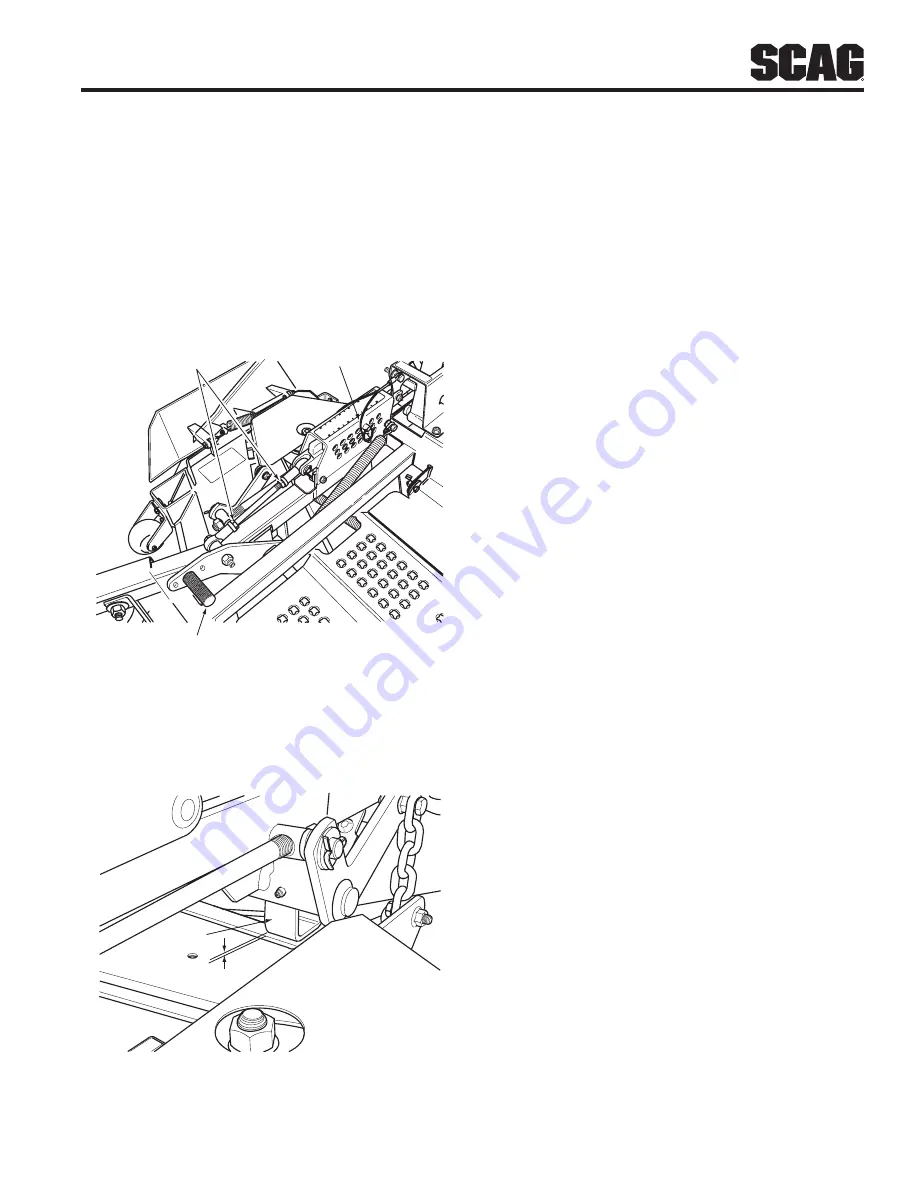
27
R
Section 6
CUTTER DECk HEIGHT
The cutter deck height adjustment is made to insure that the
cutter deck is cutting at the height indicated on the cutting
height index gauge. To check for proper deck height, be
sure that the mower is on a flat, level surface and the tires
are properly inflated.
Place the cutter deck in the transport position.
1.
Loosen the jam nuts on both ends of the deck height
control rod. (See Figure 6.7)
390S014A-2
CUTTING
HEIGHT
6
5.5
5
4.5
4
3.5
3
2.5
2
1.5
1
48
154
3
HEIGHT ADJUSTMENT PEDAL
LANYARD
PIN
LOOSEN HERE
Cutter Deck Height Adjustment
Figure 6-7.
Turn the control rod (See Figure 6.7) until there is a
2.
1/4" space between the rear deck stop and the top
of the cutter deck. (See Figure 6.8). Tighten the jam
nuts on the control rod.
1/4"
DECK
STOP
390S0175-1
Cutter Deck Stop
Figure 6-8.
Check the cutter deck cutting height by placing the
3.
lanyard pin in the 3" position on the cutting height
index. Release the deck from the transport position
and allow the deck to move to the 3" cutting height
position.
Check the measurement from the floor to the
4.
cutter blade tip. If the measurement is not at 3",
an adjustment can be made using the deck height
control rod. (See Figure 6.7)
- NOTe -
If an adjustment had to be made, be sure that the
cutter deck can easily be locked into the transport
position.