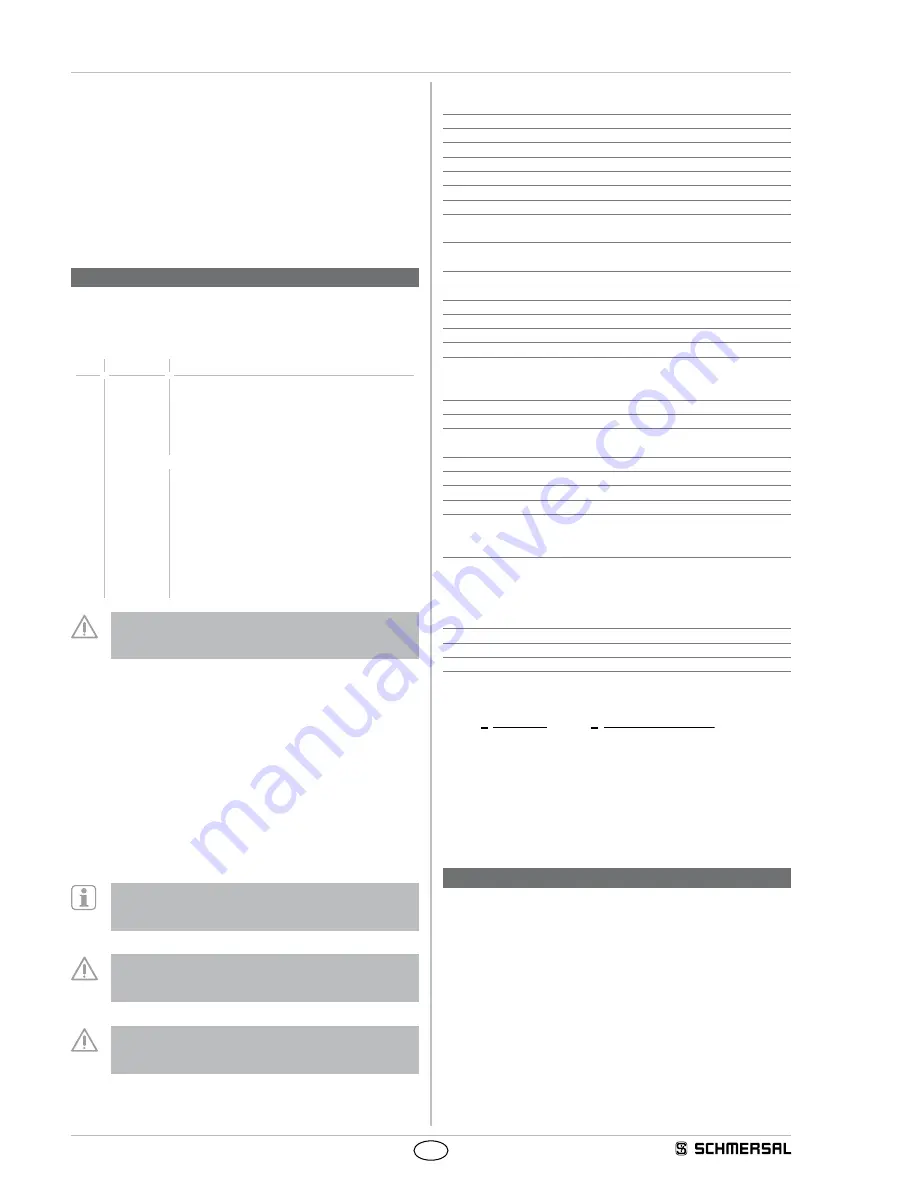
2
Operating instructions
Safety switch
AZ 16ZI
EN
1.7 Exclusion of liability
We shall accept no liability for damages and malfunctions resulting from
defective mounting or failure to comply with this operating instructions
manual. The manufacturer shall accept no liability for damages
resulting from the use of unauthorised spare parts or accessories.
For safety reasons, invasive work on the device as well as arbitrary
repairs, conversions and modifications to the device are strictly
forbidden; the manufacturer shall accept no liability for damages
resulting from such invasive work, arbitrary repairs, conversions and/or
modifications to the device.
