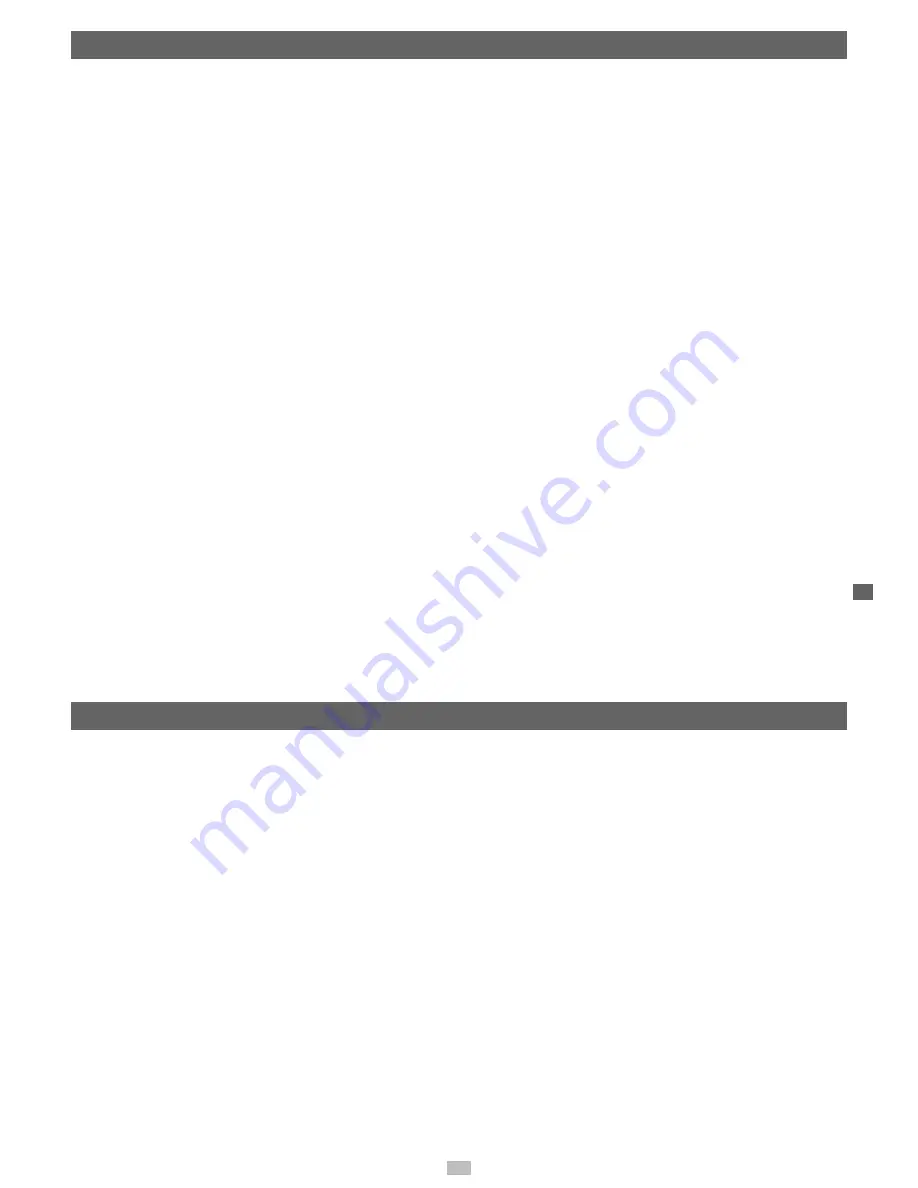
Commissioning
Before commissioning, be aware of the
safety notices.
All protective and auxiliary
equipment must be attached.
Carry out work such as re-tooling, adjusting,
measuring and cleaning only when the motor
is switched off.
Disconnect the mains plug!
Motor brake:
Before operation, test the run down time, it
should be less than 10s.
Practical example - dressing fig. 5 + 6
Warning! Never work with a jointer without the
cutterblock cover.
Jointer work – takeoff fig. 7
During jointer work, the takeoff can be
adjusted from 0 – 3 mm via the table
adjustment lever (5).
Warning! Loosen the locking handle (6)
first when adjusting, adjust the takeoff
on the scale (D) with the table adjustment
lever and re-tighten the locking handle (6).
With longer work pieces (longer than the
loading and unloading table), a dolly (special
accessory) or something similar has to be
used.
Thicknessing – machine set-up Fig. 9.0,
9.1, 9.2.
Changing from dressing to thicknessing
Unlock the jointer tables on both sides by
unclamping and removing both cam levers fig.
9 (9).
Push both tables up by the handles fig. 9 (12)
until the catch fig. 9.1 (E) clicks into place.
Rotate the ejection hood for shavings (8)
upwards until it clicks into place with the spring
U-bolt fig. 9.2 (F).
Extraction can then take place in conjunction
with an extraction unit.
