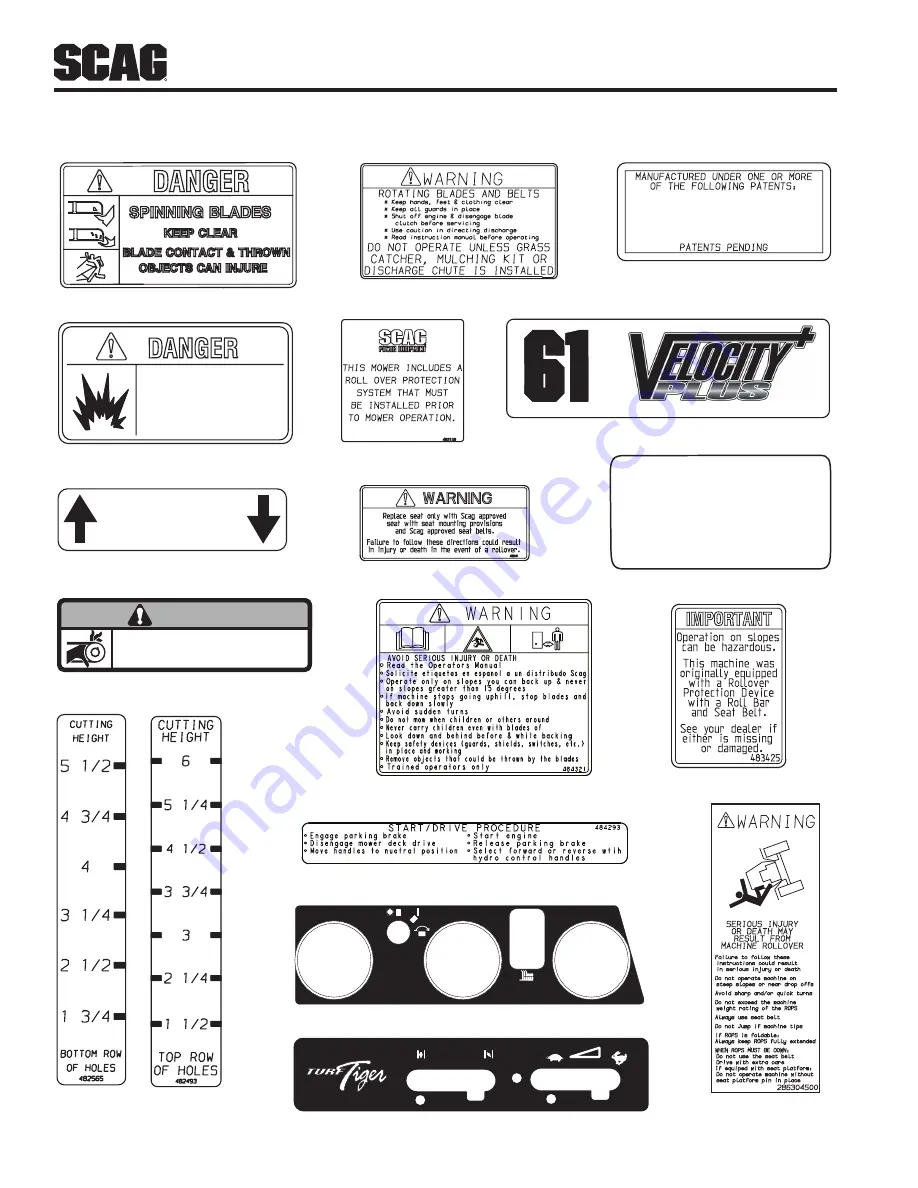
70
R
Section 8
REPLACEMENT DECALS AND INFORMATION PLATES
2
STT-DF 2011 Decals 1
10
WARNING
INSTALL BELT COVER BEFORE
OPERATING MACHINE
READ OPERATOR'S MANUAL
7
FORWARD
REVERSE
F
R
9
Heavy-Duty
Commercial
481971
13
14
1
12
6
5
8
18
4
3
__________ __________ __________ __________
__________ __________ __________ __________
__________ __________ __________ __________
__________ __________ __________ __________
11
17
CHOKE
SLOW
FAST
482983
16
483762
OFF
ON
START
MOWER DECK
PULL OUT TO ENGAGE
PUSH IN TO DISENGAGE
15
484281
Avoid injury from burns
- Shut off engine
- Allow to cool several minutes
- Remove cap slowly
- Do not overfill