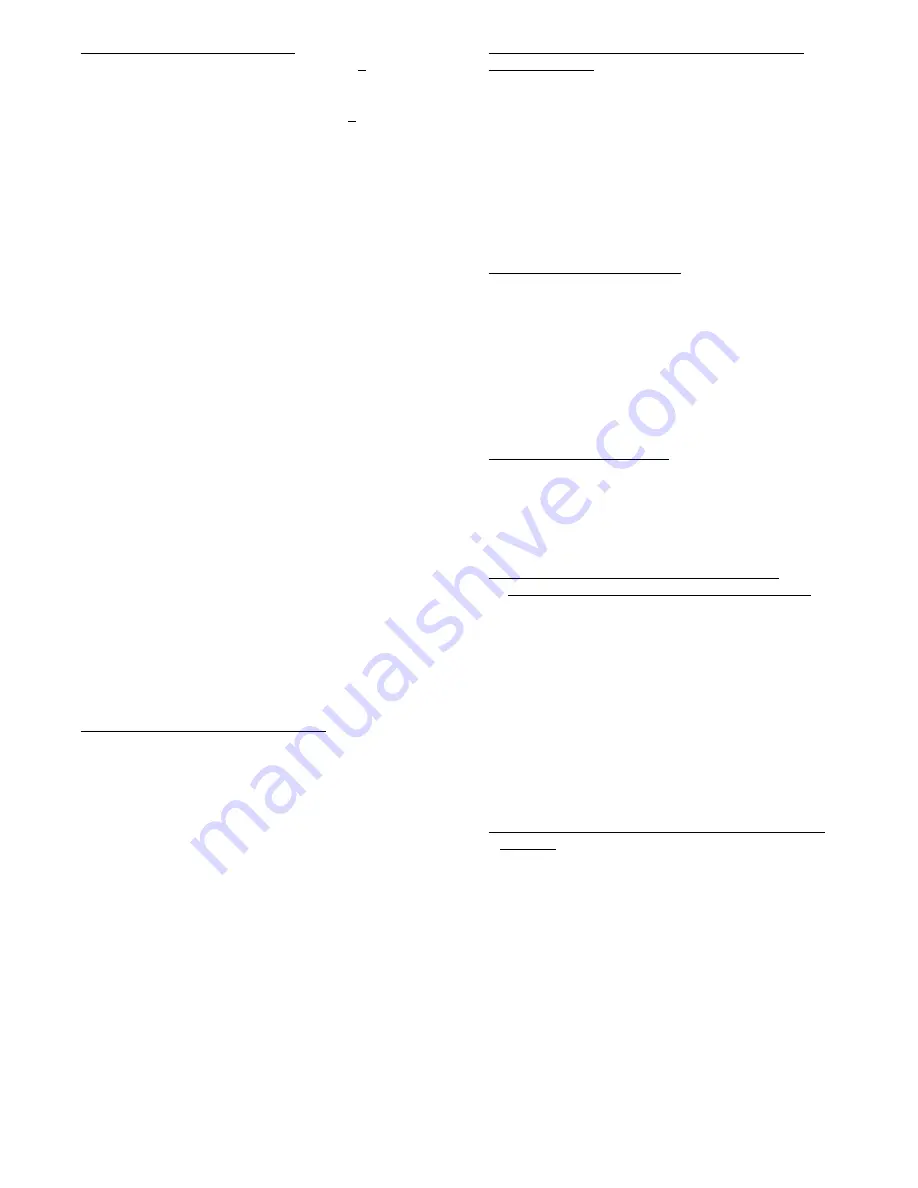
2. SPECIFICATIONS - EM-
SL100N
Rated Power Consumption........ Micro. 1450+15%W
Conv. 1200+5/-10%W
Grill
1
2
00+5/-10%W
Dual 2
600
+15%W
(After 15mins.)
Microwave Output...................... 900W
Frequency.................................. 2,450MHz ± 50MHz
Power Supply............................. 230V,50Hz
Rated Current.............................6.45+15% Amps Micro
5.3+5/-10%Amps Conv.
4.95+5/-10% Amps Grill
11.5±15% Amps Dual
(After 15mins.)
Safety Devices........................... Thermal Protector for
Magnetron, Open at135˚C.
Thermal Protector for
Cavity, Open at 122˚C.
Thermal Protector for
Heater, Open at 150˚C.
Thermal Protector for
Convection, Open at
122˚C
Fuse (Cartridge Type 8A)
Primary Interlock Switch
Door Sensing Switch
Interlock Monitor Switch
Timer.......................................... Electronic Digital
Micro,90min x 3 Stages
Convection, 90 mins
Grill, 90 mins
Oven Temperature Control.........Convection,
40˚C-250˚C
Dual,
150˚C-250˚C
Overall Dimensions......... 550(W)x487(D)x355(H)mm
Oven Cavity Size.............348(W)x345(D)x265(H)mm
Turntable Diameter.....................325mm
Net Weight..................................Approx.
23.3
Kg
3. POWER OUTPUT MEASUREMENT
(1) Prepare 1000cc tap water in a wide mouthed Pyrex
container.
(2) Stir thoroughly and note initial water temperature T1
(˚C).
(3) Place container in centre of oven and operate for 60
seconds at full power.
(4) Remove container, stir thoroughly and note final
water temperature T2 (˚C).
(5) Calculate power output= 70 x Temp. rise (T2-T1).
NOTE: This is only an approximate test method, not IEC705
test method to which the microwave oven has been tested
and rated.
4.PRECAUTIONS AND REPAIR SERVICE TIPS
PRELIMINARY
A.SINCE NEARLY 4,000 VOLTS EXIST IN
SOME CIRCUITS OF THIS MICROWAVE
OVEN, REPAIRS SHOULD BE CARRIED
OUT WITH GREAT CARE
B.TO AVOID POSSIBLE EXPOSURE TO
MICROWAVE ENERGY LEAKAGE, THE
FOLLOWING PRECAUTIONS MUST BE
TAKEN BEFORE SERVICING.
(1)Before the power is applied.
(a)Open and close door several times to make sure
the primary interlock switch, the door sensing switch,
and the interlock monitor switch operate properly.
(Listen for the clicking sound from switches). Make
sure the interlock monitor switch is closed after the
primary interlock switch is opened, when the door is
opened. (See pages 1 and 9).
(b)Make sure the perforated screen and the dielectric
choke of the door are correctly mounted.
(2)After the power is applied.
(a)Open and close the door to see if the interlock
mechanism operates properly.
(b)Check microwave energy leakage with a leakage
detector and confirm the energy leakage is below
5mW/cm
2
.
(3)Do not operate the unit until it is completely
repaired, if any of the following conditions exists.
(a)Door does not close firmly against the cavity front.
(b)The hinge is broken.
(c)The choke dielectric or the door seal is damaged.
(d)The door is bent or warped, or there is any other
visible damage to the oven that may cause
microwave energy leakage.
NOTE: Always keep the seal clean
(e)Make sure there are no defective parts in the
microwave generating and transmission assembly.
(especially waveguide).
(f)Make sure there are no defective parts in the inter
lock mechanism.
(4)Following items should be checked after the unit is
repaired.
(a)The interlock monitor switch is connected
correctly and firmly.
(b)The magnetron gasket on the magnetron is
properly positioned.
(c)Wave guide and oven cavity are intact ( no leakage
of microwave energy).
(d)The door can be properly closed and the safety
switches work properly.
(e)The oven must be stopped when the door is
opened or the time is up.
The oven must not be operated with any of the above
components removed or bypassed.
-2-