Thicknessing – table adjustment fig. 10
The thicknessing table can be height-adjusted
with the handwheel (11) and it is secured
against displacement with the thicknessing
table clamp (10)
The integrated position display (G) shows the
aperture height.
One turn corresponds to 2 mm.
Always keep the thicknessing table as well as
the jointing tables free from resin.
Adjusting the scale during planing fig. 10
If there are irregularities, the scale (G) can
be adjusted. For this, loosen both mounting
screws, align the scale exactly and tighten
both screws again.
Automatic infeed in thicknessing operation
fig. 11
The automatic infeed is switched on and off
via the infeed locking lever (7).
Position top = on
Position bottom = stop
When the infeed is switched on, the wood
is automatically fed in and a precise and
consistent surface is the result.
During dressing, it is recommended to turn the
infeed off.
The infeed can also be turned off for safety
reasons.
V-belt tension motor
Warning! Always disconnect the mains plug
during all re-tooling and adjusting work.
Tension the v-belt again after 3 hours of initial
operation. The belt tension also has to be
checked regularly after 40 operating hours
and, if needed, tensioned again.
Jointer work – cutterblock cover fig. 5
When dressing up to a 100 mm work piece
width, the cutterblock cover has to cover the
work piece and the cutterblock from the top. If
the work piece is wider than 100 mm, set the
guard rail of the cutterblock cover to the width
of the work piece. Make sure you put the flat
of the hand with all five digits together and
extended on the work piece.
1 Jointing fence
2 Cutterblock cover
Joining, fig. 6
For this procedure, use the jointing fence.
Place the cutterblock cover on the jointer table
and set the guard rail to the width of the work
piece.
Press the work piece against the planing
fence and guide it over the cutterblock with
both hands. As soon as the board reaches far
enough into the unloading table, put your left
hand on it and push it over the cutter without
stopping.
Jointer work – ejection of shavings fig. 8
During jointer work, the jointer table has to be
locked.
The extraction hose must be attached to the
extraction hood.
Extraction can then take place in conjunction
with an extraction unit (special accessory).
Diameter of the extraction port – 100 mm
Operating instructions
■
SET-UP AND ADJUSTMENT OF THE MACHINE
• Carry out work such as re-tooling, adjus-
ting, measuring and cleaning only when the
motor is switched off. Disconnect the mains
plug and wait for the rotating tools to stop
moving.
• All protective and safety equipment must be
re-attached immediately after completing
repairs and maintenance.
•
Replace faulty planing knives (flaws or
similar) straight away. See Replacement of
knives!
• Check the effectiveness of the return pre-
vention system before every process step.
The hook-tips must be sharp.
• All protective and safety notices must be
re-attached immediately after completing
repairs and maintenance.
■
THICKNESSING AND JOINTER WORK
• Maximum revolutions of the cutterblock
4000 1/min
• The cutterblock has been manufactured in
accordance with DIN EN 847-1.
• Start the process only when full revolutions
have been reached.
• Keep the operating area of the machine free
from shavings and wood debris.
• Use an extraction unit to extract shavings
and wood dust. The flow rate at the extrac
-
tion port must be 20 m/s.
• Work only with sharpened planing knives.
Blunt planing knives increase the risk of
recoil.
• Thickenessing: Feed with thicker work piece
end at the front, hollow side downward. Ma-
chine max. 2 work piece at one time, feed
on both outer sides.
• When working on longer work pieces
(longer than the loading table), use dollies
(special accessory).
• Dressing: When dressing up to a 100 mm
width work piece, the cutterblock cover has
to cover the work piece and the cutterblock
from the top. If the work piece is wider than
100 mm, set the guard rail of the cutterblock
cover to the width of the work piece. Make
sure you put the flat of the hand with all five
digits together and extended on the work
piece.
• Joining: The work piece is positioned
against the jointing fence. Set the guard rail
of the cutterblock cover to the width of the
work piece and place it on the table.
• Dressing and joining of small cross sections
(slats): During dressing, the work piece is
pushed forwards with hands sitting flat on
it, as is the case with work pieces up to a
width of 100 mm. During joining, the work
piece is pushed against the stop with both
hands, fists closed, and pushed forwards.
The guard is positioned at the fence and lies
on the work piece.
• Dressing and joining of short work pieces
(min. length 150mm): During dressing, the
work piece is pressed on the loading table
with a flat hand and pushed forwards with
the push block guided by the right hand. The
left hand glides over the guard. As soon as
the work piece lies on the unloading table,
the pressure from the left hand is changed
to the unloading table. During joining, the
work piece is pressed against the fence and
the table with the left hand, fist closed, and
GB
19
Summary of Contents for plana 3.1c
Page 4: ...1 1 3 4 2 6 5 12 10 8 9 13 7 11 4...
Page 5: ...2 2 5 3 3 1 A B C 3 4 5 2 1 6 2 1 7 5 6 D 8 D 5...
Page 6: ...9 9 1 9 2 10 11 12 12 1 13 12 9 E 8 7 K L M F G 10 11 D 6...
Page 23: ......
Page 25: ......