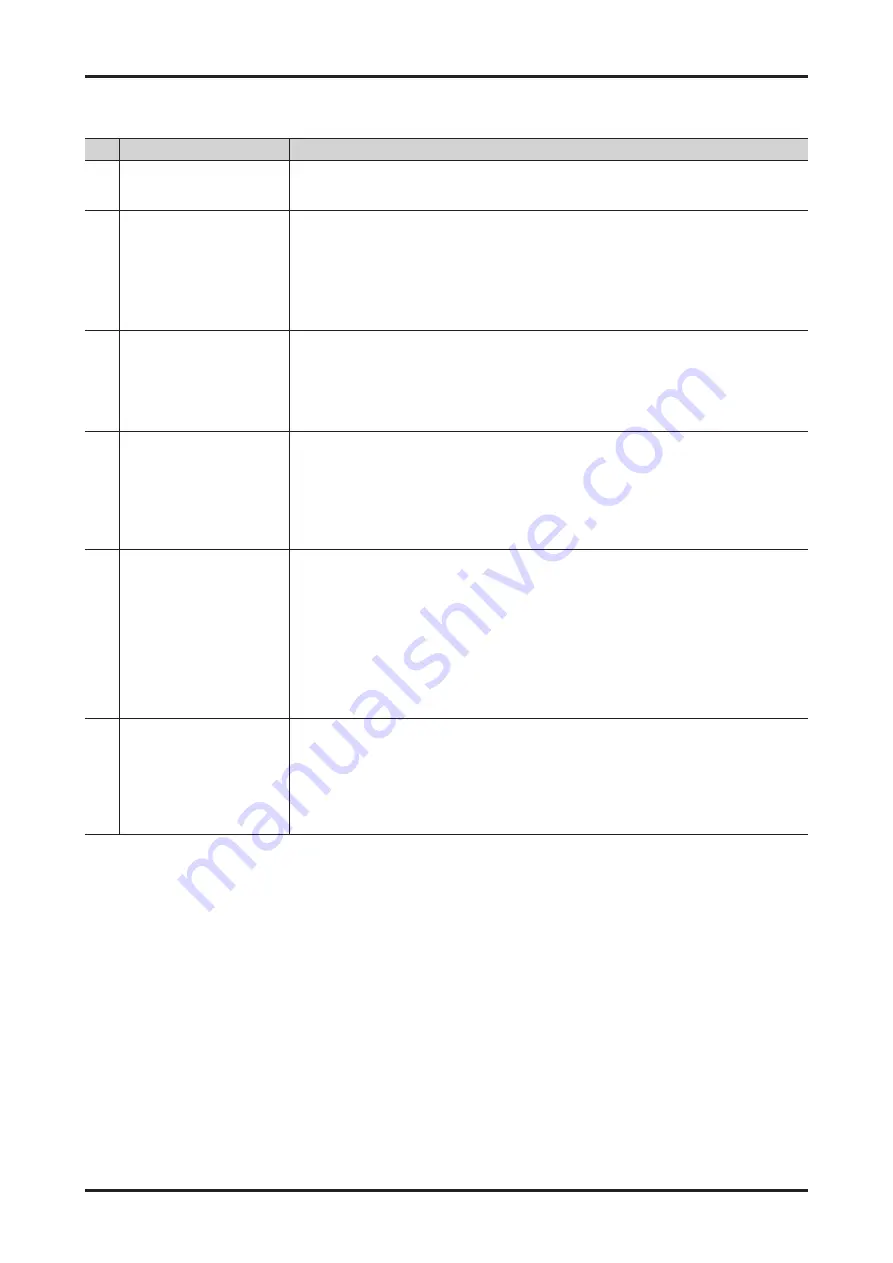
Troubleshooting _ 29
No
Problem
What to do
7
Will Not Dry Gas Model Poor
Gas Ignition
When the dryer is operated on a heat setting, the igniter should be energized and burner shall
fire within 45 seconds at 120 VAC. The failure of a component in this system will usually be
indicated by one of three symptoms (No.8, No.9, No.10)
8
The igniter does not glow
If the igniter does not heat up, remove power and using an ohmmeter, check the following:
• Open flame sensor
• Open igniter
• Shorted booster coil
• Open wiring
• Bad motor switch ( Neutral supply)
• No power from control ( L1 supply)
9
Igniter glows - No gas ignition
If the igniter heats up but the main burner flame is not ignited, remove power and using an
ohmmeter, check the following:
• Open secondary coil
• Open holding coil
• Open wire harness
• Stuck flame sensor (Stuck closed)
10
The gas is ignited but the
flame goes out
If a normal ignition takes place and after a short while the flame goes out, check for the
following:
• Radiant sensor contacts opening prematurely.
• Weak gas valve coil may open when stressed by higher Temps.
• Weak Hi-Limit
• Poor venting
• Bad drum seals
11
Improper drying clothes
wrinkled Rough texture long
dry time
• The lint filter is not clean.
• Any restriction in the exhaust.
• The outside exhaust hood damper door stuck closed.
• Is the exhaust too long, too many elbows, flex ductwork installed.
• Poor intake air available for the dryer.
• Incorrect tumbler speed. Tumbler belt slipping.
• Blower impeller bound; check for foreign material in blower area.
• Customer overloading dryer.
• Check clothing labels for fabric content and cycle selected.
• Clothes too wet due to insufficient spin out by washer.
12
Noisy and/Or Vibration
• “Thumping” Check for loose tumbler baffle, rear tumbler roller(s) worn or misaligned, out-of-
round tumbler or high weld seam on tumbler.
• “Ticking” Check for loose wire harness or object caught in blower wheel area.
• Scraping Check for front or rear bulkhead felt seal out of position or worn tumbler front
bearings.
• “Roaring” Check for blower wheel rubbing on blower housing or bad motor bearings.
• Popping or squealing sound. Check for a sticky or frayed belt.