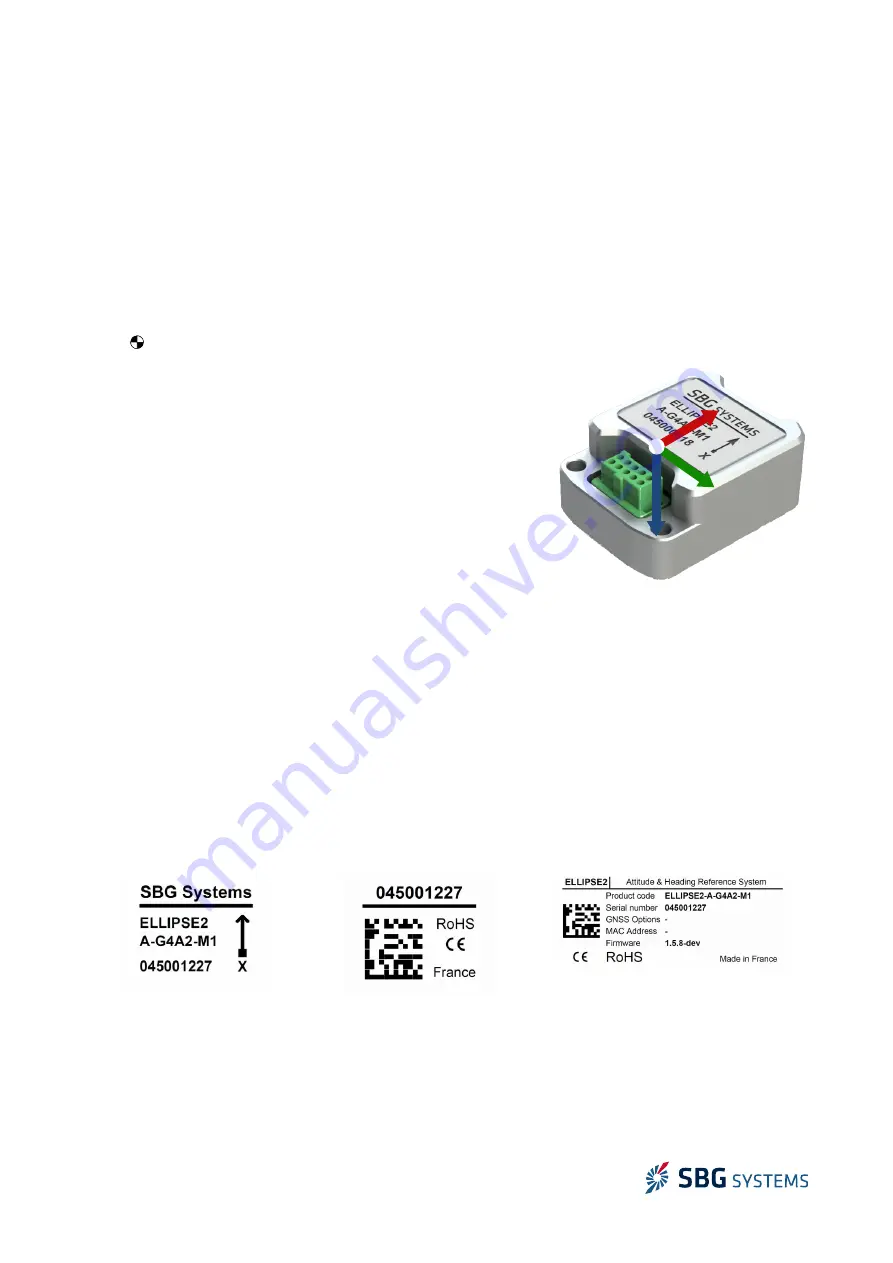
ELLIPSE2 Micro series
– Hardware Manual
ELLIPSEMHM.1.1
2.1.1. Device mechanical alignment
For best measurement accuracy, a good mechanical alignment is required. During manufacturing, the Ellipse
measurement frame has been carefully aligned to 0.1° with the base plate for roll, pitch and yaw angles.
In order to align properly the IMU frame with your own system, SBG Systems recommends the use of 3x
alignment pins, located along two perpendicular sections of the enclosure.
2.1.2. Origin of measurements
The center of measurement for acceleration, velocity and position is represented on the mechanical outlines
by the symbol. It is referenced to the base plate fine alignment hole.
2.1.3. Device coordinate frame
Device coordinate frame is identified on the product by the axis X
direction.
The whole coordinate frame is as explained in following diagram:
2.1.4. Device labels
SBG Systems manufacturing process is based on EN-9100 system with individual and full traceability of
every component and operation. Each Ellipse is identified by a unique serial number that can be used to
trace all operations during the product lifetime such as manufacturing, calibration, tests and repairs.
In addition to a unique serial number, a product code is used to define exactly the device type and options.
You can find on the top and bottom sides of the Ellipse micro, laser printed labels that hold all these
identification information. These labels also include a data-matrix code that encodes the device unique
serial number. Finally, the topside label identifies the IMU X axis direction.
In addition, the Ellipse packaging includes a second label that provides other useful information such as
installed firmware version.
12/26
Figure 2.4: Ellipse packaging label
sample
Figure 2.2: Ellipse device label
sample (top side)
Figure 2.3: Ellipse device label
sample (bottom side)
Figure 2.1: Device coordinate frame
X
Y
Z