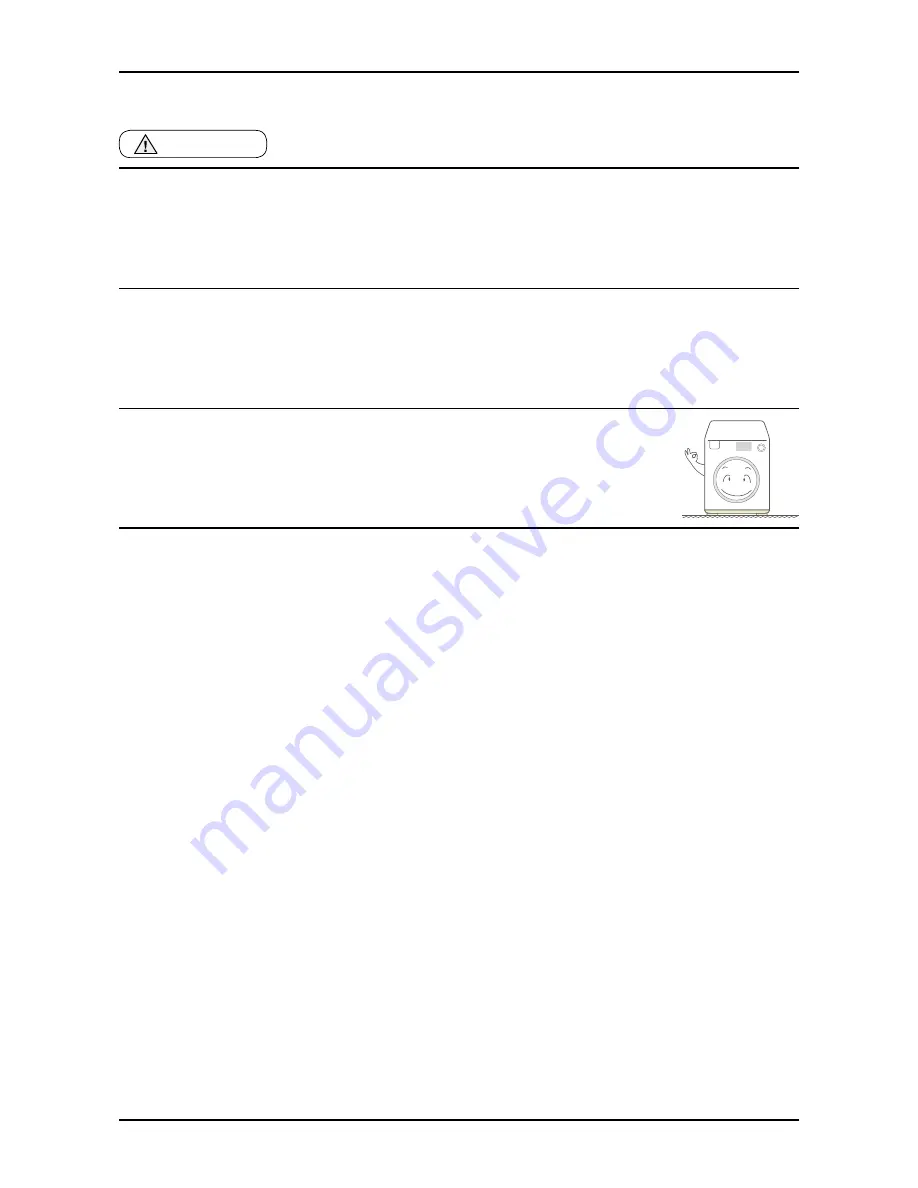
4 _ Safety Instructions
AFTER SERvICING
• Check the assembled status of the parts.
√
Now is a good time to inspect your work. Review all connections and wiring, including mounting hardware.
• Check the insulation resistance.
√
Disconnect the power cord from the power outlet and measure the insulation resistance between the power plug
and the grounding wire of the washing machine. The value must be greater than 10MΩ when measured with a
500V dC Megger.
• Check whether the washing machine is level the floor with respect to the original position
of the washing machine prior to service.
By doing this now will reduce for the need of customer dissatisfaction and redo call.
√
Vibrations can shorten the lifetime of the product.
CAuTION