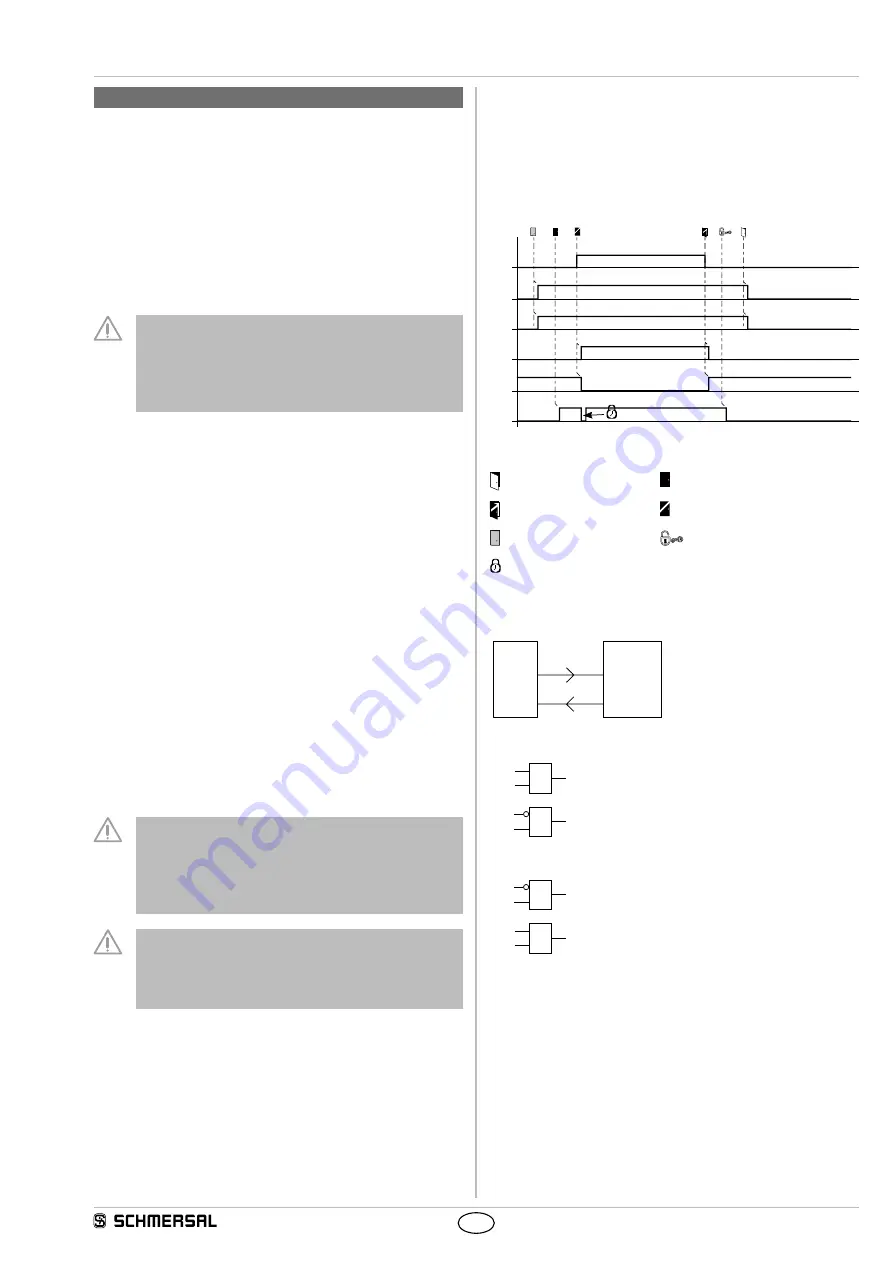
5
AZM 200 D
Operating instructions
Safety switch with interlocking function
EN
5. Operating principle and diagnostic functions
5.1 Magnet control
In the power to unlock version, the safety switch is unlocked when the
IN signal (= 24V) is set. In the power to lock version, the safety switch is
locked when the IN signal (= 24 V) is set.
5.2 Mode of operation of the safety outputs
The unlocking of the safety switch causes the safety outputs Y3 and Y4
to be disabled. As long as the actuator is inserted in the safety switch,
the unlocked safety guard can be relocked, in which case the safety
outputs will be re-enabled.
The safety guard must not be opened.
Enabling path 1 is depicted by the safety outputs Y1/Y2. This
path switches when the actuator is detected for applications
up to PL e / control category 4.
Enabling path 2 (Y3/Y4) enables (unlocks) both outputs,
when the actuator is detected AND the target is detected
AND the locked condition is detected.
5.3 Diagnostic-LEDs
The safety switchgear signals the operational state as well as errors
through three coloured LEDs installed on the front side of the device.
green
(Power)
Supply voltage on
red
(Fault)
Error (see table: Error messages /
flash codes red diagnostic LED)
yellow
(Status)
Operating condition
5.4 Operating principle of the electronic diagnostic output
The short-circuit proof diagnostic output can be used for central
visualisation or control functions, e.g. in a PLC.
The diagnostic output is not a safety-related output.
Error
Errors, which no longer guarantee the function of the safety switch
(internal errors) cause the safety outputs to be disabled. Any error that
does not immediately affect the safe functionality of the safety switch
will lead to a delayed shut-down (refer to table 2).
After fault rectification (fault at output Y1 or Y2, temperature fault), the
fault is acknowledged by opening and relocking the relevant guard door.
The safety outputs enable and allow a restart. An interlocking chain
must be permanently "locked" to enable the reactivation.
Automatic, electronic locking takes place if more than one
fault is detected at the safety outputs or a cross circuit is
detected between Y1 and Y2. This means that normal fault
acknowledgement is no longer possible. To reset this type
of interlocking, the safety switch must be isolated from the
power supply after elimination of the error causes.
The safety outputs Y3 and Y4 are not monitored. This task is
assumed by the downstream safety-monitoring module.
To test the outputs, the AZM 200 D must be operated at least
once a year (energisation of the IN input). The ambivalence
of the outputs Y3 and Y4 must be tested.
Error warning
A fault has occurred, which causes the safety outputs to be disabled
after 30 minutes. The safety outputs initially remain enabled. This
enables the shutdown of the process in a controlled manner. An error
warning is deleted in the slave when the error cause is eliminated.
Behaviour of the diagnostic output (Version ...1P2P2P)
(Example: power to unlock version)
OUT
Y4
Y3
IN
Y1
Y2
Key
Safety guard open
Safety guard closed
Safety guard unlocked
Safety guard locked
Door ajar
Actuator not inserted
Locking time: 150 ... 250 ms,
typically 200 ms
Evaluation of the diagnostic output (Version ...-1P2P2P)
SPS
SPS
AZM 200
AZM 200
I N
O U T
E 1 . 0
A 1 . 0
A 1 . 0
E 1 . 0
A 1 . 0
E 1 . 0
M 1 . 0
M 1 . 0
M 2 . 0
M 2 . 0
&
&
A 1 . 0
E 1 . 0
&
A 1 . 0
E 1 . 0
&
Door can be locked
Door can be locked
Power to unlock: IN = 0 = locking
Door is locked
Door is locked
Power to lock: IN = 1 = locking
AZM200