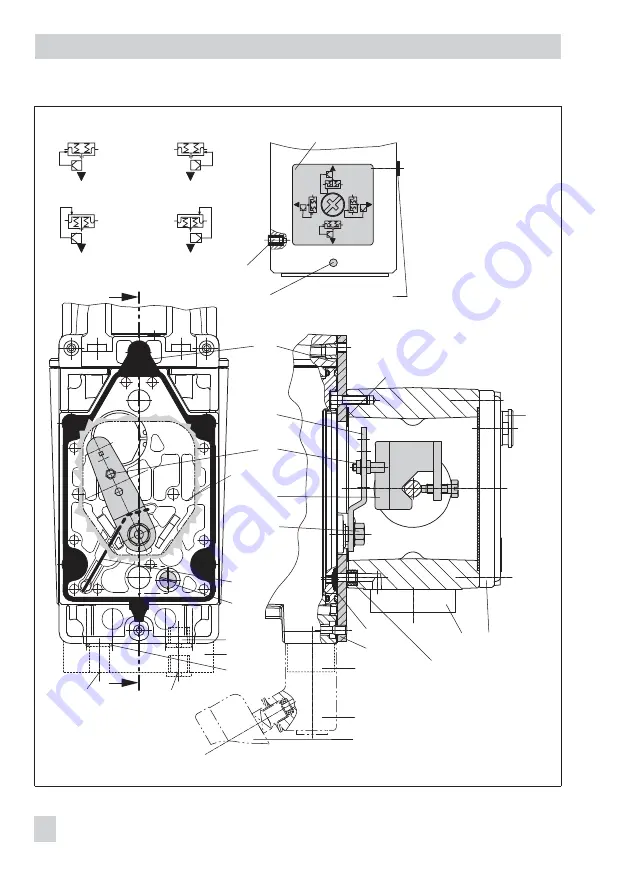
20
EB 8387-3S EN
Attachment to the control valve – Mounting parts and accessories
9
11
Supply 9
Output 38
5
6
4
17
7
6
10
10.1
3
2
1
15
6.1
1.1
1.2
14
8
11.1
A
A-A
A
Fig. 4 · Direct attachment for Type 3277-5 Actuator with 120 cm²
Switchover plate (9)
1
Lever
1.1
Nut
1.2
Disk spring
2
Follower pin
3
Follower clamp
4
Screw plug
5
Stopper
6
Connecting plate for G ¼
6.1
Seal rings
7
Pressure gauge bracket
8
Press. gauge mounting kit
9
Switchover plate
for actuator
10
Cover plate
10.1 Seal ring
11
Cover
11.1 Vent plug
14
Gasket
15
Formed seal
17
Bias spring (only with
direct attachment)
Signal pressure input
for right attachment
Symbols
Actuator stem
extends
Left attachment Right attachment
Actuator stem
retracts
Signal pressure
input for left
attachment
Signal pressure input
with brass restriction
Cut-out of
cover plate
Marking
Summary of Contents for TROVIS SAFE 3731-3
Page 5: ...EB 8387 3S EN 5...
Page 92: ...92 EB 8387 3S EN...
Page 93: ...EB 8387 3S EN 93...
Page 94: ...94 EB 8387 3S EN...
Page 95: ...EB 8387 3S EN 95...
Page 96: ...96 EB 8387 3S EN...
Page 97: ...EB 8387 3S EN 97...
Page 98: ...98 EB 8387 3S EN...
Page 101: ...EB 8387 3S EN 101...
Page 102: ...102 EB 8387 3S EN...
Page 103: ...EB 8387 3S EN 103...