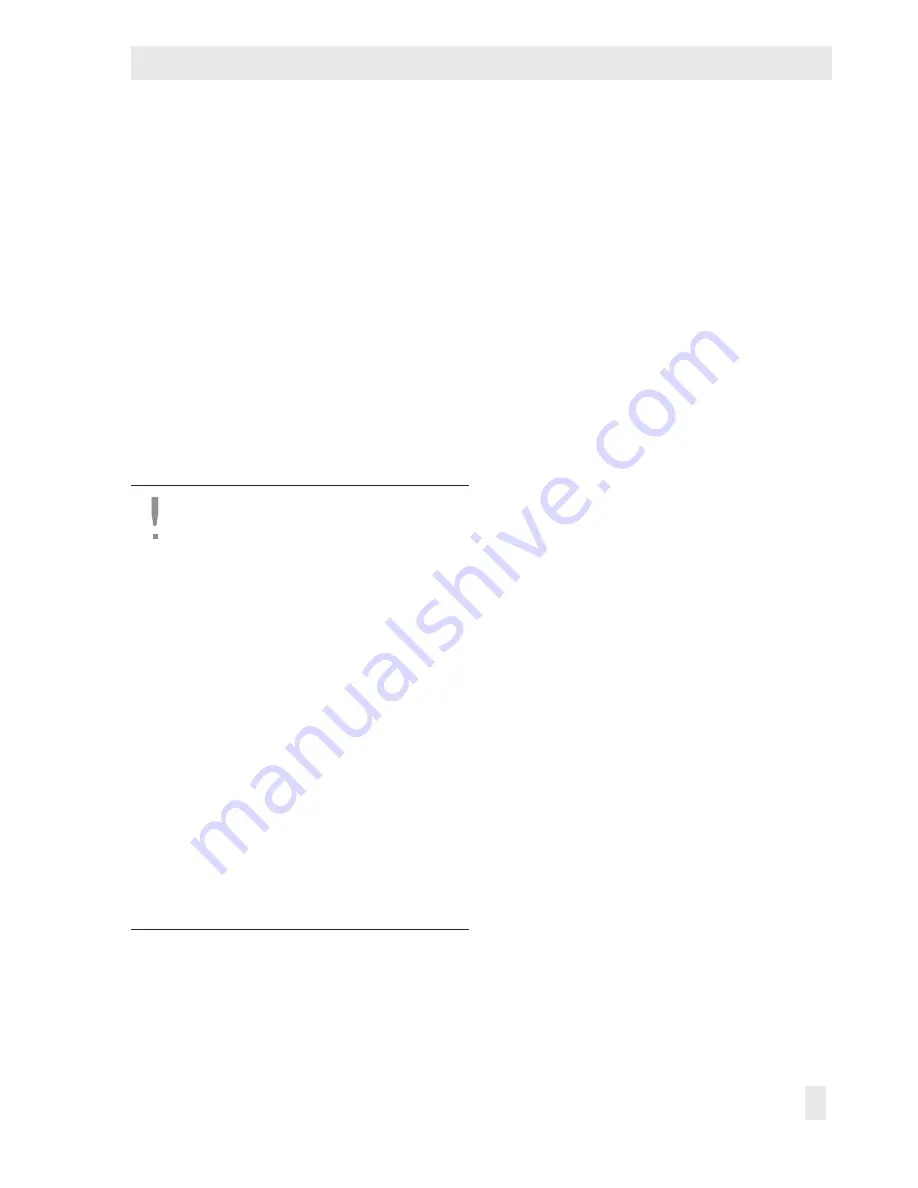
EB 8135/8136 EN
9
Installation
3
Installation
Valve and actuator are delivered ready
mounted.
Refer to the corresponding mounting and
operating instructions for more details on the
actuator used.
3.1
Mounting position
The valve can be mounted in any desired
position.
Î
Observe the restrictions for the actuator
used.
NOTICE
Install the valve free of stress and
with the least amount of vibrations as
possible. If necessary, support the
pipelines near the connections. Do
not attach supports directly to the
valve or actuator.
Pipeline routing
To ensure that the control valve func-
tions properly, the pipeline must be
straight and without any manifolds
or disturbances for a distance of at
least 6 times the valve size (DN) up
-
stream and downstream of the valve.
Contact SAMSON if this distance
cannot be observed.
Flush the pipeline thoroughly before
installation of the valve.
3.2
Arrangement of the valve
Install the valve as shown in Fig. 2 depend-
ing on whether it is to be used for mixing or
diverting service.
The plug arrangement (i.e. either mixing or
diverting valve) is indicated on a label at-
tached to the valve body.
Fail-safe action: the valve shuts off the flow
of the heating medium or opens the flow of
the cooling medium.
3.3
Strainer and bypass
We recommend installing a SAMSON
Type 2 N Strainer upstream of the valve, and
upstream of both inlet ports in mixing valves.
We recommend installing a shut-off valve
both upstream of the strainer and down-
stream of the valve to ensure that the plant
does not need to be shut down for mainte-
nance. In addition, install a bypass line.
Summary of Contents for V2001 Series
Page 26: ...26 EB 8135 8136 EN...
Page 27: ...EB 8135 8136 EN 27...