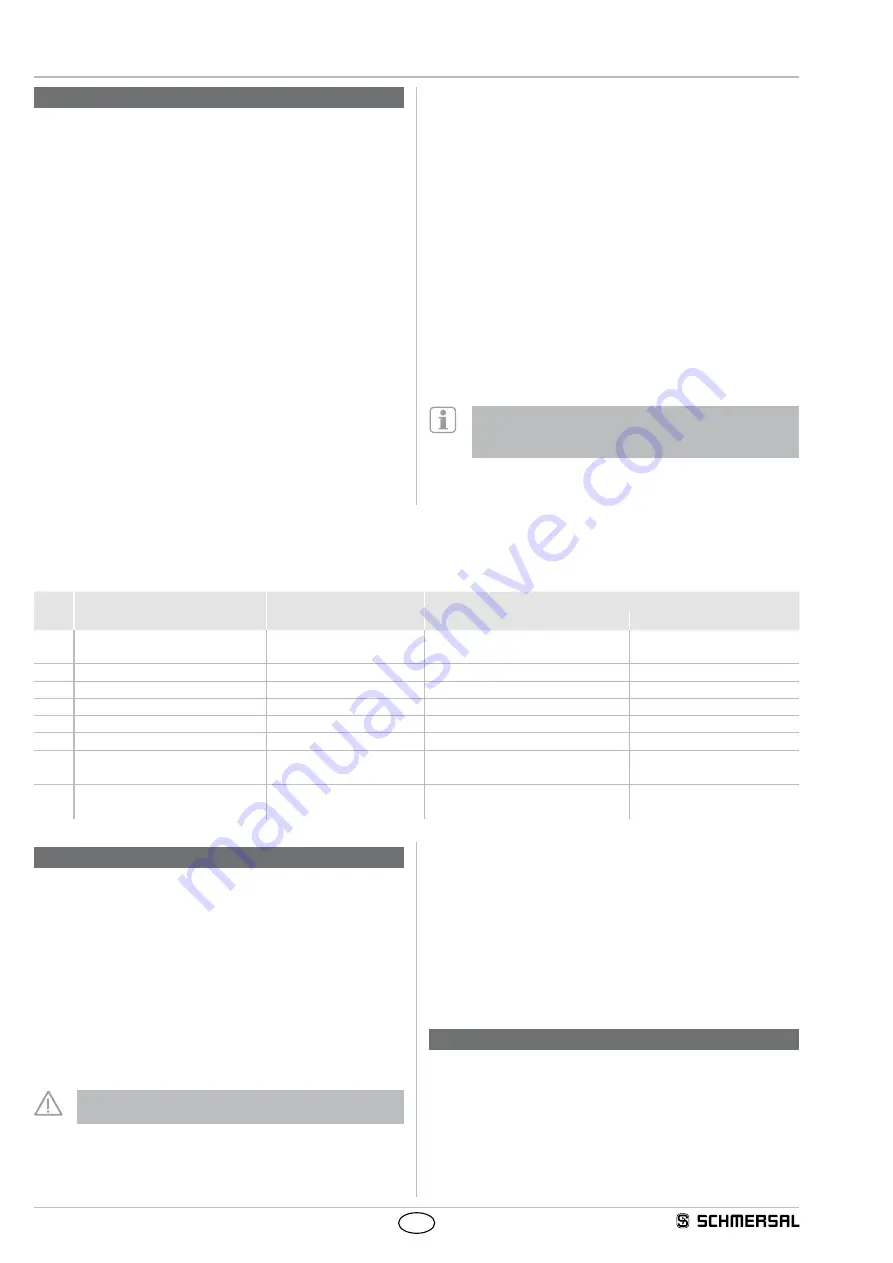
6
Operating instructions
Control panel with emergency stop
BDF200-SD
BDF200-FB
EN
6. Diagnostic functions
6.1 Diagnostic functions of SD interface
Safety switchgear devices with serial diagnostic cable have a serial
input and output instead of the conventional diagnostic output If these
safety switchgear devices are wired in series, the safety channels as
well as the inputs and outputs of the diagnostic channels are wired in
series
Up to 31 safety switchgear devices can be connected in series with
serial diagnostics For the evaluation of the serial diagnostics line either
the PROFIBUS-Gateway SD-I-DP-V0-2 or the Universal-Gateway
SD-I-U- are used This SD-Gateway is integrated as a slave in an
existing field bus system In this way, the diagnostic signals can be
evaluated by means of a PLC
The necessary documentation for the integration of the SD-Gateway is
available for download at wwwschmersalcom
The query details for each safety sensor are transmitted to the device
via one output byte of the PLC respectively
The request data for each safety sensor are transmitted to the device
through an output byte of the PLC
Should a communication error occur between the SD Gateway and the
safety switchgear, the safety switchgear retains its switch status for the
safety outputs
Diagnostic error warning and error
If an error (warning) is signalled in the response byte, detailed fault
information can be read out
Detailed information about the use of the serial diagnostics can be
found in the operating instructions of the PROFIBUS-Gateway
SD-I-DP-V0-2 and the Universal-Gateway SD-I-U-….