2. Product description
2.1 Ordering code
This operating instructions manual applies to the following types:
AZ 16-
➀
ZI-
➁
-
➂
-
➃
No. Option
Description
➀
03
3 NC
12
1 NO / 2 NC
➁
ST
M12 x 1 connector bottom
STL
M12 x 1 connector LHS
STR
M12 x 1 connector RHS
➂
Actuator:
B1
Straight actuator
B1-1747
Straight actuator with magnetic latch
B1-2024
Straight actuator with slot lip-seal
B1-2053
Straight actuator with ball latch
B1-2177
Straight actuator with centering guide
B6L
Flexible actuator for left-hand side door hinge
B6R
Flexible actuator for right-hand side door hinge
➃
M16
Cable entry M16
M20
Cable entry M20
Only if the information described in this operating instructions
manual are realised correctly, the safety function and therefore
the compliance with the Machinery Directive is maintained.
2.2 Special versions
For special versions, which are not listed in the order code below 2.1,
these specifications apply accordingly, provided that they correspond to
the standard version.
2.3 Destination and use
The safety switches are suitable for safety fences, flaps and doors, which
need to be closed in order to ensure the necessary operational safety.
The safety switches are used for applications, in which the hazardous
situation is terminated without delay when the safety guard is opened.
When the safety guard is opened, the NC contacts are positively
opened and the NO contacts are closed.
The safety switchgear units are classified as type 2 switch-
gear in accordance with ISO 14119 and are rated as highly
coded.
The user must evaluate and design the safety chain in
accordance with the relevant standards and the required
safety level.
The entire concept of the control system, in which the safety
component is integrated, must be validated to the relevant
standards.
2.4 Technical data
Standards:
IEC 60947-5-1
Enclosure:
glass-fibre reinforced thermoplastic, self-extinguishing
Actuator:
stainless steel 1.4301
Coding level according to ISO 14119:
high
Actuating speed:
2 m/s
Max. switching frequency:
4000 / h
Protection class:
IP67 to IEC 60529
Contact material:
Silver
Contact type:
Change-over with double break,
galvanically separated contact bridges
Switching system:
A
to IEC 60947-5-1, slow action,
positive break NC contact
Connection:
Screw connection,
connector M12, 8 pole
Max. cable section:
0.75 ... 2.5 mm² (incl. conductor ferrules)
Rated impulse withstand voltage U
imp
:
6 kV
Rated insulation voltage U
i
:
500 V
Utilisation category:
AC-15, DC-13
Rated operating current/voltage I
e
/ U
e
:
4 A / 230 VAC
4 A / 24 VDC
- Connector:
2 A / 24 VDC
Required short-circuit current:
1000 A
Max. fuse rating:
6 A gG D-fuse
Latching force:
approx. 30 N for AZ 16ZI-1747,
up to approx. 100 N for AZ 16ZI-2053
Positive break travel:
8 mm
Positive break force:
10 N for each NC contact
Ambient temperature:
−30 °C … +80 °C
Mechanical life:
> 10
6
operations
2.5 Safety classification
Standards:
ISO 13849-1
Envisaged structure:
- Basically:
applicable up to Cat. 1 / PL c
- With 2-channel usage and
fault exclusion mechanism*:
applicable up to Cat. 3 / PL d
with suitable logic unit
B
10d
NC contact:
2,000,000
B
10d
NO contact at 10% ohmic contact load:
1,000,000
Service life:
20 years
* If a fault exclusion to the 1-channel mechanics is authorised.
MTTF
B
d x
x
h
s/h
3600
d
10d
op
op
op
n
0,1 x n
op
t
cycle
(Determined values can vary depending on the application-specific
parameters h
op
, d
op
and t
cycle
as well as the load.)
If multiple safety components are wired in series, the Performance
Level to ISO 13849-1 will be reduced due to the restricted error
detection under certain circumstances.
3. Mounting
3.1 General mounting instructions
The mounting dimensions are indicated on the rear of the component.
The enclosure must not be used as an end stop. Any mounting position.
The mounting position however must be chosen so that the ingress of
dirt and soiling in the used opening is avoided. The non-used actuator
openings must be sealed with sealing plugs after fitting.
Different actuator forms are available. The actuators B1 are preferably
used for sliding and removable safety guards; the actuators B6R and
B6L for hinged guards.