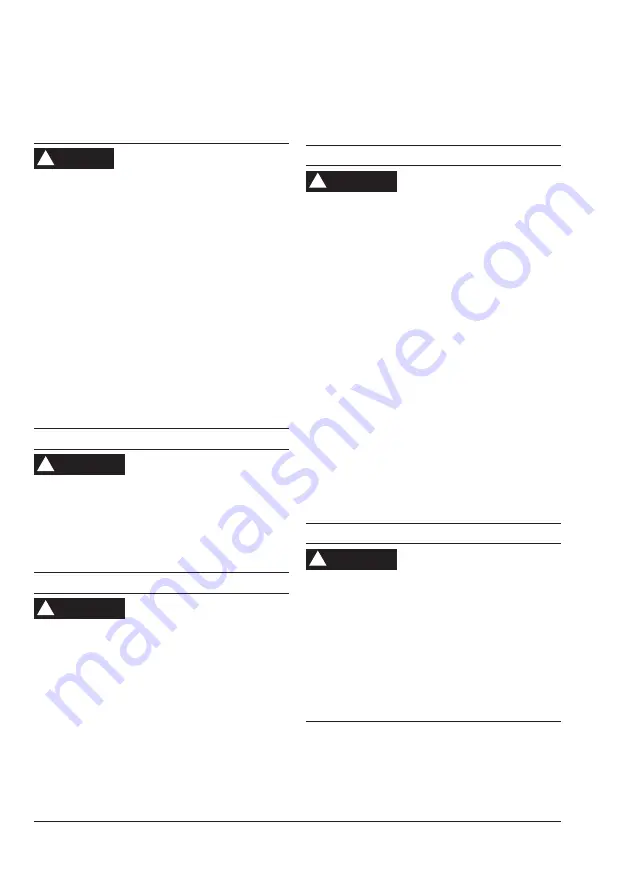
5-16
EB 8061 EN
Installation
5.4 Testing the installed valve
Risk of bursting due to incorrect opening of
pressurized equipment or components.
Valves and pipelines are pressure equipment
that may burst when handled incorrectly.
Flying projectile fragments or the release of
process medium under pressure can cause
serious injury or even death.
Before working on the control valve:
Î
Depressurize all plant sections affected
and the valve (including the actuator).
Release any stored energy.
Î
Drain the process medium from all the
plant sections concerned as well as the
valve.
Risk of personal injury due to pressurized
components and process medium being
discharged.
Î
Do not loosen the screw of the test con-
nection while the valve is pressurized.
Risk of hearing loss or deafness due to loud
noise.
Noise emission (e.g. cavitation or flashing)
may occur during operation caused by the
process medium and the operating
conditions. Additionally, a loud noise may
briefly occur through the sudden venting of
the pneumatic actuator or pneumatic valve
accessories not fitted with noise-reducing
fittings. Both can damage hearing.
Î
Wear hearing protection when working
near the valve.
Crush hazard arising from actuator and
plug stem moving.
Î
Do not insert hands or finger into the
yoke while the air supply is connected to
the actuator.
Î
Before working on the control valve,
disconnect and lock the pneumatic air
supply as well as the control signal.
Î
Do not impede the movement of the actu-
ator and plug stem by inserting objects
into the yoke.
Î
Before unblocking the actuator and plug
stem after they have become blocked
(e.g. due to seizing up after remaining in
the same position for a long time), re-
lease any stored energy in the actuator
(e.g. spring compression). See associat-
ed actuator documentation.
Risk of personal injury due to exhaust air
being vented.
While the valve is operating, air is vented
from the actuator, for example, during
closed-loop operation or when the valve
opens or closes.
Î
Wear eye protection when working in
close proximity to the control valve.
DANGER
!
WARNING
!
WARNING
!
WARNING
!
WARNING
!
WARNING
!
WARNING
!
Summary of Contents for EB 8061 EN
Page 28: ...3 14 EB 8061 EN...
Page 34: ...4 6 EB 8061 EN...
Page 80: ...12 2 EB 8061 EN...
Page 82: ...13 2 EB 8061 EN...
Page 84: ...14 2 EB 8061 EN...
Page 85: ...EB 8061 EN 14 3...
Page 86: ...14 4 EB 8061 EN...
Page 91: ......