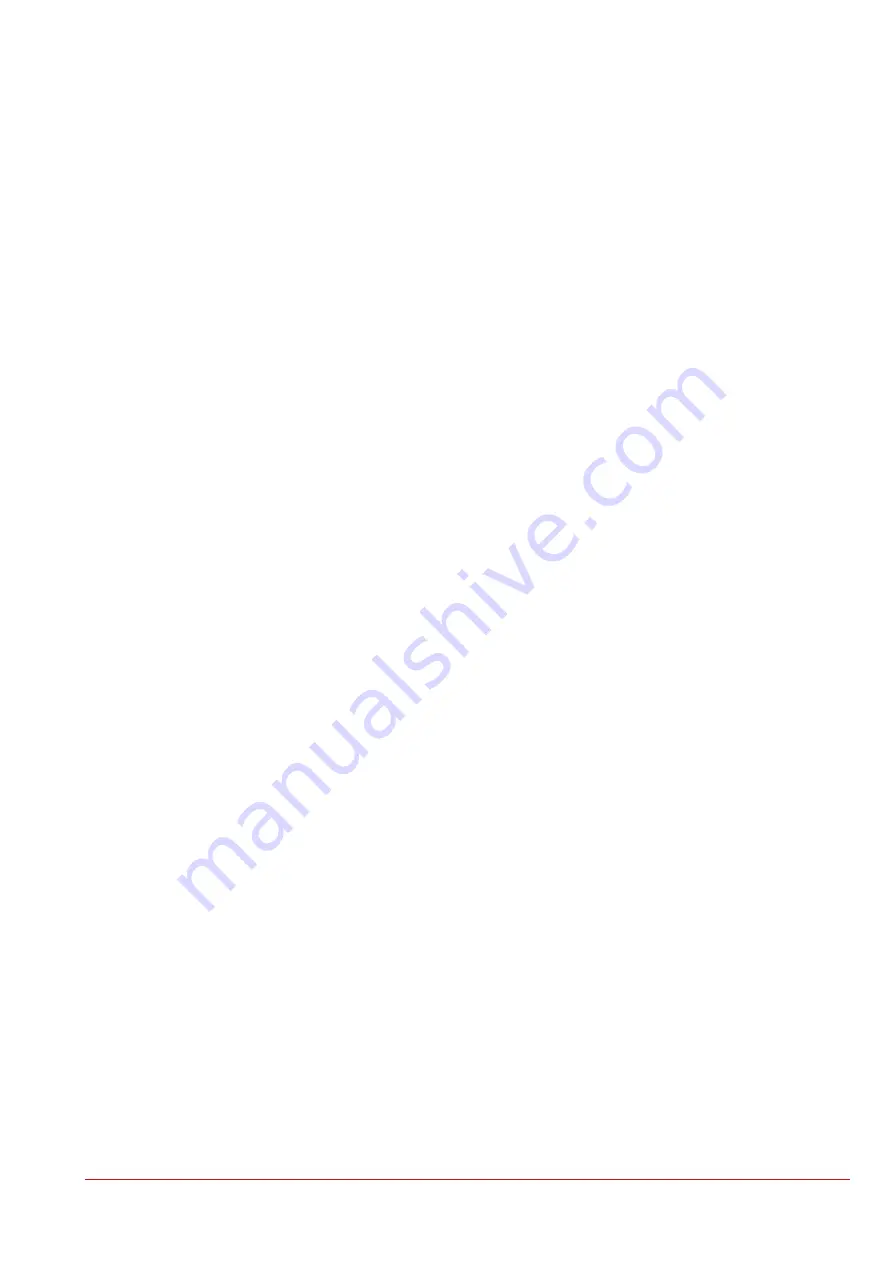
1-1
EB 31a_EN
December 2022 edition
Subject to technical changes
Safety instructions and safety measures
1
Safety instructions and safety measures
Intended use
The PFEIFFER-rotary actuator BR
|
31a Edition
|
2010 is intended
for the actuation of an installed control valve, ball valve or other
actuation with a rotating throttle housing. Together with the valve,
the rotary actuator is used to cut off
fl
uid, gaseous or vaporous
media in pipes. The rotary actuator is suitable for control tasks or
ON/OFF operation. The rotary actuator can be used in process
technology and industrial plants.
