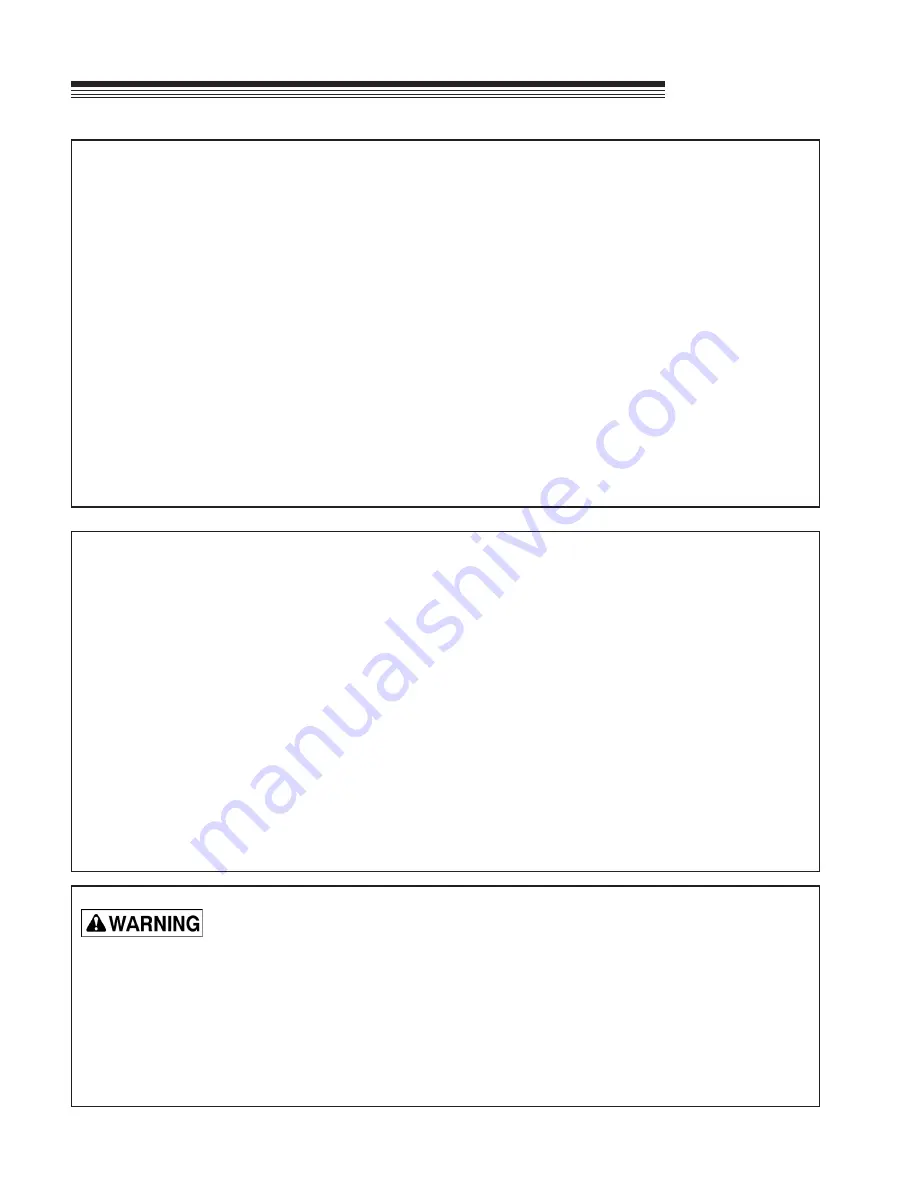
10
Hydro
Midsize
MACHINE OPERATION
BEFORE STARTING THE ENGINE:
•
Disengage cutterdeck drive.
•
Traction levers are positively locked in neutral.
•
Parking brake is on and speed selector is in neutral.
1. Check the engine oil level and add if necessary. Open the fuel valve under the fuel tank. Set the traction
levers in the neutral position and the PTO switch to the off position. Shift the speed selector to neutral.
2. For cold starts, set the throttle lever to the half open position and apply the choke.
NOTE:
For engines with combination choke/throttle controls, move throttle lever all the way forward to
choke position.
3. Pull the rope operated recoil starter firmly, or turn the key to operate electric starter (if so equipped) to
start the engine. Allow the rope to recoil slowly before releasing the handle.
4. As soon as the engine starts, gradually back the choke off from the choke position until the engine will
run with no choke at all.
OPERATING THE MACHINE
•
Practice at slow engine and speed selector speeds with the blade control disengaged until completely
familiar with the controls.
•
For normal cutting the throttle should be set at the full open position. By using the speed control lever
to speed up or slow down the machine during use, maximum control and cutting efficiency can be
maintained.
•
Using the machine at less than full throttle in heavy conditions will cause the engine to labor and result in
excessive wear.
•
For maneuvering where the speed control lever does not give the required speed, partial throttle may be
used.
•
Steering is controlled by the operation of the traction control levers. To steer the machine to the left,
reduce the drive to the L.H. wheel by pulling up the L.H. traction control lever. To steer to the right, reduce
the drive to the R.H. wheel by pulling up the R.H. traction control lever. Pulling a traction control lever up
past neutral will cause that wheel to back up.
•
To change speeds, depress the operator present controls then move speed control levers to desired
speed.
FUEL TANK
GASOLINE IS HIGHLY FLAMMABLE!
•
Fill fuel tank with good quality, clean, regular unleaded gasoline.
•
Do not use hi-test fuel.
•
Do not smoke.
•
Do not spill fuel.
•
Fill outdoors.
•
Do not overfill. Fill to 1" below bottom of filler neck to allow room for expansion.
•
USE A FUNNEL TO FILL GAS TANK