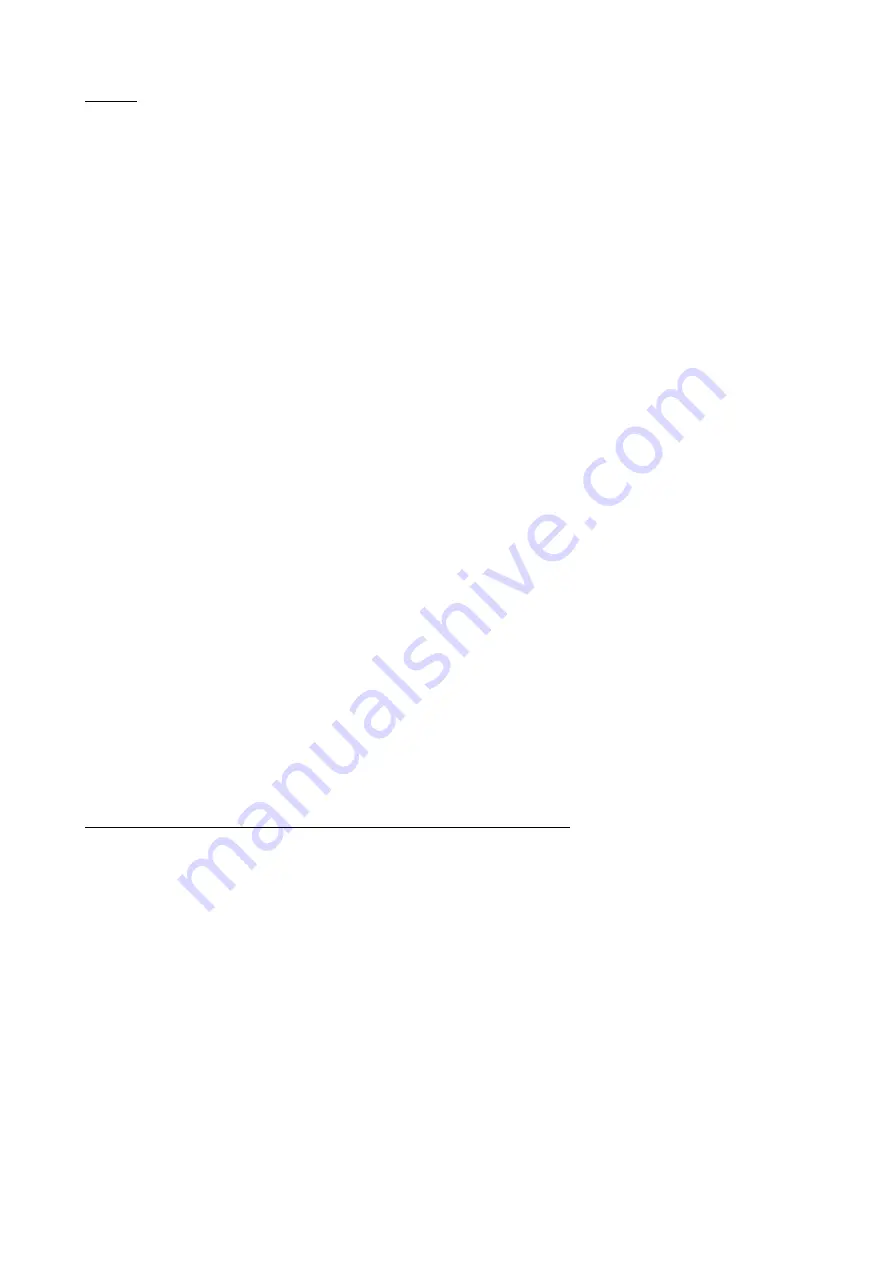
47/90
User manual SCAIME:
NU-Soft-eNod4F-E-0716_235704-C.doc
Warning: an input can only be assigned to
suspend/resume batch
, with a functioning in a bistable mode and on rising
or falling front depending on the selected logic.
10.3.25
Emptying hopper (cleaning)
In loss in weight feeder mode, this command allows to automatically emptying the hopper (or silo) in preparation of a
cleaning process or for changing the dosing product. Dosing is running and totalization works until the gross weight
reaches the
empty hopper level
.
An input can be assigned to
start/stop hopper emptying
, with a functioning in a bistable mode and on rising or falling
front depending on the selected logic. It's not possible to suspend an emptying.
The command
start/stop dosing
or
suspend/resume batch
systematically lead to the emptying shutdown.
10.3.26
Refilling start
This command allows refilling activation. Refilling stops when the gross weight reaches the
refilling high level
minus
the
refilling inflight value
. Inflight value is not adjusted automatically at each cycle.
Refilling can also be initiated/stopped by an input assigned to
start/stop refilling
, with a functioning in a bistable
mode and on rising or falling front depending on the selected logic.
10.3.27
Refilling stop
This command will stop refilling immediately. Refilling can also be initiated/stopped by an input assigned to
start/stop
refilling
, with a functioning in a bistable mode and on rising or falling front depending on the selected logic.
10.3.28
Learning cycle on next cycle
If
PID activation
,
smart refill mode
and
acquisition of flow rate refill references on learning cycle
options are
activated, this command will launch a learning cycle after the next refilling phase. This smart refill mode compensates
for the flow rate variation due to the product thrust in the hopper or silo so that the flow rate always remains
constant throughout the phase. New values for
reference flow rate control output start refilling
and
reference flow
rate control output end refilling
parameters will be determined.
10.3.29
Flow rate calibration
So that
eNod4
can carry out an expected flow rate dosing in the best possible conditions, the flow rate calibration is
required. This also applies when
eNod4
is used both as constant flow rate totalizer and as loss in weight feeder.
From this calibration will depend the accuracy of the flow rate obtained and on the settling time, if a PID controller is
activated. This calibration is carried out in minimum two segments by the variable
segments number for the
calibration curve of flow rate
.
In case the extraction device has a nonlinear response it is recommended to define
maximum segments for the flow rate calibration.
In order to calibrate the flow rate, if the control of extraction device is directly provided by
eNod4
through an analog
control output in current or voltage, analog output functioning of
eNod4
must be allocated to
level on request
function first.
For each calibration point of the variable
control output value,
read the appropriate
average flow rate.
Then provide
each of the
Calibration of flow rate point n (control output)
and
Calibration of flow rate point n (flow rate value)
matching with
control output value
.
Validate the flow rate calibration by sending
calibration of flow rate
command.
Finally allocate in the end the current
or voltage analog output of
eNod4
to
flow rate control output
function
.
10.3.30
Auto Measurement in two or three points for flow rate calibration
In order to calibrate the flow rate, if the control of extraction device is directly provided by
eNod4
through
an analog control output in current or voltage, analog output functioning of
eNod4
must be allocated to
level on request
function first. There are two commands, the first allows automatic measurement of flow
rate in two points (35% & 70% of control output). The second allows automatic measurement of flow rate
in three points (20%, 50% & 80%).
At the end of procedure, the flow rate calibration is validating automatically.
10.3.31
PID parameters auto-adjustment
The configuration of the PID controller can be made in a totally automatic way. The behavior of PID controller (slow,
fast or stable) must be previously configured. You have also to configure
PID adjustment flow rate
parameter that will
be used for PID auto-adjustment.