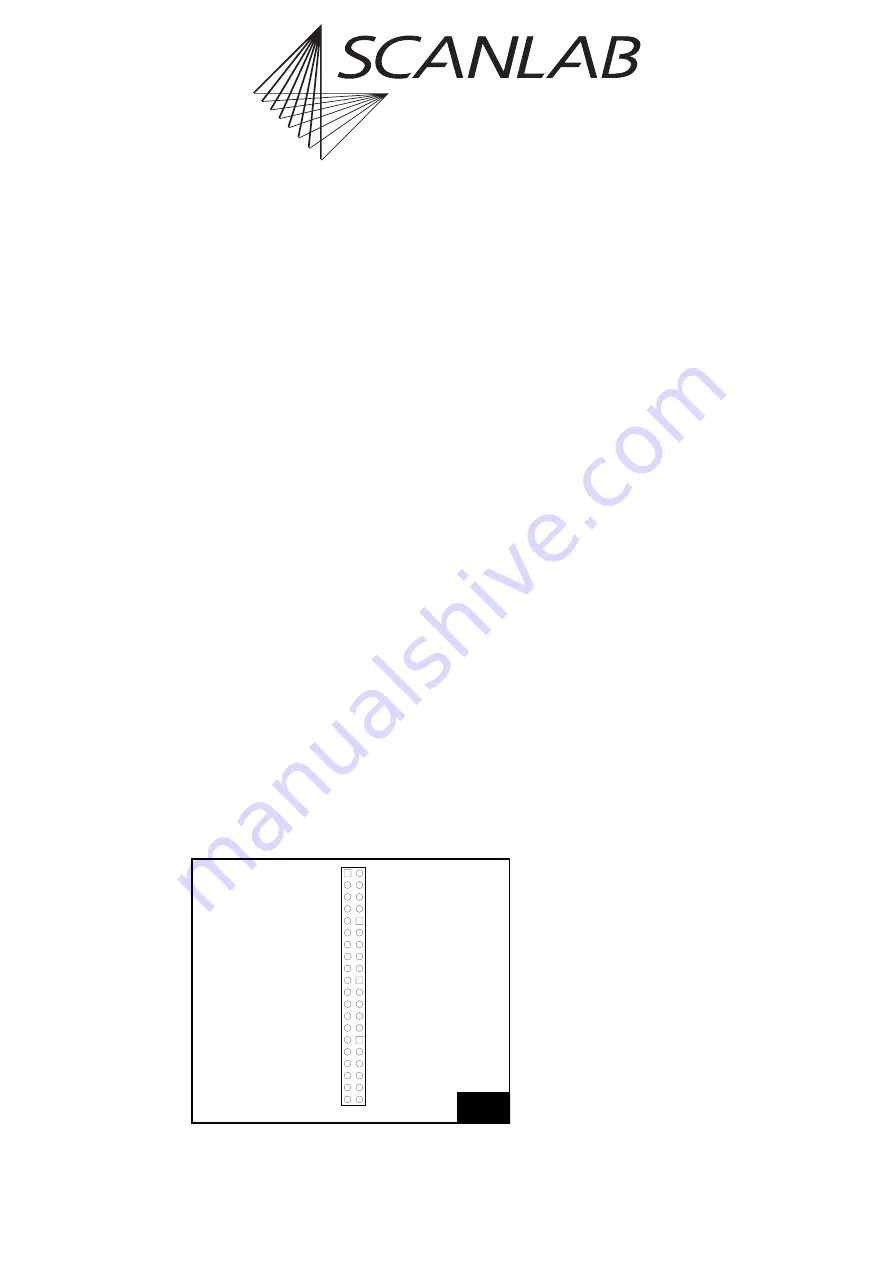
RTC
®
4 PC Interface Board
Rev. 1.3 e
6 Electrical Connections
56
innovators for industry
6.6 Optical Data Interface
(Optional)
Optionally, the RTC
®
4 is equipped with an optical
data interface and ST ports for data transfer via a
duplex optical fiber cable (see
This allows scan systems to be controlled via optically
transferred signals. Optical data transfer provides the
advantages of immunity to electrical interference
(ESD and EMC) and complete galvanic separation.
The data interface converts electrical signals into
optical signals with a wavelength of 650 nm. The
optical signals are guided along a polymer optical
fiber cable to an optical data interface (optionally)
installed in the scan system, where they are converted
back into electrical signals. Compliant with the
XY2-100-O protocol, the optical signals are trans-
ferred bidirectionally every 10
µ
s over 3 data
channels.
The optical fiber cable is not included in the package.
SCANLAB recommends use of a 1 mm diameter
duplex polymer optical fiber (POF) cable with a
maximum length of 30 m. The optical fiber cable
must be fitted with two ST plugs at each end. Use the
optical fiber cable to cross-connect (
not
1:1) both ST
ports of the RTC
®
4’ primary scan head connector
with both ST ports of the scan system.
If the signals for a second scan head are enabled, also
a second scan system can be connected via a polymer
optical fiber.
6.7 EXTENSION 1 Connector
The EXTENSION 1 connector provides a 16-bit digital
TTL input and a buffered 16-bit digital TTL output.
The pin-out is shown in
16-Bit Digital Input and Output
The 16-bit digital output port can be used, for
example, for controlling a workpiece transport
system. Signals of the transport system, of workpiece
recognition systems etc. can be read via the 16-bit
input port. A group of related commands facilitates
straight-forward incorporation of port-based opera-
tions into application programs:
The
and
commands specify the digital output values. The 16-
bit digital output is in high-impedance mode (tri-
state) until an initial value is assigned to it.
The
commands read
the current values of the digital input or output ports.
The
and
commands allow digital output values to be influ-
enced by digital input values: Depending on the
current value of the digital input, individual bits of
the output port are set or cleared.
The commands
can be used to call subroutines or jump within a list
– depending on the current value of the digital input
(also see
"Structured Programming", page 45
BUSY Status
The BUSY status signal, available at pin (36), is HIGH
when an application is currently executing.
28
DIGITAL OUT0
(1)
DIGITAL OUT1
(3)
DIGITAL OUT2
(5)
DIGITAL OUT3
(7)
DIGITAL OUT4
(9)
DIGITAL OUT5 (11)
DIGITAL OUT6 (13)
DIGITAL OUT7 (15)
DIGITAL OUT8 (17)
DIGITAL OUT9 (19)
DIGITAL OUT10 (21)
DIGITAL OUT11 (23)
DIGITAL OUT12 (25)
DIGITAL OUT13 (27)
DIGITAL OUT14 (29)
DIGITAL OUT15 (31)
DO NOT CONNECT (33)
DO NOT CONNECT (35)
+5 V (37)
GND (39)
(2)
DIGITAL IN0
(4)
DIGITAL IN1
(6)
DIGITAL IN2
(8)
DIGITAL IN3
(10) DIGITAL IN4
(12) DIGITAL IN5
(14) DIGITAL IN6
(16) DIGITAL IN7
(18) DIGITAL IN8
(20) DIGITAL IN9
(22) DIGITAL IN10
(24) DIGITAL IN11
(26) DIGITAL IN12
(28) DIGITAL IN13
(30) DIGITAL IN14
(32) DIGITAL IN15
(34) DO NOT CONNECT
(36) BUSYOUT
(38) +5 V
(40) GND
Pin-out of the 40-pin EXTENSION 1 connector