Error warning
A fault has occurred, which causes the safety outputs to be disabled
after 30 minutes The safety outputs initially remain enabled
This enables the shutdown of the process in a controlled manner
An error warning is deleted when the cause of error is eliminated
Error
A fault has occurred, which causes the safety outputs to be disabled
The fault is reset, when the cause is eliminated and bit 7 of the query
byte changes from 1 to 0 or the emergency stop is pressed again
Faults at the safety outputs are only deleted upon the next release,
as the fault rectification cannot be detected sooner
On the FB variant of the BDF200-SD/FB, the two diagnosis
bytes 'Error warnings' and 'Error messages' are not
transferred
Table 1: Overview of status signals, warnings or error messages of SD variant
Communication directions: Request byte:
From PLC to local safety switchgear
Response byte:
From local safety switchgear to PLC
Warning/error byte:
From local safety switchgear to PLC
Bit n° Request byte
Response byte
Diagnostic
Error warnings
Error messages
Bit 0: —
Safety output
emergency stop switched on
Error output Y1
Error output Y1
Bit 1: LED G24 red
NO contact from
pos 2
Error output Y2
Error output Y2
Bit 2: LED G24 green
NC contact from
pos 2
Cross-wire Y1/Y2
Cross-wire Y1/Y2
Bit 3: LED illuminated push button pos 2 NO contact from
pos 3
Temperature too high
Temperature too high
Bit 4: LED illuminated push button pos 3 NC contact from
pos 3
—
Error emergency stop button
Bit 5: LED illuminated push button pos 4 NO contact from
pos 4
Internal device error
Internal device error
Bit 6: —
Error warning
Communication error between field
bus Gateway and SD slave
—
Bit 7: Error reset
Error
(enabling path switched off)
Operating voltage limit
—
7. Set-up and maintenance
7.1 Functional testing
The safety function of the safety components must be tested
The following conditions must be checked and met:
• Correct fixing of the fitted component
• Check the integrity of the cables and connections
• Check the command and signalling devices for damage
• For the types with extension …-2875, the proper fitting and the
smooth operation of the pushbuttons must be checked after the
installation of the pushbutton and illuminated pushbutton caps
7.2 Maintenance
The function of the emergency stop button must be tested in regular
intervals
Maintenance:
Please observe that the safety function must
be triggered at least once a year to test the system!
In case of correct installation in accordance with the instructions
described above, the component requires little maintenance Under
extreme conditions, we recommend routine maintenance as follows:
• Check the correct fixing of the control panel
• Remove particles of dust and soiling
• Check the integrity of the cables and connections
• For the types with extension …-2875, the smooth operation of the
pushbuttons and the illuminated pushbuttons must be checked
Damaged or defective components must be replaced.
8. Disassembly and disposal
8.1 Disassembly
The safety switchgear must be disassembled in a de-energised
condition only
8.2 Disposal
The safety switchgear must be disposed of in an appropriate manner in
accordance with the national prescriptions and legislations