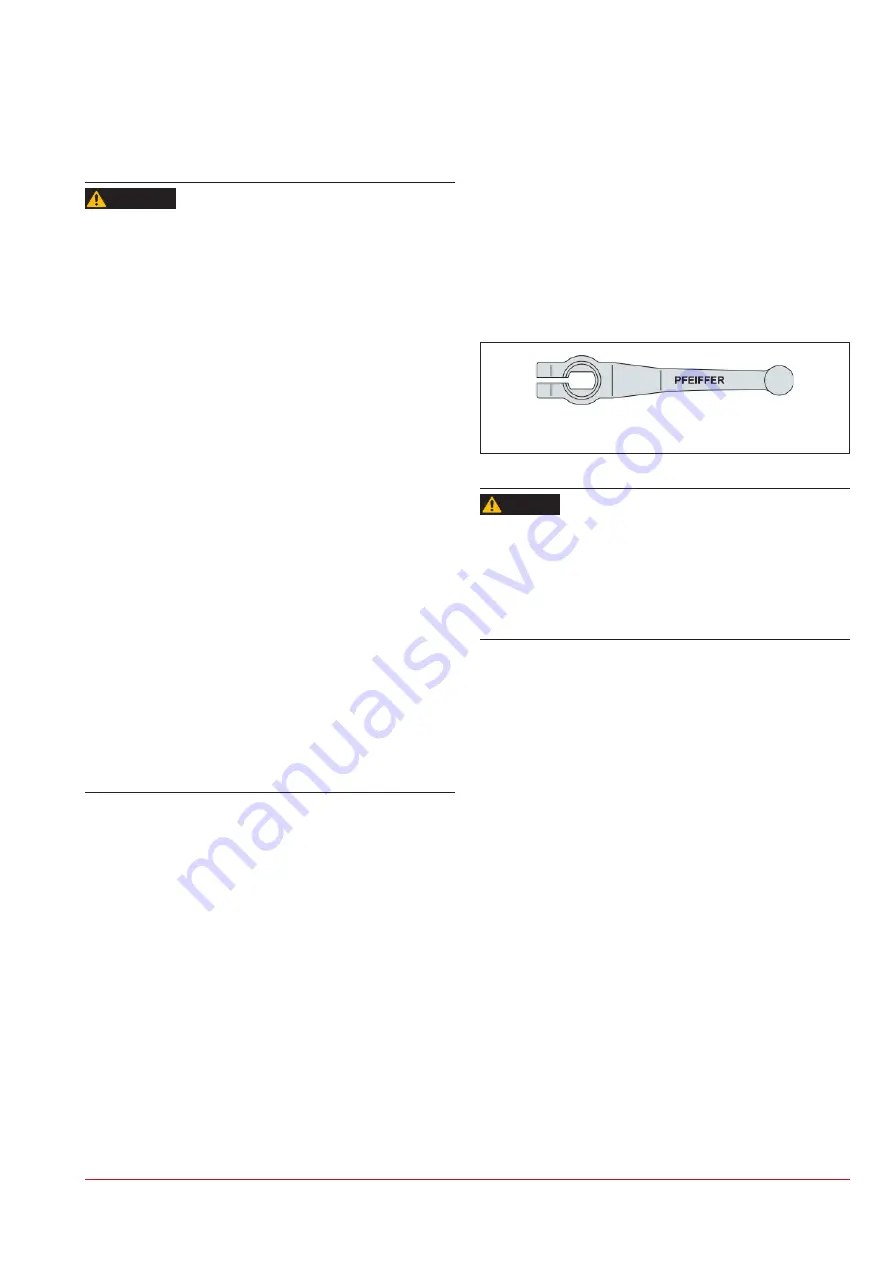
7-1
EB 20a_EN
November 2023 edition
Subject to technical changes
Operation
7 Operation
As soon as the commissioning/recommissioning work is com-
plete, see Chapter “6 Commissioning”, the ball valve is ready for
operation.
Danger of burning due to hot or cold components and pipe!