The rotary actuator is designed for precisely de
fi
ned conditions
(e.g. signal pressure, torque, opening angle, direction of turning
and action). Therefore the operator must make sure that the rota-
ry actuator is only used when the conditions of use comply with
the design criteria de
fi
ned in the order. If the operator would like
to use the actuator in other applications or environments, they
must contact PFEIFFER.
PFEIFFER shall not be held liable for damage that result from
non-compliance with the intended use, as well as for damage
that results from external forces or external in
fl
uences.
Ö
Limits of use, areas of use and possible uses can be found in
the technical data and on the type plate.
Reasonably foreseeable erroneous use and unintended use
The rotary actuator is not suited for the following areas of use:
−
Use outside of the technical data and the limits de
fi
ned by the
design.
−
Use outside of the limited de
fi
ned by the attachments installed
on the rotary actuator.
−
Use in a corrosive environment with unsuitable protection.
Furthermore, the following activities are considered unintended
use:
−
Use of third-party spare parts.
−
Disassembly of individual spring cartridges.
−
Performance of maintenance and repair work that is not de-
scribed.
Quali
fi
cation of operating personnel
The rotary actuator may only be disassembled, dismantled, as-
sembled and commissioned by specialist personnel who are fa-
miliar with the assembly, commissioning and operation of this
product.
−
Specialist personnel in terms of this installation and operating
manual are persons who, on the basis of their vocational ed-
ucation, knowledge and experience and knowledge of the
relevant standards, are capable of evaluating the assigned
tasks and identifying possible hazards.
Personal protective equipment
PFEIFFER recommends the following protective equipment when
handling the pneumatic rotary actuator BR
|
31a:
−
Protective gloves and safety shoes during assembly and dis-
assembly of the actuator.
−
Eye protection and hearing protection when operating the ro-
tary actuator.
Ö
Request additional protective equipment from the plant oper-
ator.
Changes and other modi
fi
cations
Changes, conversions and other modi
fi
cations to the product are
not permitted without consulting PFEIFFER. Non-compliance in-
validates the product guarantee. PFEIFFER shall not be held liable
for any resulting property damage or personal injury.
Protective devices
On their own, PFEIFFER pneumatic rotary actuators do not have
any particular protective devices.
In the case of a power supply failure, the rotary actuator auto-
matically switches to a certain fail-safe position.
−
The fail-safe position corresponds to the direction of action
and is indicated on the type plate of PFEIFFER rotary actua-
tors, see chapter “2.1 Type plate of the actuator”.
Warning of residual risks
To prevent personal injury or property damage, the operator and
operating personnel must use suitable measures to prevent the
hazards that can result from the signal pressure, tension energy
of the springs and moving parts of the rotary actuator.
−
Therefore, the operator and operating personnel must ob-
serve all the hazard information, warning information and
information in this installation and operating manual.
Obligation of the operator to exercise diligence
The operator is responsible for proper operation as well as com-
pliance with the safety regulations.
−
The operator is responsible for providing operating personnel
with this installation and operating manual as well as the ap-
plicable documents and to provide instructions on proper op-
eration.
−
Furthermore, the operator must ensure that operating person-
nel and third parties are not endangered.
−
It is not the responsibility of PFEIFFER and therefore when us-
ing the rotary actuator make sure that the rotary actuator is
only used as intended as described in this chapter.
−
These instructions do not replace the safety and work instruc-
tions provided by the operator. In the case of con
fl
icts be-
tween these instructions and the procedure de
fi
ned by the op-
erator, the differences shall be clari
fi
ed in writing between an
authorised representative of the operator and an authorised
representative of PFEIFFER.
Summary of Contents for EB 31a
Page 6: ...EB 31a_EN December 2022 edition Subject to technical changes Content...
Page 32: ...6 2 EB 31a_EN December 2022 edition Subject to technical changes Start up...
Page 34: ...7 2 EB 31a_EN December 2022 edition Subject to technical changes Operation...
Page 42: ...9 6 EB 31a_EN December 2022 edition Subject to technical changes Servicing...
Page 44: ...10 2 EB 31a_EN December 2022 edition Subject to technical changes Decommissioning...
Page 52: ...13 2 EB 31a_EN December 2022 edition Subject to technical changes Disposal...
Page 54: ...14 2 EB 31a_EN December 2022 edition Subject to technical changes Certificates...
Page 55: ...14 3 EB 31a_EN December 2022 edition Subject to technical changes Certificates...
Page 56: ...14 4 EB 31a_EN December 2022 edition Subject to technical changes Certificates...
Page 67: ...EB 31a_EN December 2022 edition Subject to technical changes...