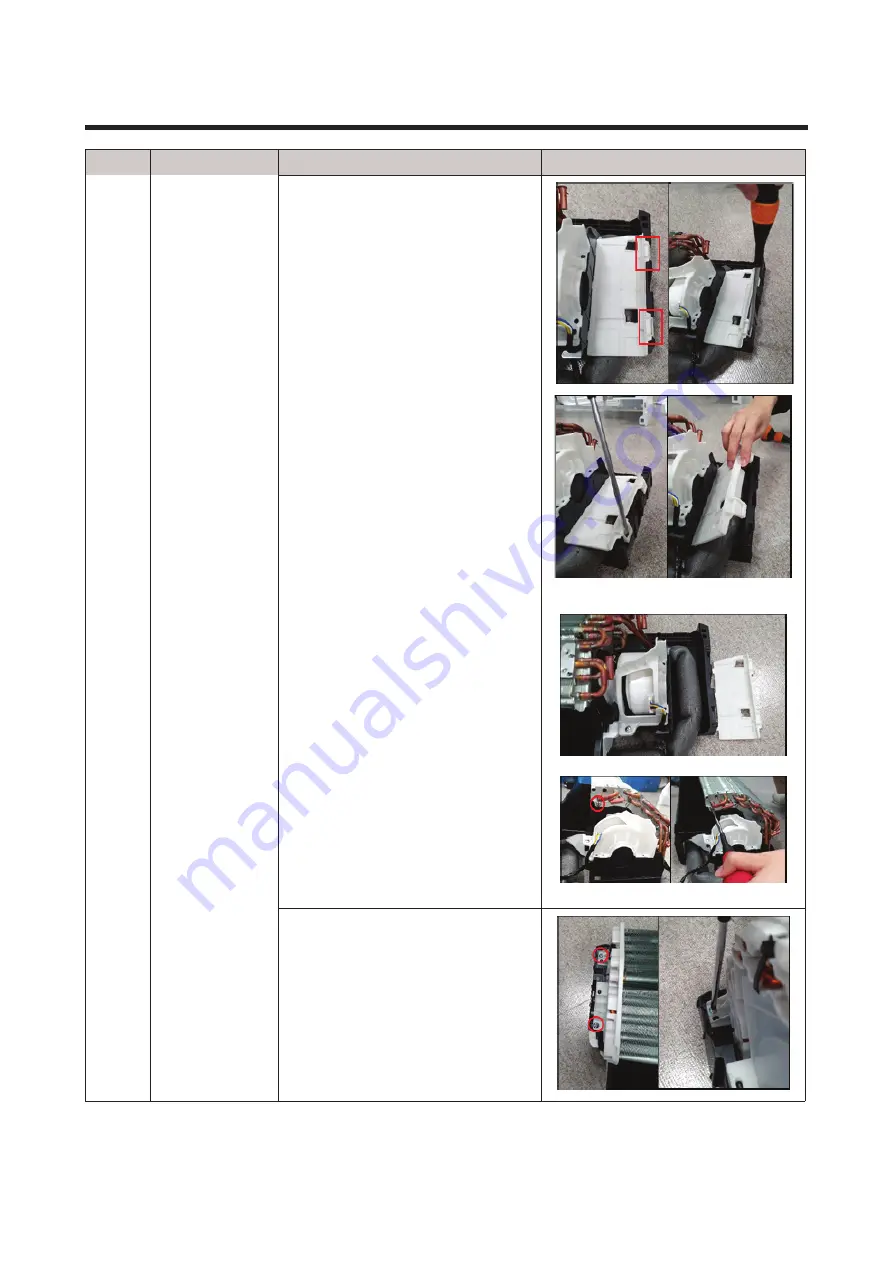
28
NO.
Parts
Procedure
Remark
7
EVAPORATOR
20) The HOLDER PIPE is fixed
to body by 2 hooks as shown in the
figure.
21) To detach the HOLDER PIPE
from the main frame,loosen 2 hook
structhres.
When separate hooks: Use the (-)
Screw Driver. Insert the (-) Screw
Driver into the gap of the hook
and lean to the Moter side as
shown in figures. (Watch out for
the damate of hooks)
22)Remove the HOLDER PIPE.
23)Unfasten a screw of the Fan
Moter side.
(Use (+) Screw Driver.)
24)Unfasten 2 screws of the
opposite side of the Fan Moter.
(Use (+) Screw Driver.)
Summary of Contents for AR09AXKAAWKNEU
Page 38: ...38 6 Wiring Diagram 6 1 IndoorUnit CODE DB68 08680A 01 ...
Page 39: ...39 6 2 OutdoorUnit CODE DB68 08682A 01 ...
Page 40: ...40 7 PCB Diagram 7 1 IndoorMain PCB CODE DB92 05042A ...
Page 41: ...41 7 2 OutdoorMain PCB CODE DB92 04837M ...
Page 42: ...42 ...
Page 43: ...43 7 3 DISPLAY PCB ...