Ball valve components and pipes can become very hot or very
cold during operation and cause burns upon contact.
Ö
Let the components and pipes cool down or warm up.
Ö
Wear protective garments and protective gloves.
Danger of injury due to pressurised components and escaping
medium!
Ö
Do not loosen the screw of the optional test connection while
the ball valve is pressurised.
Danger of crushing due to moving actuator- and control shafts!
Ö
Do not reach into the bracket as long as the pneumatic pow-
er is connected to the actuator.
Ö
Before working on the ball valve, interrupt and lock pneumat-
ic energy and the control signal.
Ö
Vent the actuator.
Ö
Do not allow the jamming of objects in the bracket to hinder
the operation of the actuator- and control shaft.
Ö
If the actuator- and control shaft are blocked (e.g. due to
“seizure” if not actuated for a long period of time”), release
the residual energy of the actuator (spring tension) before re-
leasing the blockage, see the corresponding actuator docu-
mentation.
Ö
Prior to disassembly of the actuator, bring the ball valve into
the fail-safe position.
Danger of injury due to escaping exhaust air!
During operation, when regulating or when opening and closing
the ball valve, exhaust air can escape, for example from the ac-
tuator.
Ö
Wear eye protection and, if necessary, hearing protection
when working near valves.
Observe the following points during operation:
Ö
The PTFE plastic sealing surfaces tend to
fl
ow. After commis-
sioning and reaching the operating temperature, tighten the
body screws with the corresponding tightening torques, see
Table 15-1 in Chapter “15.1.1 Tightening torques”.
Ö
Tighten all
fl
ange connections between the pipe and ball
valve, if necessary, with the corresponding tightening torques
according to Table 15-2 or Table 15-3 in Chapter “15.1.1
Tightening torques”.
Ö
The ball valve/actuator unit must be actuated with the control
signals.
WARNING
Ö
Ball valves that were delivered from the factory with an actu-
ator are precisely adjusted. The user is responsible for any
changes they make.
−
For the manual operation or manual override of the actuator
(if present), normal manual forces are suf
fi
cient and the use
of extensions to increase the actuation torque is not permit-
ted.
−
In the case of ball valves with a hand lever, the position of the
hand lever indicates the location of the bore in the ball. The
hand lever moves in general parallel to the bore. Special ver-
sions are to be taken from the respective order.
–
Hand lever 90° transverse to the pipe: Ball valve closed.
–
Hand lever parallel to the pipe: Ball valve open.
Figure
|
7-1:
Hand lever
Danger of injury due to jerky operation of the ball valve!
The failure to observe these warnings can cause extreme danger
for persons or for the pipe system.
Ö
Do not open and close the ball valve suddenly to prevent
pressure surges and/or a temperature shock in the pipe sys-
tem.
−
If a ball valve leaks, observe chapter “8 Faults”.
DANGER
Summary of Contents for BR 20a
Page 28: ...6 2 EB 20a_EN November 2023 edition Subject to technical changes Start up...
Page 30: ...7 2 EB 20a_EN November 2023 edition Subject to technical changes Operation...
Page 36: ...10 2 EB 20a_EN November 2023 edition Subject to technical changes Decommissioning...
Page 38: ...11 2 EB 20a_EN November 2023 edition Subject to technical changes Removal...
Page 44: ...13 2 EB 20a_EN November 2023 edition Subject to technical changes Disposal...
Page 46: ...14 2 EB 20a_EN November 2023 edition Subject to technical changes Certificates...
Page 47: ...14 3 EB 20a_EN November 2023 edition Subject to technical changes Certificates...
Page 48: ...14 4 EB 20a_EN November 2023 edition Subject to technical changes Certificates...
Page 49: ...14 5 EB 20a_EN November 2023 edition Subject to technical changes Certificates...
Page 50: ...14 6 EB 20a_EN November 2023 edition Subject to technical changes Certificates...
Page 59: ...EB 20a_EN November 2023 edition Subject to technical changes...